KZO-330 ASP air separation equipment
Condition:New | Type:Air Separation Plant | Product Type:heavy machinery | Place of Origin:Zhejiang China (Mainland) |
Brand Name:siadgas | Model Number:KZO-330 ASP | Voltage:380V/220V three- phase AC | Power(W):~480KW (name plate) |
Weight:according to real conditions | Dimension(L*W*H):according to real conditions | Certification:ISO9001:2000 ISO14000 | Warranty:one year |
After-sales Service Provided:Engineers available to service machinery overseas | colour:whiteand could be changed according to clients' requirements | installation and operation:easy and convenient | power consumption:low and energy-saving |
after-sales service:professinal and qualified | running period:12~24months | running life:20~30 years | testing:on-site commisioning |
start-up time:24Hs | control system:PLC or DCS | operation:automatic |
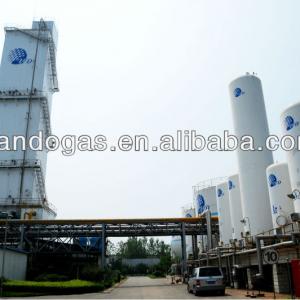
1.Technical Property( KZO-330 ASP air separation equipment) :
Production, Purity, Pressure (Outlet the Cold Box): | ||||
medium | Production(Nm3/h) | Purity | Pressure(MpaG) | |
Oxygen | 330±5% | ≥99.6%O2 | ~15 | |
Product Production State(0ºC, 101.325Kpa) | ||||
Start-up pressure | 1.0MPa(G) | |||
Running period | 12Months | |||
Start time needed | ~10Hs |
Notice:all the output can be designed according to customer’s requirements.Our KZO model production ability range from20~500.Above is just for your referrence. If you have any questions, please feel free to cantact us.
2.Product name: KZO-330 ASP air separation equipment
A complete set of air separation equipment is composed by air filter, air compressor, pre-cooler( pre-cooling system), refrigeration units, molecular sieve purifier(purifying system), fractionating column, turbo expander, instrument control.
Food packing, Food storing, Electric & Electronic industry, Petro-gas & Oil field, Chemicals & Petro-chemicals, Coal-mine, Metallurgy, Pharmacy, SMT, Fire-resistance, lab, Air driving, and so on...
1. Metallurgy: For anneal protection, agglomeration protection, nitrogenizing, furnace washing and blowing, etc. Used in fields such as metal heating treatment, powder metallurgy, magnetic material, copper process, metallic mesh, galvanized wire, semiconductor, etc.
2. Chemical and new material industries: For chemical material gas, pipeline blowing, gas replacement, gas protection, product transport, etc. Used in fields such as chemical ,urethane elastic fiber, rubber, plastic, tyre, polyurethane, biological technology, intermediate, etc.
3. Electronic industry: For encapsulation, agglomeration, anneal, deoxidization, storage of electronic products. Used in fields such as peak welding, circumfluence welding, crystal, piezoelectricity, electronic porcelain, electronic copper tape, battery, electronic alloy material, etc.
6. What we promise?
1. professional and quick on-line service
2. first-rate products and competitive price
3. unparallable after-sales service
4.OEM and on-site commissioning
Technical Information | Your kind requirement |
1).Altitude( above the sea level) | |
2).Output | |
3). purity | |
4).Temperature and Pressure (outlet the coldbox) | |
5). Voltages and Frequency |
Dear customs,
If you have any special requirements, please have no hesitance to contact us and we will spare no efforts to satisfy you!
more knowledge about ASP:
An air separation plant is an industrial facility that separates naturally occurring air, or atmospheric air, into its component gases. The gases harvested in the process include oxygen, nitrogen, and argon, as well as some inert gases such as neon, xenon, and krypton. Since nitrogen and oxygen are the two most common gases in the earth's atmosphere, these two elements make up the bulk of the gases harvested in this process.
The process employed in an air separation plant is calledcryogenic distillation. By cooling the atmospheric air to extremely low temperatures, the component gases can be separated and harvested. Liquid forms of nitrogen or oxygen may also be harvested at some plants.
The cryogenic distillation process is a four step procedure.
In the first step, atmospheric air is cleaned and compressed to a pressure range of 5 to 10 bars (4-9 atmospheres). The cleaning process removes dust and contaminants that could interfere with the cooling process. The compression process heats the air to remove traces of moisture before passing thecompressed airto a heat exchanger for cooling.
When the compressed air has been cooled, the next step is purification. This process involves passing the air through a molecular sieve, which filters the air by a process called adsorption. In this process, gases or molecules are attracted to an adsorbent surface and form a layer on top of the adsorbent material. The molecular sieves are designed to removecarbon dioxide, water, and hydrocarbon gases.
After the air is purified, it can safely be passed to the cooling and distillation chamber. The cooling chamber consists of a heat exchanger and cryogenic streams. When the air is passed through this chamber, it reaches sufficiently low temperatures to enable distillation of the component gases.
The distillation of the air occurs in the distillation column. Depending upon the gases to be harvested, the air may pass through more than one distillation column. This component usesrefrigerantand an expander or valve to generate a Joule-Thomson effect, which causes the component gases of the air to cool and reach a liquid state. The liquefied gases are then collected and warmed to ambient temperature for storage or use.
The gases produced by an air separation plant are used in many industrial processes. In some cases, these gaseous forms of these elements are transported to industrial users via direct pipelines. In other cases, the harvested elements may be stored in the liquid or gaseous forms for later transportation and use. Larger quantities of the distilled gases are usually transported in their liquid forms by tanker trucks. Smaller quantities may be transported in pressurized cylinders as a gas.
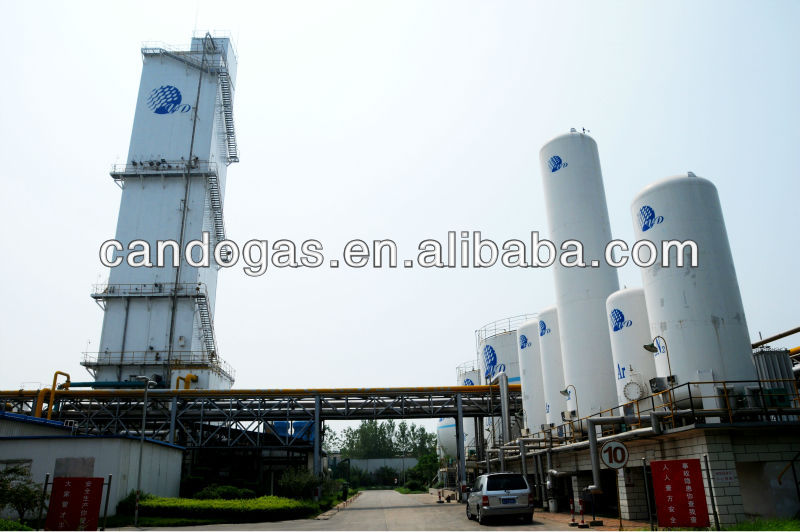
Packaging Detail:package: 1.standard packing for export 2. we can pack according to custmer's requirements |
Delivery Detail:dlivery:2-3 months after receiving deposits |