Pre-finishing mill
Place of Origin:Shaanxi China (Mainland) | Brand Name:HangJi | After-sales Service Provided:Engineers available to service machinery overseas | Packing:seaworthy packing |
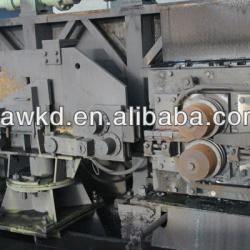
The function of pre-finishing mill
In the process of high-speed wire-rod rolling, pre-finishing mill can improve the precision of the rolling element to guarantee the product quality and avoid possible operation failure during the finishing mill section.
The structure of framework
Its structure is two horizontal and two vertical (horizontal-vertical-horizontal-vertical; H-V-H-V) cantilever type, it is very compact, and the weight adjustment is more precise and reliable, and so to avoid possible twist rolling.
Pre-finishing mill is composed by two horizontal mills, three vertical loops, two vertical mills, safety cover and so on.
Equipment structure
Transmission box
The role of transmission box is to transmit the moment outputted by reduction gear and motor to roll shafts. Horizontal box has a pair of cylindrical bevel gears; vertical box has a pair of additional spiral bevel gear beside a pair of cylindrical bevel gear. The spiral bevel gear speed ratio of the two vertical transmission boxes is different.
Roller box
Each roller box has one upper roll shaft and one lower roll shaft; they are not meshed, and driven by a pair of cylindrical bevel gears in the transmission box.
A cantilever cylindrical roll shaft is fixed to each roll shaft; the roll shaft is fixed in the eccentric locking collar and sustained by the front and rear film bearing. Driven by the left and right feed screw and nut of the shaft gap adjustment device, the eccentric locking collar makes the upper and lower roll shaft open and shut symmetrically and evenly relate to the milling centre line, in so to achieve roll shaft gap adjustment. The roll shafts are made oftungstencarbide.
The roller box is installed with flange in plug-in method,
and convenient to assembly and disassembly, the roller box and transmission box are individual unites, during the installation,assemble the roller box and transmission box at the first stage and then fix the roller box inside the transmission box with screw bolt, the roller box is positioned by two locating pins to obtain accurate position. In this way, the installation can be done easily and with a shorter time, meanwhile, the pipework on the panel is reduced and make it easier for failure handling.
1, The roller gap is adjusted by using the eccentric locking collar, by adjusting the lead screw and nut , the eccentric locking collar will spin and then drive the roller shaft to move symmetrically, in so to achieve the adjustment of roller shaft gap. The best advantage of this adjustment method is that the central line will be kept unchanged.
2, By using the thrust bearing that fixed at the end of the roller shaft, we can effectively prevent the axial shift of the roller shaft, in so to ensure size accuracy of the product.
3, the size and structure of the roller box for horizontal framework and vertical framework are the same, all the parts are interchangeable.
4, the power transmission and speed control are conducted by a pair of spiral bevel gears in the transmission box, the reducer is omitted from the transmission system of the vertical rolling mill, so that the whole equipment is lighter and smaller.
5. As the horizontal framework is completely symmetrical, it can be rotated 180, so it can be shared by two production lines that located at its right and left side.
Guide device
The entrance of roller box has installed scroll guide and slip guide, the exit of roller box just has slip guide, slip guide is lubricated byspeciallubrication device.
Main technical features
First mill input specification: dia28~dia31mm
Fourth mill output specification: dia16~dia20mm
The kinds of rolling steel: Carbon steel, high carbon steel, low alloy steel, welding steel, heading steel.
The temperature of rolling: 900~1050°C
Transmission method: Direct current (DC) motor alone drives
The transmission parameter table of pre-finishing mill
framework | Roller size | main motor | Ratio of speed | Rotary speed of roll r/min | ||||||
Maximum outside diameter mm | Minimum outside diameter mm | Inside diameter mm | width mm | type | power kW | Rotary speed r/min | ||||
15H | 285 | 255 | 160 | 95/70 | DC | 450 | 0/600/1200 | 1.5 | 247~476 | |
16V | 285 | 255 | 160 | 95/70 | DC | 450 | 0/600/1200 | 1.24 | 314~606 | |
17H | 285 | 255 | 160 | 95/70 | DC | 450 | 0/600/1200 | 1.25 | 407~782 | |
18V | 285 | 255 | 160 | 95/70 | DC | 450 | 0/600/1200 | 0.94 | 500~1001 |
Maximum rolling strength:~240kN
Maximum rolling moment:~6.2kN·m
Centre distance of roll shaft: dia255mm~dia291mm
Adjustment of roller gap:±18 mm
Cooling water of roll shaft: consumption: 4x20 t/h
water pressure 0.6MPa
temperature of water coming: <30°C
(11)lubrication
Roller box and reduction equipment adopt thin oil to lubricate, which is offered by workshop.
Pressure of oil: pressure in lubrication point 0.15~0.25MPa
Total consumption: 400 l/min
Oiliness: Mobil 533
Refined filter: 25μ
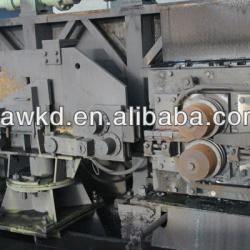
Packaging Detail:seaworthy packing |
Delivery Detail:30 days |