Powder Point-Bonded Interlining Coating Machine
Place of Origin:Shanghai China (Mainland) | Brand Name:DaHe | Model Number:DJ01-135,175,200,220,250 |

aapplication:
Thisinterlining coating machineis suitably applied tothe powder point transfer bonding with use of thermoplastic adhesives(HDPE,LDPE,PA,PES,EVA,EVAL)to produce various woven and nonwovens bondedinterliningsfor garment and shoe-making.
Features:
*Equipped with unique fabric feeding device with selvedge calibrator and fabric opener, increase the qualified finished product rate; the heater that doed not use a bokler keeping temperature difference within less than 2°C,guaranteed even and stable powder point transfer; the heating chamber with conveyer making the finished fabric have soft touch and the stable hydraulic winding device bringing in a more easy machine operation;
*Use of advanced electronic components and imported intelligent temperature control and display instrument and motor speed change by imported converter.
Main Technical Parameters:
Items | Parameters | |
Product Width(mm) | 1200 | 1600 |
Production Speed(m/min) | 10~30 | |
Installed General Power | 60KW 380V | 80KW 380V |
Overall Dimension(mm)(L*W*H) | 9000×2100×2600 | 9000×2400×2600 |
Weight(T) | 6 | 7.5 |
Specifications:
1) Production speed: 12 - 25m/min
2) Power supply: 90kW, 380V, 50Hz
3) Coating width: 120 - 160cm
4) Imported advanced electronic components, intelligent temperature
control, display instrument, and motor speed converter
5) Equipped with unique fabric feeding device with selvedge calibrator
and fabric opener
6) Increase qualified finished product rate
7) Heater does not use a boiler keeping temperature difference of less
than ±2oC
8) Guaranteed even and stable powder point transfer
9) Conveyer heating chamber results in finished fabric having soft
touch
10) Stable hydraulic winding device allows for easy machine operation
- Coating Process
Base cloth orientation opening selvage justifying coating curing
Flat padding and cooling winding
- Brief Introduction
2.1 The principle of thepowder dot laminating fabric coating processis: first the thermosol powder was softened and shaped on the engraved roller, then passing through the surface of the heated fabric, the melted powder transfer to the fabric surface to fulfill the powder dot transfer, finally, the powder fixed to the surface via curing closely.
2.2 During the whole process, the stability of temperature plays an important role, while the variation of speed exerts direct influence on the temperature change, so in the production, it is essential to master the relationship between the speed and the temperature, as well as how to control parameters of the whole machine.
2.3 To keep the uniformity of the product quality, operators must operate strictly according to the manual.
- structure and features
3.1 Inlet frame and open-width selvage justifying machine
3.1.1 The main function of inlet frame is to adjust the tension when the matrix enters into the frame head; different tension of different substrate is adjusted by different delivery and tension frame.
3.1.2 Width opening selvage justifying machine assures the substrate smoothly and precisely enter into the frame head, reduce or diminish unevenness of coating by the substrate flipping. This system greatly improves the finished product ratio and reduces the labor intensity.
3.2 Powder dot coating machine
3.2.1 This section is the core heart of the whole process, preheating roller is used to preheat the coated fabric for water removal and fabric heating, main heating roller is used to fulfill the thermosol powder transfer, engraved roller is used to soften and shape the powder, auxiliary heating roller is used to assist the powder transfer.
3.2.2 The four rollers have different functions, but their surface temperature must be uniform and keep constant during the whole process.
3.2.3 All the heating roller in this machine is heat by built-in oil .we adopt imported three-phase voltage regulating automatic temperature control system, the roller temperature is stable and uniform. The surface temperature difference of the heating rollers is less than +-2Centigrades and it changes between +-2Centigrades.
3.2.4 As heat continuously transfers to the surface of engraved roller from the heating roller through substrate, different thermosol should adopt different heat insulating method. Except for HDPE, this heating system is normally used for preheating, in addition, in practical operation, cooling water is also needed to keep the surface temperature not too high. The temperature control panel show that the temperature is less than 2 centigrades.
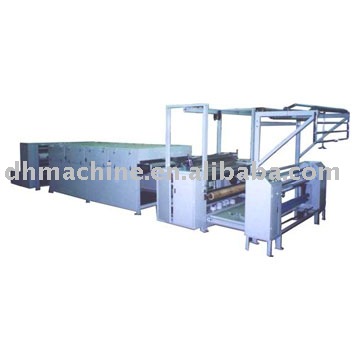
Packaging Detail:10-25container |
Delivery Detail:within 2month or 60days after receipt deposite |