PVC Coating Lines,PVC wire coating machine, pvc wire coating line
Type:Coating Production Line | Substrate:Iron | Coating:Other | Place of Origin:Hebei China (Mainland) |
Brand Name:xinfeng | Weight: about:3000kg | Total power:55kw |
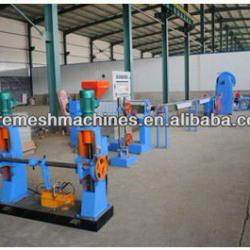
PVC Coating Lines,PVC wire coating machine, pvc wire coating line PVC wire Coating Lines
1. Product Introduction
Our PVC wire coating line apply to PE, PVC, rubber etc. adopts thermoset extrusion to isolation the wire core, then through change the different mechanical headstocks and dies, we can get the steel wire that the customers need.
The main machine barrel and screw adopt 38CrMoAl material, are made through twice nitrogen treatment, which can extend the machine service life. This machine line is the ideal products of PVC wires and cables manufactures.
2. Electrical Units of Type 65
A.wire spools, I set
B.wire re-winde
C wire un-winde
D;tension control
E. extruder; type 65, I set (5.5kw, speed adjustable, 5-step temperature control)
F. temperature control electric cabinet
G. cooling bath—2m; 2set/section
H. wire tracking, I set
I.wire re-winder; 1set
3. Technical Data
NAME | UNIT | DX65 |
Wire diamter | mm | 0.5~4.5 |
In-wire speed | m/min | 6~120 |
Screw diamter | mm | 65 |
Length-diameter ratio | - | 65:1 |
Compression ratio | - | 1:3 |
Main machine power | kw | 5.5~7.5 |
Heat up power | kw | 5~7 |
Pulling power | kw | 1.1 |
Specification | mm2 | 0.3~16 |
Wire re-winder diameter | mm | 560 |
Exterior size of main machine | mm | 1520×660×1500 |
4. Installation and Debugging
The machine must be checked as following, after sure of that, it can test run
1. check all the bolts, fastening screws and foot screws whether fasten or not;
2make sure there is no sundries in the gear box, and then add enough oil for lubrication;
3check the temperature control electric cabinet, make sure the electrical line is correct;
4check whether the motor towards the right turning direction.
Check all the rotatable elements make sure they can run smoothly.
After the check above, start the machine for empty running; and if there is no problem with it, do the following as the actual test running.
1. install the out-wire die accordingly
2. adjust the temperature of the main machine and auxiliary machines accordingly
3. inject cool water into the cooling bath
4. let the wire into the pay-off stand
5let the wire into the die through the horizontal wheel accordingly
6. through traction wheel let the lead wire into the take-up reel
7. start the machineries, try testing running
8. check whether the cable wire made by the machine up to the standard, if ok, you can run the machine normally.
5. Machine Maintenance
Proper operation and maintenance are the premise of the machine smoothly running and long service life, so you have to strengthen the machine maintenance system. At first, check fastening screws in every position, make sure they are fasten, in case of looseness; keep the oil amount in the right position(about 2/3), make sure the lubrication of the bearings; during oil, keep the bearings well, for insure the life time of the bearing.
6. Machine Operation
The machine type 65, it should be installed and debugged by the technician, and after the trail running well, it can work normally.
1, Before the machine running, heat the barrel and screw of the extruder first, pre-warming it according to the plastic thermal melting temperature, and keep for the definite heating time, let the plastic plasticizing, so that the wire it produced will looks brightness; which avoid, the wire will be unbrightness and rough surface under low temperature, or the wire cable surface will be scorched under the high temperature, it will decrease the plastic insulation degree. If you want to get all of the plastic plasticizing, you should adjust the temperature according to there inner frame. The temperature are different from the different plastic plasticizing degree, so you have to adjust it according to the different produce situation.
2, when the plastic up to plasticizing, prepare the cable dies, aluminum wire, copper wire and other material well.
3, during the pre-heating, start up cool water cycle, make it coincidence to the requirement, and then wait for the produce of the products.
4, the usage of temperature control electric cabinet
4-1, install and connect it by the professional electrical technician, let it up to demand.
4-2, temperature line: fetched by temperature control cabinet, install it on the fixed position of the barrel; there are two heads of the temperature line, positive and negative, if connect it wrong, it will show no temperature, so you have to change it into the right way.
4-3, when pre-heating and the normal operation, you should adjust the temperature accordingly; and if you just produce one kind of plastic, just keep the temperature in the same range.
4-4, the control parts of the temperature control electric cabinet, type45 wire coating line
4-4-1,extruder main motor
4-4-2,extruder barrel heating appliance
4-4-3,temperature line
4-4-4,Pulling motor of the wire tracking
4-4-5,torque motor of the torque transmission device(equipped with type 65-3)
4-4-6,Elevating motor(equipped with type 65-3)
4-4-7,Pump motor(equipped with type 65-3)
4-5, the temperature control electric cabinet is a complicated electric equipment, which included semi-automatic and full-automatic device it plays an import role on the whole production line. If you can operate it correctly, it will make sure the whole production line running smoothly; otherwise, it will be a waste of material, labor and power. So it should be operated by the people who is familiar with the electricity, and also he should be under the direct of the installation technician.
5, after the pre-heating, install the cable die. Get the inner wire (both aluminum wire and copper wire are ok )from the pay-off stand, through horizontal in-wire stand, die, coiling bath and horizontal wheel, let the wire in to the wire tracking wheel, and after two or three cycles, through the cycloid device(that is reciprocating motion),cycle the wire into the wire collection wheel(wire re-winder). Start the machine slowly, and make the start motor and tracking motor running, let the plasticized plastic cover the surface of the wire, and than increase the speed of the machine. Visual observation the surface of the covered wire, and check the eccentricity by hand; and after the adjust of the experienced technician, the wire it produced will up to the international standard(whether the wire can up to the national standard, it determined by the quality of material).
5-1, adjust the eccentricity of the cable wire
During the cable processing, you should adjust the cable core, and if there is a eccentricity, there are 4 place on the mechanical headstock die(face to the machine): if the eccentricity is outside, exit wire 1 slightly, fasten wire 2, and then the wire will move into the center; if the ; eccentricity occurred on 2 and 3, it will be more easy to adjust: if the eccentricity upward, exit 3 and fasten 2; and if eccentricity downward, exit 2 and fasten 3; and adjust eccentricity should operate by the experienced worker.
5-2, adjust the surface of the cable wire
Some plastic is heat- resistance, while some others not, so you should adjust the temperature according to different kind of plastic. The machine type DX65 has 3 temperature zones, and there are the temperature difference between those section, and the general temperature of them are as following:
PVC material
Section 1 | Section 2 | Section 3 |
mechanical headstock | Front of the barrel | Back of the barrel |
140°C~150°C | 140°C~150°C | 160°C~180°C |
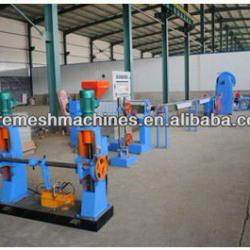
Packaging Detail:container |
Delivery Detail:45day |