YR series slip ring asychronous motor
Brand Name:NEW HENGLI | Model Number:YR800 | Type:Asynchronous Motor | Frequency:50 |
Output Power:6000 | Protect Feature:Drip-proof | Phase:Three-phase | Certification:GB755 |
AC Voltage:6KV | Place of Origin:Zhejiang China (Mainland) | Efficiency:IE 2 | HOT!:NEW ! |
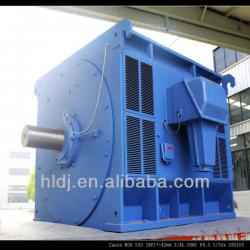
Hangzhou Hengli Electric Machine MFG. Co., Ltd
The Tendentious Reference for High Voltage AC Motor Series Product
To comply professional standard and meet customers’ requests,various ofHigh Voltage A.C.Motor produced by our companyhave been largely improved itsperformancestabilities and reducedmaintenance fee. Fordifferent industrialconditions, we supplyourmature products with excellent and efficient quality.Different kinds of environments, protection class, winding and mounting methods could be chosen. With typical and mature design and processing technology, our products hold the following technical characteristics:
- Excellent main structure and frame protection.
Y Series (incl. series YKK,YKS and other exclusive-use cage rotors); series YR (incl. YRKK,YRKS derivated rotor-wind motors), main structure (like stator, terminal box, bearing, end shield, etc) could satisfy corresponding frame protection class requests from the customers.
IP23 (Drop-proof Type): Suits Non-hazardous indoor use without powder and dust matching water pumps and fans.
IP54 ( Totally Enclosed Type): Suits badly environments , such as cement making, steel rolling, sugar mill, mining machine ( conveyor, crusher), coal mill, cement rotary furnace, rolling mill (piercing mill, blooming mill), which meets protective demand for electric power, water pump, exhaust fan , blower and powder exhauster,etc.
Motor frames are made of all-steel armor plate, to be bended, formed and welded.Without hatch or lid, dustproof capacity and bright advantages come out. Electrode rings and their shells are fixed outside the frame. Coaxial cooling fan is fixed inside its shell, efficiently improve interior heat dissipation conditions and avoid carbon powder gathering, which improves performance of greater stable.
For easily replacement, brush screws are fixed on the backside of conducting rings. Viewing windows are easily for the user to see whether brushes run and wear well.
Customers could choose different cooling methods for both main structure and collector rings. Normally we choose the same methods, but we could also choose different methods for practical use. For example, IP54 for main structure and IP23 for rings are also workable.
1.1 High efficient and reliable insulation system
We use a series of key technologies for special insulation, such as self-bonding mica tape covered rectangle winding wire, impregnated under VPI holistic vacuum press, resisted corona by two classes, ensuring stable dielectric performance and excellent heat dissipation.
Standard 6kv product adopts polymide-imide film covered winding wire and insulated with mica tape for coils and VPI impregnated structure for stator.
High voltage converter motor takes corona resistance sintering line as winding turn-to-turn insulation so as to against infections caused by high frequent switches of convert source.
Wound rotor coil adopts rolling package insulation construction and thermal solidification forming. Imbedded coils are hard brazed. Two-time impregnating process reinforces insulation strength, system humidity prevention and dustproof capacity of the rotor.
1.2 Perfect mechanical strength of the shaft
Aiming to different load, shaft adopts spider-weld structure which provide enough support, torque rigidity and mechanical strength. Regarding impact load, good-quality alloy steel is used.
1.3 Rolling bearing structure:
According to usage requests, greased rolling bearing and slide bearing inside end shields are used (depends on different requests). Bearing takes helical and sealing structure.
1.4 Precise main and auxiliary terminal boxes.
Made of integral stretched cold-roll steel board, high voltage motors takes faults decompression structure and earthing protection ends both interior and exterior.
1.5 Fully established indication boards.
Indication boards for turning direction, terminal boxes, lubrications, which provides convenience for fixing and maintenance.
2. AC motor technology, techniques and main equipment capacity:
2.1 Resources and technical guarantee:
2.1.1The professional technician team:
We recruited senior engineering technicians for products development who used to work in famous motor manufacturers in China. They grasp advanced technology and congener product development trend in the world. With rich and several decades of expert manufacturing experiences and developing capacity for all sorts of A.C. motor, they are able to satisfy different kinds of environments and using conditions, electricity source, load characteristics, supervise system, and protection and so on.
2.1.2Mechanical processing:
We possess large lathe, large horizontal lathe, large digital face boring mill, large round exterior mill, large metal cutting capacity in process center and with the largest fix lifting capacity up to 60t.
2.1.3 Punching tapes (laminated core) productionacquires Numerical wire controlled cutter,
High speed groover, 315t of Four-pole double-act hydraulic roller, 200t of Open fixed pressure puncher, Vertical-compound hydraulic roller: 200t, height:2200mm.
2.1.4Coil productionadopts Semiautomatic circle winding wrapper with constant stretch.
2.1.5Insulation processingadopts Vacuum press impregnant system (VPI-42: 4200X3500mm)
2.1.6Cage/wound rotor medium conversional inductive welding process equipment.
2.1.7Inspection and test
Power frequency voltage resistance device with highest power frequency test voltage 33Kv
Turn-to-turn current resistance test device with capacity of 2000kVA
Electrical source test system with highest test voltage: 14000V
Test device with largest voltage 13.8kV
Frequency converter electrical source test system with test capacity:1-120Hz,
Converter test electrical source system and computer data collection and processing with 6000KVA
Underpropped dynamic balancer with biggest working quality:7500kg( Shanghai Shen Ke)
Portable micro computer dynamic balancer:
2.2 Design and development capacity:
2.2.1Electromagnetism design:
We have plenty of international A.C. motor development software, which could be used for calculation and analysis of the electromagnetism.
2.2.2Mechanical design:
We adopt from KMSOFT company’s PDM system KMCAD and CAPP collection as our design and management platform to make design and management standard, fast , efficient, secure, and stable.
2.3 Main processing techniques and quality guarantee.
Core parts of H.V A.C. motor like coils, stator cores, shaft welding, frame and insulation processing are done all by ourselves. The key materials selection and purchasing follows strictly to below procedures:
Design- Techniques- Purchasing-Inspection when delivered to our factory
The main materials suppliers are managed classificated according to warranty system and all pass qualified supplier attestation procedure.
Main parts processing technics are introduced as follows:
a). Stator coil production:
According to demands of different voltage, corresponding insulation for stator coils is used, we use insultation materials to wrap, wind and form coil made from rectangle copper wires. With internal technology development, we adopt dominate insulations with little glue powder mica belt continuously winding insulation.
b). Insulation process:
To satisfy the insulation design requirements, the insulators are of excellent voltage endurance, heat aging and mechanical strength. Meanwhile, insulation epoxy without solvent produced by domestic excellent suppliers is adopted, together with VIP impregnated process makes motors with perfect F class insultations
c) Iron core production:
Laminated steel for stator and rotor made of 50W470 high quality nondirectional cold-rolled silicon steel board with low wastage and high magnetoconductivity, to avoid laminating error , an auto device are used for changing tapes directions; fulfill grooves by high speed grooving machine.
d) End rings welding:
To acquire advanced weld equipment and technology, the most importance for copper-bar rotor is to use microcomputer controlled intermediate frequent induction welding equipment.
e) Aluminum die cast for rotor:
As to different use conditions, we have different design structures for cage rotor.
f) Coil manufacturing for wound rotor:
TBR flat copper bars are used for wound rotor asynchronous motor. Mica film wrapped insulation technology is processed after coil forming
g). Structure components processing:
Vibratory aging and electric annealing processing is used for motor frame, spider-welded shaft and all casting parts, which could decrease distortion caused by remaining stress and provide stable performance of the motor.
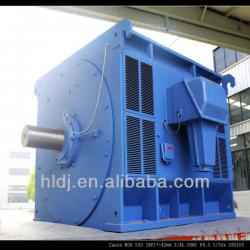
Packaging Detail:STANDARD EXPORT PACKING |
Delivery Detail:60 DAYS |