Plano milling conversion
Place of Origin:Karnataka India | Brand Name:SEPL | plano milling conversion kit:planomilling conversion kit | add milling capability to planer:milling retrofit |
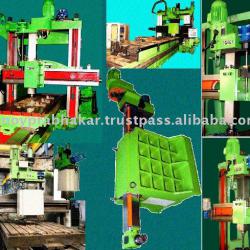
- A converted Plano miller boosts up the productivity of your planer by as much as 10 times without needing additional space and man-power.
- After Plano milling conversion, older planers receive a new lease of life and the newer planers last longer. After Plano milling conversion, not only the table speed is drastically reduced, but also the cutting load is taken over by the self-powered milling head.
- Drastically reduced break-down rates & negligible wear & tear in a converted Plano miller, due to slow feed rates.
- Power consumption drastically comes down, specially in the old planers with Ward Leonard drive system.
- 5 HP, 10 HP, 20 HP all geared Milling heads and different types of feed system packages offered.
- Plano milling conversion offered at site on turn-key basis.
- Special Purpose Plano Millers for specific applications.
- Right Angle Milling Head, in combination with vertical / cross feed, adds floor boring capability to a converted Plano miller.
After removing the existing tool post of the planer, on the same tool post carriage a milling head is mounted, perpendicular to the machine table. If your planer do not have a slow table speed, suitable for planomilling mode, an auxiliary table feed unit is inter-phased to the existing drive system of the planer.
Planomilling conversion of your planer drastically reduces the break down rates of your planer, since its speed is drastically reduced in planomilling mode and the cutting load is taken over by the newly introduced, self-powered milling head.
Planomilling conversion means increased productivity, as much as 10 times – no additional space; no additional manpower are required.
Planomilling conversion adds anew lease of life to your old planer. The slow table speeds in Plano milling mode and shifting of the cutting load from the machine drive system to the self-powered milling head certainly adds years into your old machine. The old planer, which otherwise should have been discarded sooner or later, gets a new lease of life and proves to be one of the most productive machines in your shop floor. lanomilling conversion simply enhances the life span of your machine by several times.
Two factors are to be taken into account whileselecting a suitable milling head– the maximum diameter of cutter you wish to deploy and the rigidity of the cross rail of your planer. For the generally available Indian make planing machines upto about 10 ft stroke length, 5 HP milling heads are the most suited ones. 5 HP milling head is suitable for mounting Ø125 to Ø 160 mm cutter.
Electrical Table Drive Unit (ETDU)is a combination of worm reduction gearbox, motor and a frequency converter (VFD). A control panel houses all the switch gear elements for the milling head motor, table drive motor and the optionally offered cross feed unit and vertical feed unit. An operator pendant station with the required mechanical support houses all the controls and “mm per minute” digital indicator. User friendly, sleek and aesthetic, ETDU is certainly worth a little higher price tag. It provides stepless table speeds from 40 mm per minute to 1000 mm per minute to set the optimum cutting parameters. The controls on the operator’s pendant throws many operational advantages.
Through the same VFD of the ETDU, it is possible to control the cross feed unit (ideal for machining cross verse in table stationary position) and the vertical feed unit (ideal for vertical machining and drilling in table stationary position). It may be noted, being a common VFD, any one axis can be used at a given time through a selector switch mechanism, which is an in-built safety measure by itself.
Right angle attachment, in combination with cross feed and vertical feed, adds floor boring capabilitiesto your converted planomiller! Jobs, which otherwise, should have been done in a floor borer, can be done in a converted plano miller.
Right angle attachment has a Circular T slot based flange, which has a graduated collar. This enables you to set the spindle axis of the right angle attachment to any angle ±360°. In other words. You can machineall the 4 sides of a rectangular job in the same setting with the help of a right angle attachment.
When introduced in between the tool post carriage of your planer and the seating base of the milling head,an intermediary back platefacilitates setting the spindle axis ±45°, so that you can machine the profiles like tapers etc. Back plate enables easy setting of the spindle axis with respect to the machine table in right angles. It also facilitates full utilization of the quill stroke of the milling head spindle. It is possible to mechanize the tilting mechanism through an integral sector gear and worm mechanism.
The drive mechanism of the ECONOMY MILLING HEAD (MHE-5)consists of is a single stage reduction gearbox and a stepped timer pulley & belt mechanism. This milling head is without a quill movement and, therefore, it has to be mounted on the clapper box of the existing tool post of the planing machine. Using the same sliding mechanism of the tool post, you can set the depth of cut. The existing circular T slot based tilting mechanism in your tool post will continue to provide ± 45° the tilting mechanism to the milling head, after mounting the milling head. This milling head is designed specially for small jobbing shops, where investment is a constraint. MHE-5 is not suitable for heavy material removal from hard and work hardening type of metal. This milling head can also be used for mounting on the tool post carriages of lathes (for operations like slot milling, key way milling, peripheral drilling etc). Since this is a very robust and proven milling head, it can also be used in the milling and drilling SPMs.
MHR series milling headsare all geared milling heads. They are the most rugged and well proven. MHR series milling heads are with 6 stepped spindle speeds and these speeds are achieved through change gear pairs provided. Change gear method helps to reduce the weight and the price of the milling head. Since changing of the cutter is not frequent in a planomiller (like in a milling machine), users do not feel it inconvenient to change the spindle speeds through change gear pairs.
MHCL milling headsare with 4 spindle speeds and you can select the required spindle speed through a convenient lever changing method.
What information should I furnish to get an offer?
- Make and size of your planning machine
- What is the max dia of cutter you wish to deploy?
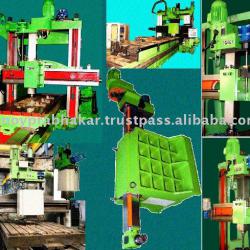
Packaging Detail:wooden cases |
Delivery Detail:2-3 weeks |