The most advanced Sand AAC bricks manufacturing equipments
Condition:New | Type:lightweight solid brick | Brick Raw Material:Sand | Processing:Brick Production Line |
Method:Vacuum Extruder | Automatic:Yes | Capacity:as customer request | Place of Origin:Henan China (Mainland) |
Brand Name:qiangyuan | Model Number:varies | Voltage:varies | Power:more |
Dimension(L*W*H):varies | Certification:ISO9001:2000 | Warranty:12 months | After-sales Service Provided:Engineers available to service machinery overseas |
Color:as your request | Authentication:ISO9001:2000 |
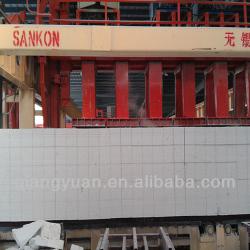
AAC bricks manufacturing equipment
A. Light weight
Aerated concrete density is usually 400-700kg/m3, it is about 1/3 of the clay brick weight and 1/5 common concrete block weight. Using the Light brick can reduce the weight of the building and also reduce the loading of the beam of roof and pillar. You can see, it can save the material and cost, it also fight against shaking.
B. Keeping temperature
It has many porous, the heat transition coefficient is 0.9-0.22W/ (mk), and it is just about 1/4 or 1/5 of clay brick, so it is the best materials for keep the room temperature now in the world.
C. Raw material available widely
There are many kind materials even waste material can be used to produce AAC products, for example: coal ash, sand, waste mine material, coal stone, stone dust, and other silicon materials.
D. Saving land and energy
When you produce AAC products it use the energy (or fuel) just 11% of the clay brick Products.
E. The feature of Plasticity
The AAC Products has one useful advantage is the “Plasticity”. As it is has more foam inside and the weight is lighter and not so hard so it is easy to be produced in every kind shape and when it is re-assemble or re-production it will be more suitable for sawing, paring, drilling, and clinch (clench).
F. Sales Profit
AAC Products’ market profit is bigger than common bricks and cement blocks, especially the AAC Board products (Plate shape AAC Products).
Application
AAC brick is applied widely in the world, especially in below conditions and places.
- 1stYouth Olympics Games in Singapore
- Pakistan Flood of 2010
- Russia Fire
- Hainan province flood in China
- In the earthquake of Indonesia and New Zealand
- Infrastructure in Iraq and Afghanistan
- 16thAsian Games Guangzhou
- EXPO 2010 Shanghai
- Infrastructure of America
- London 2012 Olympic and Paralympics Games
Production Process of Aerated Concrete
Production Process of Aerated Concrete According to the category and quality of raw material, and the features of equipment, the aerated concrete can be manufactured in different processes. Generally, add water to ash, silica sand or slag and crush them into slurry; then add powdery lime, cement of right amount, plaster, vesicant, foam stabilizer, and mix and pour it to mould frame; after curing, foaming and hardening, cut it into blocks and boards in different specifications; finally, transport it into pressure steamer with steam-curing cart, and get the light cellular concrete after steam-curing with high temperature and pressure. Process Flow of an Annual Output 50,000m3---300,000m3 Aerated Concrete Steam-Curing Production (1) Various raw material storage tanks → (2) Mix dosing → (3) add water to raw material and mix them → (4) prepare the mould → (5) pour → (6) foam and wait → (7) release from mould → (8) turn up, cut horizontally and vertically → (9) make into groups and get into autoclave → (10) cure under high temperature and pressure → (11) release the finished products from the autoclave → (12) test the finished products → (13) pack → (14) stack and store up → (15) leave the factory.
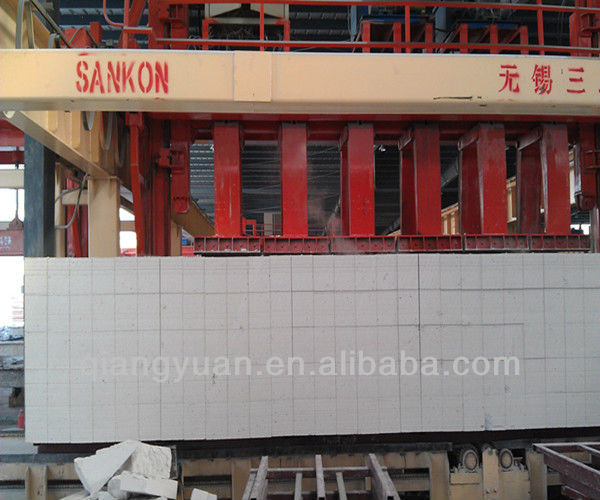
Packaging Detail:standard container or as your request |
Delivery Detail:10-30 days based on the prepayment |