Liquid Filling and stoppering machine
Place of Origin:Shanghai China (Mainland) | Brand Name:Rotech | Model Number:HGS-120 |
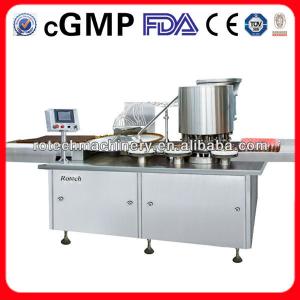
Liquid Filling and stoppering machine
Design and Manufacturing According to FDA&cGMP Standard
Liquid Filling and stoppering machine
It is complete with:
FRAME
Base manufactured in steel with AISI 304 stainless steel panels. Parts mounted to the working surfaces are manufactured in AISI 304 st. st. and sealed to prevent infiltration of product into internal mechanisms.
The machine is mounted on legs with stainless steel adjustable feet at height of 200 mm. to allow easy cleaning operations.
The height of the working desk is: 925 +/- 25 mm.
All parts in contact with the product are manufactured in AISI 316L stainless steel.
Machine motorization by speed variator.
VIAL FEEDING UNIT
For the transport of vials through their way on the machine, the following items are supplied:
- Motorised conveyor belt.
Frame of sanitised design to facilitate cleaning operations, complete with st. st. borders adjustable in width and height.
This conveyor is raised from the machine surface to facilitate cleaning operations.
The conveyor belt is divided in two parts to allow the handling of two bottles each time.
- No. 2 Arnite star-wheels to stop the bottles under the two dosing wheels (one in front of the other).
- No. 2 Arnite star-wheels to stop the bottles under the two stoppering wheels (one in front of the other).
Vial exit onto conveyor belt.
LIQUIDFILLINGSYSTEM:
This unit is prepared to dose with liquid two bottles per time.
It is complete with:
No. 1 AISI 316L SS main container with blade stirrer, equipped with tightened lid and flange to connect to the charging system pipe.
Optical system to control the liquid level.
The container is easily disassemblable to allow the cleaning and steam sterilising operations. It is equipped with electronic level control, which drives the liquid feeding and stops the machine in case of product low level.
No. 1 AISI 316L SS intermediate hopper with blade stirrer and doctoring blades in F.D.A. approved Delrin material.
No. 2 AISI 316L SS filling wheels, each provided with 2 dosing ports and 2 filling needles.
Note: The wheels and the dosing pistons can be easily disassembled for cleaning and sterilising operations.
STOPPERING UNIT
This unit is placed on the machine conveyor belt, after liquid filling unit, and it is used for the insertion of rubber stoppers into dosed vials.
It is complete with:
No. 1 AISI 316 SSvibrating bowl, at double exit.
No. 1 Linear vibrator complete with a AISI 316 vertical chute for stopper feeding to the vertical feeding wheel.
No. 1 Double vertical wheel for stopper feeding to the heads of the application wheel.
No. 2 AISI 316L SS application wheels for stopper taking, by vacuum, and inserting into the vial mouth.
Stoppering operation description
Rubber stoppers are contained into an AISI 316 stainless steel vibrating bowl.
They are fed to a AISI 316 stainless steel charging chute (with a vibrator) and by means of 2 small vertical wheels they are transferred to the heads of the application wheels.
Rubber stoppers are retained in the heads of the application wheels by vacuum until they are into the bottles mouth.
TECHNICAL DATA
Uitable bottle range | 2~250ml glass or plastic bottles (change the proper change part) |
Filling error | ≤1.5% |
Auto stoppering ratio | ≥99% |
Power supply | 220V/380V 50Hz |
Power | 1 Kw |
Speed is controlled | Speed is controlled by inverte |
Vacuum degree | -6×10-2Mpa 14m3/h |
Single machine noise | ≤70dB |
Weight | 400Kg |
Dimension | 1680×1000×1750(mm) |
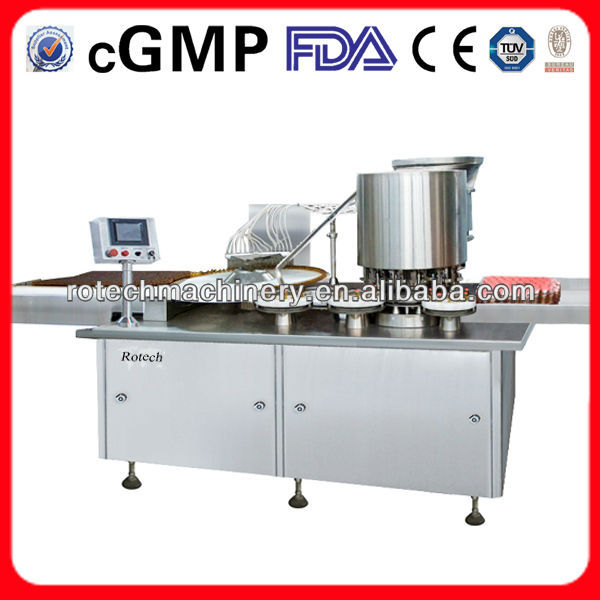
Packaging Detail:International Export Wooden Case Packing, Water Proof |
Delivery Detail:Delivery it in 2 month after received the downpayment |