The most advanced super finishing equipment--Metal shaft super finishing equipment
Ra0.2-0.8, 20% better than before, depth is 0.1-0.2mm;, can completely keep the same accuracy as before, even better than before - details see: https://www.machineto.com/the-most-advanced-super-finishing-equipment-metal-shaft-super-finishing-equipment-10164413
Condition:New | Place of Origin:Shandong China (Mainland) | Brand Name:Huawin Hawking | Model Number:HKUSM30HSQ |
Voltage:220V±10% | Rated Power:480 | Dimension(L*W*H):1000mm*400mm*800mm | Weight:170kg |
Certification:CE | Warranty:1 year | After-sales Service Provided:Engineers available to service machinery overseas | Type of maching:arc surface |
Value of roughness:Ra0.2-0.8 | Micro-hardness:raise 20% than before | Size accuracy:completely keep the same,even better | Vibration stress:preset compression stress and relief tentile stress |
wear-resisting:raised a lot | corrosion resisting:raised a lot | micro defect:raised a lot | metal working life time:raised a lot |
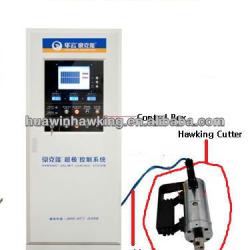
Brief introduction of HawkingPTmetal work technology:
- ≤0.2µm.
Processingafter before
Solutions of HawkingPTmetal work technology
- Solutions of HawkingPTMachine Tool. We provide solutions of HawkingPTUnlimit+combined machine tool, HawkingPTUnlimit+Lathe and HawkingPTUnlimit+boring machine for professional metal work and technical process.
- Modification solution of processing technology. We provide solution of HawkingPTMirror Finishing specially for excircle, inner bore, end face, R arc, and complex surface.
- Modification solutions of processing equipment. We provide modification solutions of HawkingPTMirror Finishing specially for horizontal lathe, vertical lathe, spherical lathe, cylindrical grinding machine, boring machine, miller, planning machine and processing center.
- Industry solutions. We provide professional engineer to make solutions of HawkingPTmetal work according to the specificity and characteristics of different industries.
HawkingPTHKUSM30G Series
- Control and display the matching rate of controller and cutter energydynamically.
- Control and display the matching rate of controller and cutter frequencydynamically.
- Control output energy of cutter more accurately
- Display operating steps and fault diagnosis.
- Working efficiency increases 25%.
- Surface roughness improves a grade after processing.
Hawking VS Polishing P32 | ||
Item | Hawking tech | Polishing |
result | reach super mirror-finishing result of Ra≤0.2µm ; feeding between 50 and 80m/min | Ra1.6-0.8µm |
efficience | line speed between 50 and 80m/min; feeding between 0.2 and 0.5 mm/r. efficient as the semi-superfinishing | inefficient |
microhardness | improve 20% more than before | no change |
fatigue | improve | no change |
stress situation on metal surface | eliminate pulling stress on metal surface and preset perfect pressing stress | uncertainty |
wear-resisting | improve | no change |
corrosion resisting | improve | no change |
quality on metal surface | even | uneven because of constant abrasing by grinding wheel |
other materials consumption | no | using polishing whee,grinding material, abrasive belt etc. |
procedure | not need moving the workpiece..Just clamp our equipment on the same lathe /machine tool | must move a workpiece to a polishing machine |
operating envirenment | energy-efficient,enviroment protection,no sand & scrap iron | will leave some sand,scrap iron,dust , bad enviroment |
suitability | best suitability,suitable for all kinds of surface shape | bad suitability, curved surface can not be processed |
damage to a lathe/machine tool | no cutting and no damage to a lathe | sands left over can damage the part of rail road on the lathe |
operating room | need a little space to set our equipment | special operating room, spcial space |
possibility of danger | no | grinding wheel might damage an operator |
P33
Hawking VS Cylindrical grinding | ||
Item | Hawking tech | Cylindrical grinding |
result | reach super mirror-finishing result of Ra≤0.2µm ; feeding between 50 and 80m/min | Ra1.6-0.8µm |
efficience | line speed between 50 and 80m/min; feeding between 0.2 and 0.5 mm/r. efficient as the semi-superfinishing | inefficient |
microhardness | improve 20% more than before | no change |
fatigue | improve | no change |
stress situation on metal surface | eliminate pulling stress on metal surface and preset perfect pressing stress | uncertainty |
wear-resisting | improve | no change |
corrosion resisting | improve | no change |
suitability for meta materials | can process a hard,soft and sticking metal materials | can not process a soft and sticking metal materials |
environment protection | very good,nothing left | leave sand and junk cooling liquid |
energy consumption | very little,the power is less than 1kw | very big, the power must be more than many kw |
procedure | not need moving the workpiece..Just clamp our equipment on the same lathe /machine tool | must move a workpiece to a polishing machine |
other materials consumption | no | using grinding wheel and cooling liquid |
P34
Steps of Hawking VS Normal grinding | ||
Step | Hawking tech | Normal grinding |
1 | use a suitable cutter imported from Switzerland to get a basic size and geometrical tolerance meeting the requirement of drawing. Roughness is Ra2.1µm. | use a Kenner KT315 cutter to get a basic size and geometrical tolerance meeting the requirement of drawing by finish maching. Roughness is between Ra3.2 and 6.3µm. |
2 | use a Hawking cutter clamped on the lathe to process (line speed of processing is 39 m/min, feeding is 0.3mm/r) | it will take72 hoursto manually grind a work piece by using a millstone with No.150 diamond grain. In order to completely eliminate the screwing wave during grinding. |
3 | done intwo daysfrom size precision to mirror finishing level.Value of Ra between 0.07 and 0.1µm | it will take24 hoursto semi-grind a work piece by using a millstone with No.180 diamond grain. |
4 | better than what the design requires | it will take16 hoursto grind a work piece by using a millstone with No.240 diamond grain. |
5 | it will take3 hoursto polish a work piece by using W7 polishing paste and kerosene on lathe when the top spinning speed is 40r/min and line speed about 300m/min . | |
6 | roughness between Ra0.16 and 0.2µm,meet the requirement |
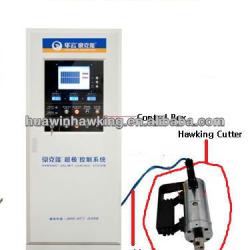
Packaging Detail:box |
Delivery Detail:30 days after advance payment |