tile making machine
Place of Origin:China (Mainland) | Brand Name:Saibo | Model Number:tile making machine | After-sales Service Provided:Engineers available to service machinery overseas |
tile making machine:tile making machine | roof tile making machine:tile making machine | wall tile making machine:tile making machine | roll forming macine:tile making machine |
cold roll forming machine:tile making machine | forming machine:tile making machine |
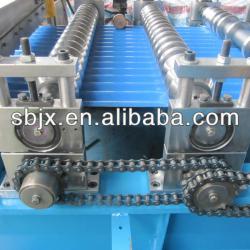
Tile making machine
The profile:The thickness of sheet: 2mm-6.4mm(5SIZE)
l forgalvanized steel coil of ZAR 340
Material resistance Fluencia Elongatión
Std 330 250 20
Zar 340 420 340 12
Direction of the line : Right to left
The equipment flow
2) the cutting press is fly systems
The production flow of equipment
Decoiling—Feeding (take the sheet to the first station)—leveling--- servo feeding—puching(two station)--roll forming -----hydraulic cut to length---manual out table
The structure of equipment
1, Hydraulic de-coiler
(1) Single unrolling machine, one side can put material
(2) Adopt automatic hydraulic system
(3) Coil weight (Max):5000kg
(4) Coil dia (Max): Φ508×1300mm
(5) Oil cylinder dia:120mm working pressure: 10mpa
(6) Coil Width (Max.):500mm
(7) Working speed: 5-6m/min
(8) Power:4K
(9) Coil car: pressure 12Mpa
2, feeding, leveling
(1) feeding the sheet to the guide roller (it is adjustable by right and left).
(2) feeding roller: diameter is100mm, material is 40CR steel, HRC48-52.°
(3) Leveling roller: upper is 3 rollers, down is 4 stations(total is 7 stations), material is 40CR steel, HRC48-52°
(4) diameter of leveling roller: 100mm
(5) leveling power:11KW.
(6) speed:5-20m/min
3, servo feeding&punching (can right and left adjust)
(1)Servo feeding power:4.4KW
(2)Feeding speed:30m/min
(3)Feeding presision:+_0.5mm
(4)using hydraulic punching
(5)mould material: Cr12 quenched 58°-62°
(6)hydraulic power: 22kw(with stored energy tank)
(7)pressure:100tons
(8)punching frequency:5times/min
(9)punching station: 2stations
(10)the more thick material will change the punch moulds
3)in the next days I will send you the final holes sizes.
3: roll forming
(1)main motor power: 55kw
(2)Decelerating motor: BWD14-43-55KW, made in Shanghai or Changzhou
(3)drive: by gear with coupling joint
4: Coupling transmission
(1)wall sheet thickness is 30mm.
(2)main shaft dia:130mm material: NO 45forge steel
(3)roller material: GCR15 quenched 58°-62°,chromed
(4)roll station: about 10stations
(5)roller thickness: 5.0mm as standard
(6)Timing by transducer:4m--6m/min( including punching time)
(7)Transducer: Panasonic made in Japan. 380V 50HZ
(8)Computer: PLC
(9)Computer operating panel: touching screen
(10)Machine structure: adopt cast steel
5: flying cutting--include 6 sets blades)
(1)hydraulic cutting
(2)knife material: Cr12,quenched 58°-62°
(3)working pressure:25mpa
(4)working journey: 160mm
6: Control panelPanasonic
1:Full line is controlled by PLC control system,touch screen operation to achieve the human and PLC interactive. The operator can monitor the setting program (programmable control) and modify the parameter to control the line. Also can check the running status, parameter and error indication etc..
2: Operation type: manual /auto two type switch. In manual position: can run the each part of the machine. In auto position: can run the full line. The emergency stop ensures the safe of the equipment and operator.
3: Machine side is equipped with the manual operation control panel for convenient worker to operate;
4: Entire line surveillance function: to reach surveillance production line movement condition, realizes to various locations production condition surveillance;
5: Has the failure detection function: Carries on to the production line signal succession examines, the checkup according to sequence, discovers the mistake, and giving the alarm to stop the machine.
7: theOutside size:
(1)25m long*2m wide*1.2m high
8: manual out table:weld by 60mmx40mm pipe, size: 1.0x0.8x0.8m LxWxH
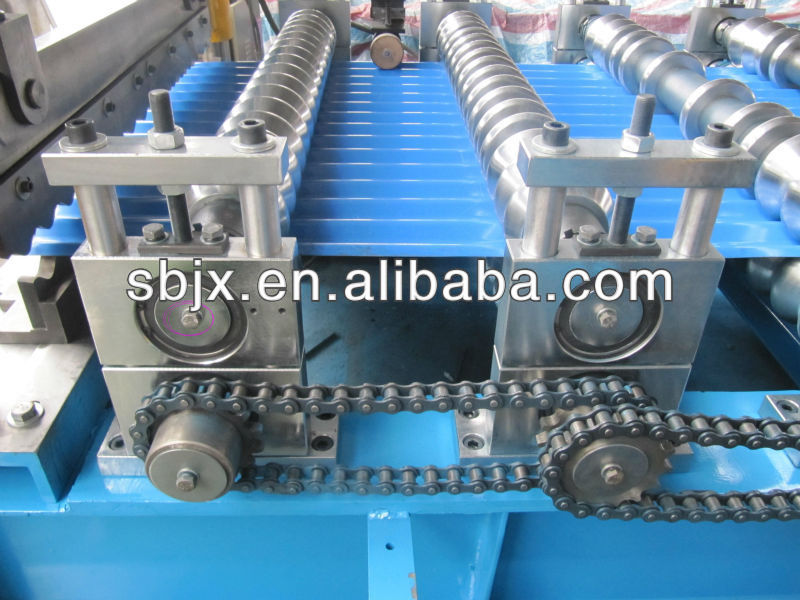
Packaging Detail:no packing |
Delivery Detail:50 days |