Lead edge feeder high-speed flexo printing slotting die cutting with stacker
Type:Flexographic Printer | Condition:New | Plate Type:water ink | Place of Origin:Hebei China (Mainland) |
Brand Name:Xinhua | Model Number:ZYKM490*2600 model | Usage:Card Printer | Automatic Grade:Automatic |
Color & Page:Multicolor | Voltage:380V 50HZ | Gross Power:18.5-30 | Dimensions(L*W*H):16m 5m 2.3m |
Weight:24-30 | Certification:CE certificate and ISO 9001 | After-sales Service Provided:Engineers available to service machinery overseas | Color:Optional |
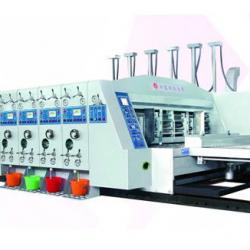
1 technical parameter
2 requirement
a, feeding unit
b, printing unit
c, slotting unit
d, die cutting unit
e, stacker
f , main part brand
1.technical parameter
A.model: ZYKM490×2750 (feeding size)
B.Max. feeding size of cardboard standard: 1500×2500
C.Min. feeding size of cardboard standard: 380×680
D.Max. printing size:1500×2600
E.Max mechanical speed:120pcs/min
F.feeding roller outer diameter:(upper roller131mm;rubber)down roller175mm
G.printing thickness:5-7mm
H.outer diameter of embossing roller:175mm
I.outer diameter of up leading axle:85mm
K.outer diameter of down leading axle175mm
L.outer diameter of press mark roller::110mm
lead edge feeding unit
1.Lead edge device | A.lead-edge feeding device, feeding accurately, fast. B.Lead edge feeding is putting cardboard width ‘s front side as locating datum, that doesn’t be affected by the cardboard cutting width error, conform to the printer, slotter, die cutter’s locating datum requirement. Electric adjust retaining box position. C. High ability to deal with the cardboard bend D. High ability to deal with thin cardboard conveying,( E and B flute cardboard can feed smoothly.) E . Blowing rate of inlet scoop is controlled by frequency converter, according the cardboard size, bend degree to adjust blowing rate, adjust conveniently, fast. The winder is 11kw. F.Brake, clean-dust |
2machine separate | A. button switch electric control lonely machine separation and combination, and with an automatic alarm device, in the moving process, that continued ringing warning, to ensure the safety of the people. B.Pneumatic interlocking device, firm locking, convenient and accurate. |
3,feeding roller | A. Up Feeding roller use single inserting groove rubber , to make balance rectifying, ensure feeding smooth and steady, good precision. B. Down Feeding roller use embossing steel roller, hard-chrome plating, wear-resisting, movement balance adjustment. C.Up and down feeding roller use cross-shaped driving micro adjusting device, spanner adjusting, dial showing, adjusting convenient, self-locking.. |
4.Automatic reset, return-zero device | A.The whole machine returns zero ,push the zero switch, convenient for change-order operation, short the change- order time, reduce waste of cardboard |
5.Phase fixed system | A. pneumatic brake device. B. Every unit of the whole machine separating, original.meshing point of transmission gear unchanged |
printing unit
1.printing roller | A. Printing roller use high quality steel, surface grinding, hard-chrome plating, axial has central datum line , cycle direction has sticker version datum line. B. Dynamic balance adjustment, stable operation C. Ratchet fixed volume edition axis with hanging-plate gutter, that can fit fast changing plate. D. High precision planetary phase adjusting mechanism, dynamic, static(moving and stopping) can both make 360 degree positive and negative adjustment. E. Printing roller axle direction adjusting device, Max. movement is±7mm |
2.embossing roller | A. Embossing roller adopts high quality seamless steel tube processing,dynamic balance correction, stable operation ,surface grinding, with hard chrome plating. B. Embossing roller use cross-shaped driving micro adjusting device, spanner adjusting, dial showing, adjusting convenient, self-locking.. |
3.metal anilox roller | A.Haili anilox roller(number180-300 ) B. Pneumatic anilox roller automatic lifting device and idle equipment, when feeding paper, anilox roller fall down and touch with the printing plate , and when stop feeding paper, anilox roller automatic rising and separate from the printing plate, in order to protect the plate, prevent the ink dry. C. High quality seamless steel pipe processing,dynamic balance correction. Surface grinding, hard chrome,custom made the net shape. |
4.rubber roller | A. High quality seamless steel pipe processing,dynamic balance correction B. Steel tube surface has high quality wear-resistant rubber, long using life. C. High grinding surface. that suitable net point high precision and large area printing. D.Micromatic setting, that ensure ink equably. |
5.ink -supply system | A.Automaticdiaphragm pump,operate easily, repair conveniently, ink supplying stably. B.Auto cleaning, and auto supplying ink. |
6. phase adjustment structure | A. Inner planet gear, feature: touch area is large, big transfer torsion, low noise B. Electric adjust printing plate 360degree position(at any run or stop process) C. Printing phase. Encode digital control |
7.phase fixed system | A. Pneumatic brake device B.when machine separating, original mesh point of transmitting gear will not change. |
slotting unit
1. Operation and control | A. PLC control to adjust slot gap, slotting phase and box height size. B. Equipped with emergency stop and whole machine inching device, that ensure operation safely. C. Multipoint control feeding paper and stopping, operation conveniently, reduce the waste of cardboard. |
2. slotting phase and box height adjustment | A. Adopt high precision inner star wheel structure, to complete 360degree adjustment of slotting phase. B. Push the return zero button, slotting knife returns to be zero, change order conveniently , short the change order time, reduce the waste of cardboard. |
3. press line wheel | A. High quality seamless steel pipe processing,surface grinding and hard chrome plating. B. dynamic balance correction, operation stably, that suitable for high speed operation. C. Pressing line wheel adopts point pressing type, pressing line effect is good. |
4. slitting, slotting and knife holder | A. Slotting knife thickness7mm,9SiCr high quality alloy steel with heating treatment crescent type slotting knife, high hardness, good toughness and wear resistance. B. 9SiCr high quality alloy steel slitting knife, knife sharp, and slitting smoothly. C. Slotting knife holder, pressing line wheel holder and pre-pressing wheel shaft electric synchronous adjustment, encoder control position, touch screen adjust directly and display specific size. |
5. the gap adjustment between the slotting and rolling line | cross slide micromatic setting, electrical adjustment, PLC control. Text display. Adjust conveniently, and self-locking. |
4.die cutting unit
A.Electric adjustment phase (die cutter )position. |
B.Die cutter rubber pad roller has automatic linear speed compensation device, to rectify the die cutter error of rubber cushion wear, axle direction automatic move left and right 60mm device |
C.Die cutter roller can move left and right±20mm |
D.Equipped With rubber grinding device, rubber cushion can use again and again, lengthen the life of rubber cushion |
E. Cleaning device |
5.Auto stacker
A .paper-receiving arm can be operated by hand ,the receiving paper height can be choosed freely. |
B.paper-receiving arm belt can adjust the tension and loosen lonely. |
C.receiving paper platform rise and fall are driven by the powerful chain |
D.receiving paper platform is automatically adjust the inclination according to the cardboard rising, the rising motor with electrical braking function, so the platform can keep the fixed position. |
E.paper plate with pneumatic action, when the cardboard get the predetermined height,it can hold out automatically |
F.1600mmthe cardboard piling height is 1600mm |
G.transfer belt driven motor 2.2kw(adjust the speed and control) 1set |
H.elevator motor3kw×1 set |
I.receiving paper arm cylinder80×300(with three five way electromagnetic valve |
J.The system is 5.5 meters , that has the receiving paper part, transmission part, collecting paper, connected with friction belt to transfer the cardboard, paper receiving part is the cylinder lifting, fasten the belt wheel lonely. |
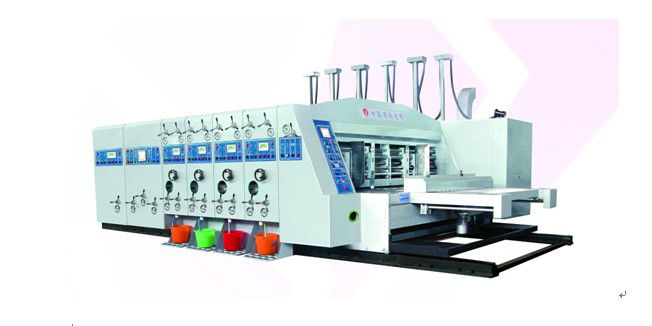
Packaging Detail:Common packing according to the clients' requirements |
Delivery Detail:after 50 days upon receipt the 30% deposit |