Sand/Fly Ash AAC machine (design/manufacturing/installation/training)
Condition:New | Place of Origin:Shanghai China (Mainland) | Brand Name:ZAONEE | Model Number:ZN-X |
After-sales Service Provided:Engineers available to service machinery overseas | Plant Area:20000-35000m2 |
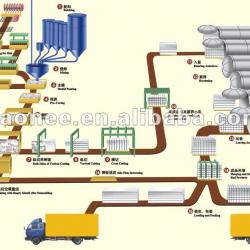
We supply the entire solution of the AAC plant,Capacity from 50,000m3-350,000m3 yearly
Sand/Fly Ash AAC machine (design/manufacturing/installation/training)
AAC Block Production Line
AAC is made from silicon material (silica sand, or recycled fly ash and silica gangue) and calcium material (lime, cement), mixing with foaming additive (aluminum powder), batching with water, the reaction between aluminum and concrete causes microscopic hydrogen bubbles to form, expanding the concrete to about five times its original volume. It is made into the multi-cells silicate products by the processes of resting, tilting, cutting and autoclaving.
Process chart
To manufacture AAC, cement is mixed with lime, silica sand, or recycled fly ash, water, and aluminum powder or paste. The slurry is poured into moulds where a chemical reaction occurs, the reaction between aluminum and concrete causes microscopic hydrogen bubbles to form, expanding the concrete to about five times its original volume. After evaporation of the hydrogen in the mold for 45mintues, the high closed cellulated AAC unit is cut to size and formed by steam-curing in a pressurized chamber (an autoclave) for 10 to 12 hours. The result is a non-organic, non-toxic, airtight material that can be used for wall, floor, and roof panels, blocks.
Project cases
With abundant air cells and micro apertures inside the aerated brick, it has good performance of heat insulation and preservation. In addition, the most prominent advantage is its plasticity. Due to the lightness and the lower hardness, AAC units are available in numerous shapes and sizes according to the real construction usages and customer's requirements.
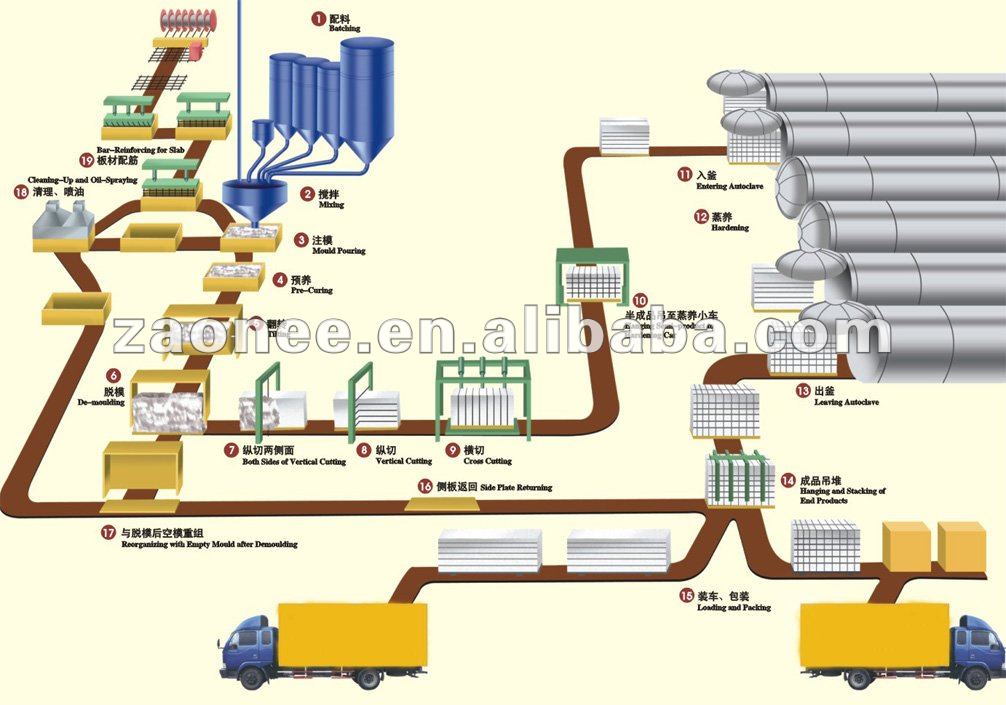
Packaging Detail:Seaworthy packing |
Delivery Detail:120days |