Spiral Welded Pipe Line
Type:Pipe Production Line | Pipe Material:Iron | Application:Energy Supply Pipe | Place of Origin:Shanghai China (Mainland) |
Brand Name:AITOMU | Model Number:SWP |
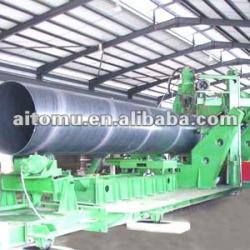
Spiral Welded Pipe Line
Characters:
Spiral Welded Pipe Line mainly produce all kinds of pipe using deliver water, gas and construction. This line technique is advanced, work perfectly and produce continuously and smoothly.
This line adopts front swinging structur continous production, is combine mechanism,electric robotization control, hydraulic control complete Spiral Welded Pipe Line.
Our machine have protector device for operato, pinching and delivering machinec could enter into self protecting function when plate thickness changing. Control system adopt PLC control, all parameter could show in live time, also set program, easy to operate and manage.
Process Flow
Coil Preparation→Uncoiling→Head Straightening→Pinching& Leveling→Electric Vertical Roll→ Cutting& Butt Welding→Electric Vertical Roll→Edge Miller No.1→Electric Vertical Roll→Edge Miller No. 2→Vertical Roll→Pre Bending Guide Board→Forming→Inside Welding→Outside Welding→Cut To Length→Collection
Introduction Of Main Equipment
1. Uncoiler
Function: to support and hold strip coil, the coil actively rotates combing with perching knife to peel strip and feed strip end to pinching& leveling machine
Composition: consists of feeding car, cone head uncoiler, and coil peeler.
2. Pinching& Leveling machine
Function: to level strip and feed strip to cutting& butt welding and delivery position.
Composition: hydraulic cylinder drives double roll pinching, worm gear elevator lifts five roll leveling. Lower roll actively drives under actuation of chain wheel, and feeds material driven by planetary cycloidal reducer.
3. Cutting& Butt Welding
Composition: butt welding platform can be wholly moved, consists of front& back pressing plate and butt welding platform
Function: to cut off plate head& tail, and butt weld them.
4. Vertical Roll
Composition: consists of vertical roll and its base. Lead screw drives vertical roll to adjust width, left& right.
Function: to avoid steel strip from being off center.
5. Edge Miller
Function: to mill welding groove to strip edge and mechanically collect the scrap
Composition: consists of machine device, width adjusting device, oil cylinder screw down Positioning device, driving device and tool disc.
6. Delivery Machine
Function: to offer feeding dynamic to the whole production line.
Composition: consists of machine body, speed reducer, coupling and electric motor. AC VF speed regulation
7. Pre-Bending Guide Board
Function: to pre-bend strip edge and feed strip into forming unit
Composition: consists of pre-bending device, upper& lower guide board
8. Forming Unit:
Function: to force the strip to bend as per requirement
Composition: three-roll forming, outside control roll sizing, consists of 1#,2#,3#,4#,5#,6# roll and its stand, base.
9. Front Bridge
Function: base of all equipment before forming, with the function of adjusting forming angle
10. Rear Bridge
Carrier of all equipment after forming, with the function of fine-tuning angle, cut-off and outlet pipe.
11. Buried Parts Of Host Machine:rail of host machine.
12. Flying Cutter
Function: carrier for cutting pipe to length
13. Inside& Outside Welding Device
Carrier of LINCOLN welding torch, with the function of adjusting welding torch position
14. Centralizer
To keep real bridge output in line, meantime connect with outside welder.
15. Hydraulic System Of Host Machine
Hydraulic pump station is the work system of each hydraulic device that reply on hydraulic power. It is used to supply pressure medium with controllable direction, pressure and flow to each action element (as hydraulic cylinder, hydraulic motor, etc.), to reset and achieve recycling work.
15.1 Arrangement Of Pump Station
Horizontal arrangement: motor pump group is horizontally installed on cover plate of oil tank, which mainly suits hydraulic system of good self-absorption like small displacement or small displacement variable pump.
15.2 Work Medium And Temperature
Work medium: recommend to use the anti-abrade hydraulic oil, YB-N46
Medium temperature: normal temperature: 35-60 0C, when the temperature below 15 0C or exceed 60 0C, must heat or cool till the normal temperature.
15.3 Adoption Of Hydraulic Component
Adopt the product produced by introducing Rexroth technology.
15.4 Cooling Of Hydraulic Pump Station
Force cooling: water cooling
15.5 Electric control
Control way: to control the hydraulic pump station by junction box.
Control power: Voltage: 380V, frequency: 50Hz, coil control power of the electromagnetic valve is DC 24V
16.Electric system
Electric system of host machine applies to operate and control each individual equipment of large diameter SSAW pipe production line, belongs to non-standard electric control system, control from uncoiler till rear bridge.
Consist of PLC auto-control system, DC speed governor, AC speed governor and digitalized display system, of which design and spare parts are in line with IS9001 and CCC standard
Have speed auto-balance governing, manually continuous adjustment
Equipped with automatic plate speed display system
Equipped with pipe sizing control and automatic cutting off system
Electric motor above 22KW (without speed regulating system) equips with reduction voltage starting
Input reactor is equipped for AC VF device and DC speed regulation device to lower pollution to power net side.
Profibus technology is used, Germany SIEMENS S7-300 serial PLC (CPU315—2DP) as main control, submodule at bus terminal and module at site adopts SIEMENS ET200 serial. Protection level of element at site is IP44, as for control cabinet and operation panel is IP20.
AC speed regulator is SIEMENS M440 serial VF speed regulator, DC speed regulator is
Eurotherm 590P serial.
Control function of electric control system is designed to tightly linked with unit process, individual equipment and hydraulic system, and can control as per variation.
No | Model | Specification | coil width(mm) | Thickness(mm) | Coil weight(ton) | Capacity(kw) | Area(M2) |
1 | SWP-400 | Φ219~Φ426 | 400~750 | 5~10 | 10 | 180 | 18×180 |
2 | SWP-500 | Φ219~Φ529 | 400~800 | 5~11 | 15 | 200 | 18×180 |
3 | SWP-600 | Φ219~Φ630 | 450~1050 | 6~12.7 | 20 | 240 | 21×180 |
4 | SWP-700 | 2Φ19~Φ720 | 500~1250 | 5~14 | 20 | 260 | 21×180 |
5 | SWP-800 | Φ219~Φ820 | 500~1300 | 6~18 | 30 | 380 | 24×180 |
6 | SWP-1000 | Φ219~Φ1020 | 500~1300 | 6~20 | 30 | 390 | 24×180 |
7 | SWP-1400 | Φ325~Φ1420 | 500~1560 | 6~22 | 30 | 400 | 26×180 |
8 | SWP-1600 | Φ426~Φ1620 | 500~1560 | 6~25.4 | 40 | 510 | 30×180 |
9 | SWP-1800 | Φ508~Φ1820 | 1100~1600 | 8~25.4 | 40 | 510 | 30×180 |
10 | SWP-2000 | Φ508~Φ2020 | 1200~2000 | 8~25.4 | 40 | 530 | 30×180 |
11 | SWP-2400 | Φ508~Φ2400 | 1200~2000 | 8~25.4 | 40 | 530 | 30×180 |
12 | SWP-3000 | Φ508~Φ3000 | 1200~2000 | 8~25.4 | 40 | 530 | 30×180 |
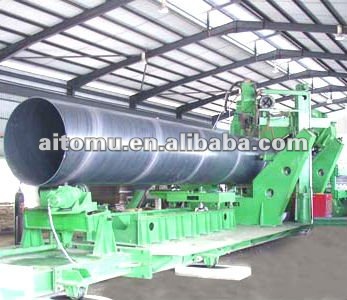
Packaging Detail:40 T |
Delivery Detail:6 MONTH |