Ultrasonic welding machine for auto door trim
Place of Origin:Jiangsu China (Mainland) | Brand Name:KEBER | Model Number:KEBER-UL2535 | Voltage:380V/415V |
Power:5000W | Frequency:30KHz/40KHz | Welding Area:According to the products | Dimensions:Can design according to the products |
Weight:3500kg | Usage:Weld auto door panel | Can design according to the products:Use high devices |
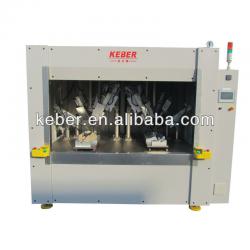
About ultrasonic welding:
Ultrasonic plastic welding is the joining or reforming of thermoplastics through the use of heat generated from high-frequency mechanical motion. It is accomplished by converting high-frequency electrical energy into high-frequency mechanical motion. That mechanical motion, along with applied force, creates frictional heat at the plastic components' mating surfaces (joint area) so the plastic material will melt and form a molecular bond between the parts. The following drawings illustrate the basic principle of ultrasonic welding.
Welding The basic principle of ultrasonic welding
Step 1 - Parts in fixture
The two thermoplastic parts to be assembled are placed together, one on top of the other, in a supportive nest called a fixture.
Step 2 - Horn contact
A titanium/steel or aluminum component called a horn is brought into contact with the upper plastic part.
Step 3 - Pressure applied
A controlled pressure is applied to the parts, clamping them together against the fixture.
Step 4 - Weld time
Step 5 - Hold time
The clamping force is maintained for a predetermined amount of time to allow the parts to fuse as the melted plastic cools and solidifies. This is known as hold time. (Note: Improved joint strength and hermeticity may be achieved by applying a higher force during the hold time. This is accomplished using dual pressure.)
Step 6 - Horn retracts
Once the melted plastic has solidified, the clamping force is removed and the horn is retracted. The two plastic parts are now joined as if molded together and are removed from the fixture as one part.
Plastics assembly is a fast, clean, efficient, and repeatable process that consumes very little energy. No solvents, adhesives, mechanical fasteners, or other consumables are required, and finished assemblies are strong and clean.
The horn is vibrated vertically 15,000(15KHz)20,000 (20 kHz) or 30,000 (30 kHz) times per second, at distances measured in thousandths of an inch (microns), for a predetermined amount of time called weld time. Through careful part design, this vibratory mechanical energy is directed to limited points of contact between the two parts.
The material of ultrasonic horn include alumium alloy,titanium alloy and steel,it’s according to the products and requirements.The horn and fixture design according the 3D drawing of the product.
Advantages And Benefits Of The Plastic Welding Process
Using ultrasonic plastic welding, no adhesives, screws, connective bolts or soldering materials are necessary. The possibilities for ultrasonic applications are broad. The process is very fast (less than one second) and can be automated very easily. The machines can be installed anywhere since no exhaust or heat has to be removed and therefore no ventilation system is required. The applied heat occures only in the joining area, avoiding any temperature changes or surface damage to the plastic parts. The joints are repeatable, clean and precise.
KEBER ultrasonic welding process advantages
KEBER provide 15,20,30,40KHz frequency ultrasonic systems,and we also cooperate with Japan manufactures,we can give the customer many different choice.We have strong R&D team to provide ultrasonic welding solutions.We also have our own CNC center to manufacture the fixture and horn,so we can provide high efficiency with good price.
Ultrasonic welding machine:KEB-1522 /KEB-1526/ KEB-2010 /KEB-3010
Hot plate welding machine:KEB-5030/KEB-6550/Horizontal hot plate welder/Servo motor hot plate welder/Hydraulic hot plate welder

Packaging Detail:wooden case |
Delivery Detail:10 weeks |