Nonmetallic Minerals Powder Surface Coating Production Line(Stearic acid coating machine ( high-speed mixing machine)
Place of Origin:Shandong China (Mainland) | Brand Name:ALPA |
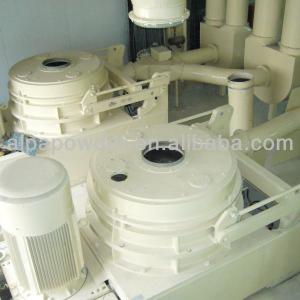
Process Features
♦ Surface coating smallest coating agent to get highest coating rate.
♦ Both continuous process and batch process are available.
♦ Coating agent includes stearic acid, coupling (Titanate coupling, Aluminate coupling, phosphate coupling, and silane coupling)
♦ Several different coating machines available.
♦ We can supply tailored solution according to different material characters and different product application.
♦ Coated material has four functions, dispersion, reduced viscosity, increased filling, and Interface mechanics function.
♦ The whole system has convenient operation, high automation, high efficiency and low production cost.
♦ Wide application and can achieve expected activation effect for various inorganic mineral materials.
Process Introduction
Continuous Process
1.Classic Process: ( used by world-famous mineral processing factory)
Process Flowsheet: Double Pin Mill + Dispersion Machine
2.Standard Process (Recommended by world-famous equipment company)
Process Flowsheet: Double Pin Mill Coating Process
Model/Output/ Fineness | 250 | 400 | 630 | 800 |
D97:5um | 300kg/h | 700kg/h | 1800kg/h | 3000kg/h |
D97:10um | 500kg/h | 1300kg/h | 3300kg/h | 5800kg/h |
D97:15um | 600kg/h | 1600kg/h | 4000kg/h | 7200kg/h |
Note: the data above is on the base of GCC coating.
3.Simple Process (Popular in China)
a. Three-roller Continuous Coating Process
Model | 200 | 3/300 | 3/600 | 3/900 |
Output D97:10um | 150kg/h | 1.5T/h | 3T/h | 6T/h |
Motor | 11km | 55.5kw | 111kw | 225kw |
Note: the data above is on the base of GCC coating.
b. Process Flowsheet: Turbo Mill Coating Process
Model | Fineness | Output | Power |
480 | D97:10um | 1.5T/h | 45KW |
750 | D97:10um | 3T/h | 75KW |
Note: the data above is on the base of GCC coating.
Batch Process
High-speed Mixer + Classifier (Or Mixer) Process
Process Features
♦ Surface coating process: raw material would be dosed into high-speed mixer or continuous coating machine, mixed and heated (moisture < 0.3%). Coating agent would be added in liquid or after atomization. The material and coating agent get mixed in high-speed mixing. Coated powder would be sent to classifier to remove big particles.
♦ The choice of coating agent and dosage depend on product character, fineness (or specific surface area) and product application. For example of kaolin, for 20-45micron powder, the dosage should be 0.3%-0.5%; for 5-20micron powder, the dosage should be 0.5%-0.8%; for 2-5micron powder, the dosage should be 0.8%-1.0%.
♦The temperature and time of coating is adjustable, and recipe can be applied in wide cases.
♦ In high-speed movement, material would be heated and coated with coating agent, which make material heated evenly and also improve coating rate. The dosage of coating agent reduced, and coating cost reduce.
♦ Classifier connected with coating machine can remove aggregate from coating effectively, and improve coated product quality and ensure performance of coated product.
♦ The inside of machine would be protected for wear resistance, which improve life time and also ensure purity.
Applications
Calcined kaolin, GCC, quartz powder, talc, wollastonite, PCC, white carbon black, alumina, magesite, magnesium hydroxide.
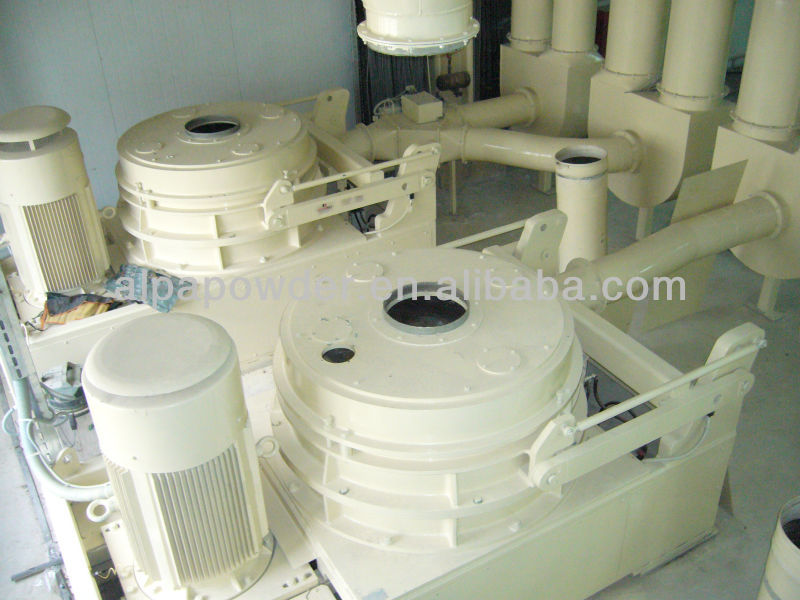
Packaging Detail:Wooden or steel package |
Delivery Detail:30 days ~90 days |