Hot Selling Type 900*1800mm Energy Saving Small Dry or Wet Ball Mill
Condition:New | Type:Ball Mill | Motor Type:AC Motor | Power(W):18.5 kw |
Capacity(t/h):0.65-2 t/h | Place of Origin:Henan China (Mainland) | Brand Name:Libo | Model Number:ball mill 900*1800mm |
Dimension(L*W*H):dia 900*1800mm | Weight:3.6t | Certification:ISO9001:2000 | Warranty:1 year |
After-sales Service Provided:Engineers available to service machinery overseas | colour:customizable | material in size:less than 20 mm | material out size:0.075-0.89 mm |
rotational speed:38r/min |
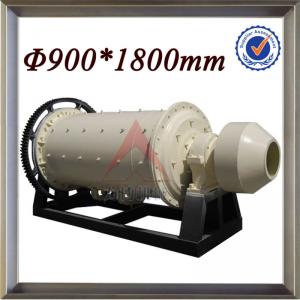
900*1800mm Energy Saving Dry or Wet Small Ball Mill
Structure and Advantages ofBall Mill
Theball millis composed by feeding part, discharging part, rotation part and driving part (reducer, small driving gear, electric motor and electric control).
The energy savingball millwe produce is different from the original ball mills, we make the body and chassis integration which makes it easy to place the machine on the ground. Compared to the traditional ball mill, the energy savingball millcan reduce the consumption by30%, and the motor power by18%-25%. It can save lubricating oil about70%and the production capacity can be increased by15%-20%. Under normal circumstances, users have no need to change the main bearing within10 years.
And theball millhas advantages as follows:
(1).Easy maintenance and operation;
(2).Big crushing ratio, uniform end product size;
(3).Simple structure;
(4).effectively avoid the pollution of heavy metals
Working Principle ofBall mill
Ball mill,a kind of horizontal drum-type rotating device, is a grate mill with external gear and double bins.
1.Materials shall be evenly charged through quill shaft in feeding device into the first bin, which has step or waved lining with steel balls in different specifications.
2.Steel balls are taken to a certain height by centrifugal force from drum rotation and then fall. Thus it will give a heavy blow to materials, playing a role of grinding. 3.Materials after crushed in the first bin shall enter bin across single-layer diaphragm into the second, which is provided with flat lining with steel balls, to go through further grinding.
4.Powder shall be discharged from discharging grating, ending the milling process
Main Technical Parameters ofBall Mill
certification and type | rotational speed(r/min) | put the ball to heavy(t) | material-in size(mm) | material-out size(mm) | yield(t/h) | motor power(kw) | weight(t) |
Φ900*1800 | 38 | 1.5 | ≤20 | 0.075-0.89 | 0.65-2 | 18.5 | 3.6 |
Φ900*3000 | 38 | 2.7 | ≤20 | 0.075-0.89 | 1.1-3.5 | 22 | 4.5 |
Φ1200*2400 | 32 | 3.8 | ≤25 | 0.075-0.6 | 1.5-4.8 | 45 | 11.5 |
Φ1200*4500 | 32 | 7 | ≤25 | 0.074-0.4 | 1.6-5.8 | 55 | 13.8 |
Φ1500*3000 | 27 | 8 | ≤25 | 0.074-0.4 | 2.0-5.0 | 90 | 17 |
Φ1500*4500 | 27 | 14 | ≤25 | 0.074-0.4 | 3.0-7.0 | 110 | 21 |
Φ1500*5700 | 27 | 15 | ≤25 | 0.074-0.4 | 3.5-8 | 132 | 24.7 |
Φ1830*3000 | 24 | 18 | ≤25 | 0.074-0.4 | 4.0-10 | 180 | 28 |
Φ1830*7000 | 24 | 25 | ≤25 | 0.074-0.4 | 7.5-17 | 245 | 36 |
Φ2200*5500 | 21 | 30 | ≤25 | 0.074-0.4 | 10.0-22 | 370 | 48.5 |
Φ2200*6500 | 21 | 31 | ≤25 | 0.074-0.4 | 14-26 | 380 | 52.8 |
Φ2200*7500 | 21 | 33 | ≤25 | 0.074-0.4 | 16-29 | 380 | 56 |
Φ2400*4500 | 21 | 30 | ≤25 | 0.074-0.4 | 8.5-60 | 320 | 65 |
Φ2700*3600 | 20.6 | 39 | ≤25 | 0.074-0.4 | 12-70 | 400 | 91.3 |
Φ2700*4000 | 20.7 | 40 | ≤25 | 0.074-0.4 | 12-80 | 400 | 94 |
Φ2700*4500 | 20.7 | 48 | ≤25 | 0.074-0.4 | 12-90 | 430 | 102 |
Φ3200*4500 | 18 | 65 | ≤25 | 0.074-0.4 | according to process conditions | 800 | 137 |
♥ Warmth Warning:
How to add steel balls into the ball mill according to ball size ratio?
Generally, the ball mill of new installation has a run-in process. In the process of running in, the amount of steel ball added into the ball mill account for about 80% of the maximum loading ball. The proportion of steel ball can be determined by the ball size(Φ120mm,Φ100mm,Φ80mm,Φ60mm,Φ40mm).
Different models of ball mill has different need of ball quantity. Let’s take 1500*3000 for an example, it’s maximum loading ball 9.5-10tons. For the first time the big steel balls (120mm and 100mm) accounted for 30%-40%, medium size balls (80mm) accounted for 40%-30%, the small balls (60mm and 40mm) accounted for 30%.
Someone may ask: why do you suggest to add only 80% steel balls in the running in process of ball mill? That’s because the gears need to mesh after installation of ball mill. The capacity(ore quantity) is gradually increased in the process of production. After the ball mill normally run for two or three days, stop the machine and check the meshing situation. If everything is going well, you can open the hole cover of ball mill to add the remaining 20% steel balls.
Note: the small balls are just added in the first time of adding balls. Under normal circumstances, there is no need to add small balls at ordinary times. If the fineness of grinding mill machine can’t meet the requirement of flotation, you can add an appropriate amount of small balls. When the operation of ball mill is normal, the friction between steel ball and steel ball, steel balls and ores, steel balls and mill liners will make abrasion increases. It follows that the bigger balls become medium size balls, the medium balls become small balls.
Steel ball size proportion: If the diameter of ball mill is below 2500mm, it can be configurated the steel balls with diameter of 100mm, 80mm and 60mm. If the diameter of ball mill is more than 2500mm, it is suitable for the steel balls with diameter of 120mm, 100mm, 80mm.
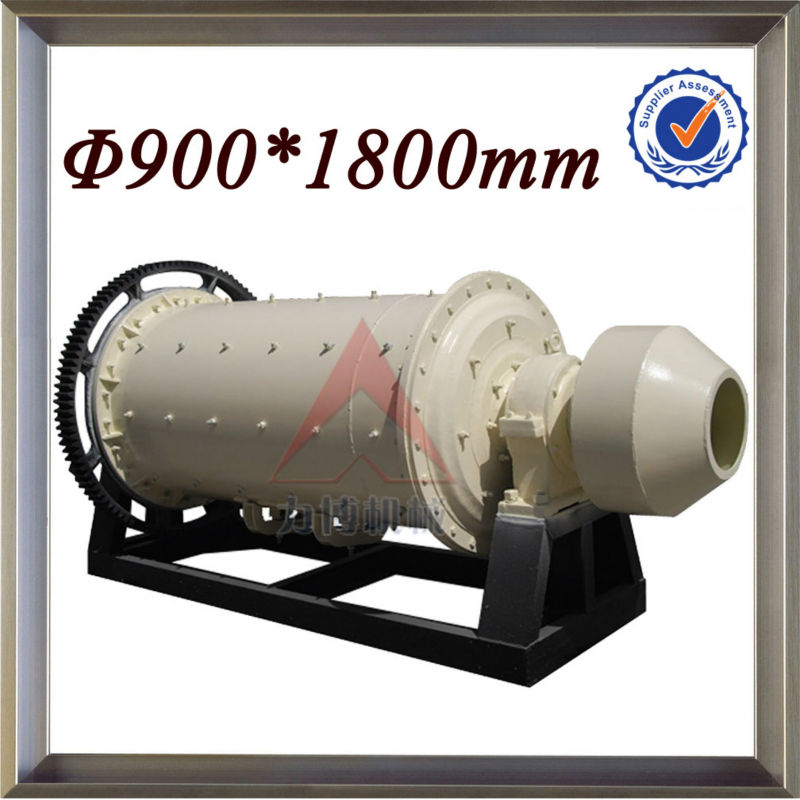
Packaging Detail:export standard |
Delivery Detail:15-30 days |