professional cement plant manufacturer
Condition:New | Place of Origin:Henan China (Mainland) | Brand Name:Yufeng | Warranty:2 year(Excluding the spare parts) |
Technical:Technical support | Installation:Dispatch engineer guide | OEM/ODM:OEM | Quality:Export standard |
Motor:As the customers' request | Shipping:By sea | Drawing / flow chart:Provide flow chart / draw | Certificate:ISO/CE 2 |
Equipments:Offer the whole plant equipments | Factory:welcome to visit |
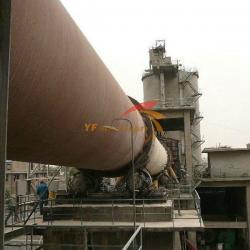
professional cement plant manufacturer
1. Raw Materials
The main raw materials used in the cement manufacturing process are limestone, sand, shale, clay, and iron ore. The main material limestone is usually mined on site while the other minor materials may be mined either on site or in nearby quarries. Another source of raw materials is industrial by-products. The use of by-product materials to replace natural raw materials is a key element in achieving sustainable development.
2. Raw Material Preparation
Mining of limestone requires the use of drilling and blasting techniques. The blasting techniques use the latest technology to insure vibration, dust, and noise emissions are kept at a minimum. Blasting produces materials in a wide range of sizes from approximately 1.5 meters in diameter to small particles less than a few millimeters in diameter. Material is loaded at the blasting face into trucks for transportation to the crushing plant. Through a series of crushers and screens, the limestone is reduced to a size less than 100 mm and stored until required.
Depending on size, the minor materials (sand, shale, clay, and iron ore) may or may not be crushed before being stored in separate areas until required. professional cement plant manufacturer
3. Crushing and Pre-homogenization.
During producing Concrete, most of the raw materials must be first crushed before being used to make concrete. These raw materials include lime stone, clay, iron ore and coal, etc. The lime stone is of the greatest usage to make concrete. With comparatively larger particles and higher hardness, crushing the lime stone to required fineness after mining is of relatively important consequence among crushing all those raw materials. There are many crushers used in crushing these raw materials, such as jaw crusher, impact crusher, cone crusher and vertical shaft impact crusher, etc. According to the raw materials' different particles and hardness, there are several suitable crushers which can be used in the crushing.
4. Raw material Homogenization.
In the process of new dry concrete production, the stability of pit entry clinker raw material component is the premise of the whole system. Raw material homogenization system plays very important role in the stability of pit entry clinker raw material component. professional cement plant manufacturer
5. Pre-heater and Calciner
6. The Burning of Concrete Clinker.
7. Grinding
Grinding is the last process of cement produce and the most current consuming working procedure. Cement clinker get grinded into the right size. The smaller the particle size is, the better the final cement is. It's important to choose suitable grinding machine.
8. Concrete Packaging
Cement manufacturing consists of raw material grinding, blending, precalcining, clinker burning and cement grinding.
In short, limestone and other materials containing calcium, silicon, aluminum and iron oxides are crushed and milled into
a raw meal. This raw meal is blended and then heated in the preheating system(cyclones) to start the dissociation
of calcium carbonate to oxide. The meal goes further into the kiln for heating and reaction between calcium oxide and
other elements to form calcium silicates and aluminates at t a temperature up to 1450 centidegree: so called clinker burning
. The cyclone system is attached to the rotary kiln by a riser duct. Secondary fuel is fed to the riser duct, the main fuel
mixture, coal/petcock, fires the kiln. Reaction products leave the kiln as a nodular material called clinker. The clinker will
be interground with gypsum and other materials to cement. professional cement plant manufacturer
The equipments we use in this whole production line are vibrating feeder, jaw crusher, impact crusher, cement ball mill, lifer, preheating system, cement rotary kiln and packing machine and so on. All the necessary equipments in this line can be provided by our factory. We have cement production line experts to design specific solutions for your preference.
Production Line We Offer:
1) Stone Production Line
2) Beneficiation Production Line
3) Sand-making Production Line
4) Cement Production Line
5) Gypsum Production Line
6) Lime Production Line
7) Drying Production Line
8) AAC Production Line
9) LECA Production Line
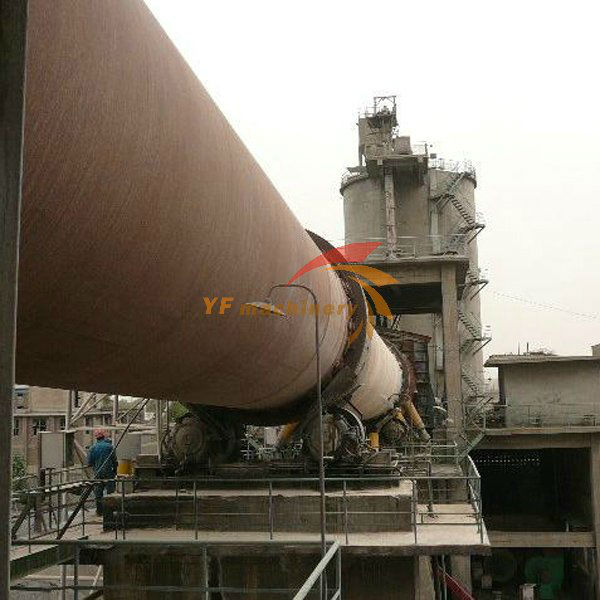
Packaging Detail:container |
Delivery Detail:20 Working days after deposit |