Large anti-reflective and conductive inline magnetron sputtering coating line
Type:Coating Production Line | Substrate:Steel | Coating:Vacuum Coating | Place of Origin:Hunan China (Mainland) |
Certification(s)::ISO9000 |
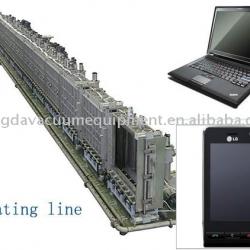
Large anti-reflective and conductive inline magnetron sputtering coating line:
Large anti-reflective and conductive inline magnetron sputtering coating machine
The anti-reflective continuous magnetron sputtering coating line has 15 vacuum chambers, among which, one entrance chamber, one exit chamber, one entrance buffering chamber, one exit buffering chamber, one entrance transfer chamber, one exit transfer chamber, two transfer chambers and seven sputtering coating chambers. Each sputtering coating chamber can be equipped with four cathodes simultaneously. The high vacuum chamber is separated by plug valve and can realize the multi-functional coating through changing the atmosphere separation; the carrier is driven by magnetic steering; the equipment has 26 sets of turbo-molecular pumps and 13 sets of mechanical pumps to get the stable pumping speed and even distribution of air.
1.Technical characteristics of production line
- The production line has used the uniformity control device for deposit thickness of large area sputtering and realized the adjustment of uniformity according to situation of production.
- The production line can produce SiO2 layer through using the control technology of piezoelectric valve and closed circuit ring.
- The production line can produce SiO2 layer through using the control technology of piezoelectric valve and closed circuit ring.
- The production line has adopted the advanced plug valve to separate the chambers and can realize the effective separation and stabilize the process gas. In China, our company is the only one which is able to design and process the plug valve. Benefiting from the plug valve, the design will have better sealing effect and be more durable.
- The production line has the design of even intake pipe structure, thus the air intake is even and stable.
- (5) The production line has adopted the advanced magnetic steering drive system; the carriers move steady.
- (6) Electrical control system: taking advantages of touch screen, PLC automatic control and human-machine dialogue, realize the data display, operation and control of system.
Layer Material | L | H | L | H | ITO | |||||
Sio2 | Tio2 | Sio2 | Tio2 | Glass | Tio2 | Sio2 | Tio2 | Sio2 | ITO | |
1 | Glass | Sio2 | ITO | |||||||
2 | Sio2 | Glass | Sio2 | ITO | ||||||
3 | Sio2 | Tio2 | Glass | Sio2 | ITO | |||||
4 | Sio2 | Tio2 | Glass | Tio2 | Sio2 | ITO | ||||
5 | Sio2 | Tio2 | Sio2 | Tio2 | Glass | Tio2 | Sio2 | ITO | ||
6 | Sio2 | Tio2 | Sio2 | Tio2 | Glass | Tio2 | Sio2 | Tio2 | Sio2 | ITO |
2.Main technical parameters
Final vacuum | 6 × 1 0E-4 Pa |
Average production cycle | 80180 seconds / frame |
Carrier size | 850 × 1500 (mm) (can be customized on request |
Film uniformity | ± 3% |
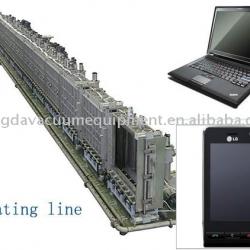
Packaging Detail:Standard package |
Delivery Detail:150-180 days after receiving prepayment |