powder coating pump
Condition:New | Type:Coating Spray Gun | Substrate:Aluminum | Coating:Powder Coating |
Place of Origin:China (Mainland) | Brand Name:GL | Voltage:110V~220V | Power(W):50V |
Certification:CE | Warranty:1year | After-sales Service Provided:Engineers available to service machinery overseas | warrant:1year |
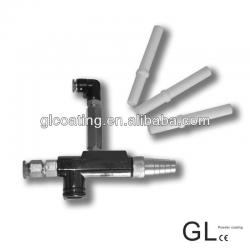
We manufacture the powder coating equipment,powder coating machine,powder coating gun,powder coating system,powder coating line,powder coating plant, electrostatic powder coating equipment, electrostatic powder coating machine, electrostatic powder coating gun, electrostatic powder coating system, electrostatic powder coating line, electrostatic powder coating plant, electrostatic powder spray gun.
mass flow powder pump
1, gema powder coating spare part
2, Professional supplier of powder coating equipment and spare parts for Nordson,wagner
Electrostatic Powder Coating Machine,Powder spraying gun, powder spray gun, metallic powder coating system, electrostatic powder spraying unit, electrostatic powder spraying
Built-in high voltage electrostatic generator
Powder applicable: All kinds of powders
packing:
Popularly used in the metal workpiecess surface treatment Built-in high voltage electrostatic generator Powder applicable: All kinds of powders
we is a profession supplier of powder coating systems and powder coating equipment including manual powder coating equipment, automatic equipment, spray booths,ovens and spare parts for itw gema, wagner, nodrson, kci famous brand in China.
China Powder coating gun, China powder coating machine, China powder coating system, China powder coating equipment, powder coating control unit
.
There is essentially two common ways of applying powder coating: by electrostatic spray and by fluidized bed powder coating. There are several other processes that have been developed, but they are far less used. These include flame spraying, spraying with a plasma gun, airless hot spray, and coating by electophoretic deposition. To get an overview of the technology used in the powder coating industry click on the items below:
•pretreatment
•Electrostatic Spray
•curing
Pretreatment.
Phosphating, or conversion coating, is the application of an iron or zinc phosphate coating to the substrate. Conversion coating can be a very critical part of the pretreatment process, adding significantly to the performance of the finished coating. A phosphate coating converts the metal substrate to a uniform, inert surface, which improves bonding, minimizes the spread of oxidation if the coating is scratchedand improves the overall corrosion resistance of the final part.
A conversion coating can be iron, zinc, polycrystalline, chromate, or manganese phosphate film. They are developed on both ferrous (iron based) and non-ferrous surfaces (zinc, aluminum, terne and manganese). Parts are subjected to an acidic bath and a chemical conversion forms a complete film on the part surface, changing the chemical and physical nature of the metal surface.
Henkelhas introduced a big breakthrough in surface treatment: Bonderite NT – a new surface pretreatment which is considerably more efficient, less complicated and more cost-effective than conventional iron phosphating
Electrostatic Spray
Electrostatic spray powder coating uses a powder-air mixture from a small fluidized bed in a powder feed hopper. In some cases, the feed hoppers vibrate to help prevent clogging or clumping of powders prior to entry into the transport lines. The powder is supplied by a hose to the spray gun, which has a charged electrode in the nozzle fed by a high voltage dc power.
Electrostatic powder spray guns direct the flow of powder; control the deposition rate; control the pattern size, shape, and density of the spray; and charge the powder being sprayed .The spray guns can be manual (hand-held) or automatic, fixed or reciprocating, and mounted on one or both sides of a conveyorized spray booth. Electrostatic spray powder coating operations use collectors to reclaim over-spray. This reclaimed powder is then reused, adding significantly to the powder coating’s high transfer efficiency.
There are various gun designs that mainly differ in the method of applying electrostatic charge to the powder. In some cases, the powder is electrostatically charged by friction. The advantage is that the powder is free to deposit in an even layer over the entire surface of the part, and deposition into recesses is improved.
The film thickness is dependent on the powder chemistry, preheat temperature, and dwell time. Film thicknesses of (40 - 60 µm) in case of plain powder ( 80 – 100 µm) in case of texture can generally be applied on products.
Curing
When a thermoset powder is exposed to elevated temperature, it begins to melt, flows out, and then chemically reacts to form a higher molecular weight polymer in a network-like structure. This cure process, called cross linking, requires a certain degree of temperature for a certain length of time in order to reach full cure and establish the full film properties for which the material was designed. Normally the powders cure at 200°C (390°F) in 10 minutes. The curing schedule could vary according to the manufacturer’s specifications.
The application of energy to the product to be cured can be accomplished by convection cure ovens or infrared cure ovens.
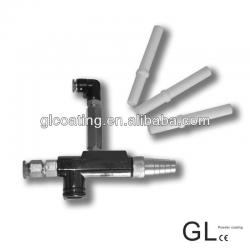
Packaging Detail:Carton :48*35*8cm |
Delivery Detail:3days after receive payment |