Gypsum board manufacturing plant
Place of Origin:Shandong China (Mainland) | Brand Name:Tengfei | Model Number:TFGB2013 | Consumption:Lower |
Efficient:Heigher | Working time:24hours/day 300days/year | Drying type:Heat exchager | Gypsum board production line technology:Heat exchanger |
Fully automatic:Operation | Easy:Maintenance |
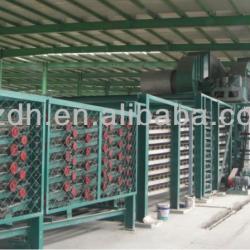
Gypsum board manufacturing plant adopts the German company, Lafarge, the United States companies and domestic well-known enterprises Kitashinchi Group, Taihe Group advanced technology. We adopts the horizontal flow, vertical airflow heat exchanger heating system, the raw material feeding system and edge cutting and edge sealing and edge grinding and recycling system and stacking system are all controlled by computer. All the whole line is full automation.
1. Capacity 2 million m2/year~50 million m2/year
2. Automation Fully automatic
3. Drying system Using hot air for drying(Heat exchanger)
4. Fuel Coal, natural gas, heavy oil and diesel oil
5. Main materials
Construction gypsum powder, modified starch, protective paper, foaming agent, water, white latex. Fiberglass and paper pulp (adding selectively according to different raw materials and kinds of products) Quantity of raw material required for producing per m2 gypsum board (referenced data) (thickness based of gypsum board: 9.5mm)
Gypsum powder(CaSO4·1/2H2O) | 6.8kg/m2 |
Protective paper | 0.48kg/m2 |
Modified starch | 0.035kg/m2 |
Foaming agent | 0.008kg/m2 |
White latex | 0.005kg/m2 |
Fiberglass (used selectively ) | 0.025kg/m2 |
Electricity | 0.3kwh/m2 |
Water | 4.8kg/m2 |
Heavy oil | Heat consumption~3800kcal/m2 |
Natural gas | Heat consumption~3800kcal/m2 |
Performance index of all materials (referenced data)
6. Dimension of product:
Thickness 8mm-22mm
width 1200mm or 1220mm
length 2400mm~3600mm
we can design and manufacture products of other dimensions as clients’ special requirement.
7. Standard of product quality
In conformity with national standard GB9775-2008
8. Category
a) Common paper surface gypsum board
b) Fireproof paper surface gypsum board (H)
c) Waterproof paper surface gypsum board (S)
9.The follwoing are all the required system
9.1Raw material supplying system
Raw material is transported and lifted to feeding hopper, after measurement it comes to vertical mixer. Face and back paperboard are lifted to each shelf. They are tensioned with special tension unit. Mixed material from vertical mixer falls down to back paperboard, then formed into shape and covered with face paperboard, after last flattening the semi finished plasterboard is completed.
9.2.Mixer
It will mix the raw material completely.
Vesicant and starch and powder and water will be blended in the mixer.
9.3.Conveying system
Conveying and Concreting
Semi-finished plasterboard from formation section is automatically edge trimmed into continuous palsterboard, conveyed to concreting station and automatically cut.
9.4.Transferring system
Transferring section
Concreted plasterboard automatically transferred and cut in middle, saving raw material.
9.5Drying system
Drying room
Plasterboard Transferred automatically into drying room which has shelves 5-storey or 6-storey supporting 2 lapped sheets, with 50m, 60m, 70m, and 90meters length range.
9.6Stacker system
Finishing section
Automatically cut into dimensions you pre-set to avoid defect product occurrence and higher efficiency.
9.7 Gypsum board controlling system
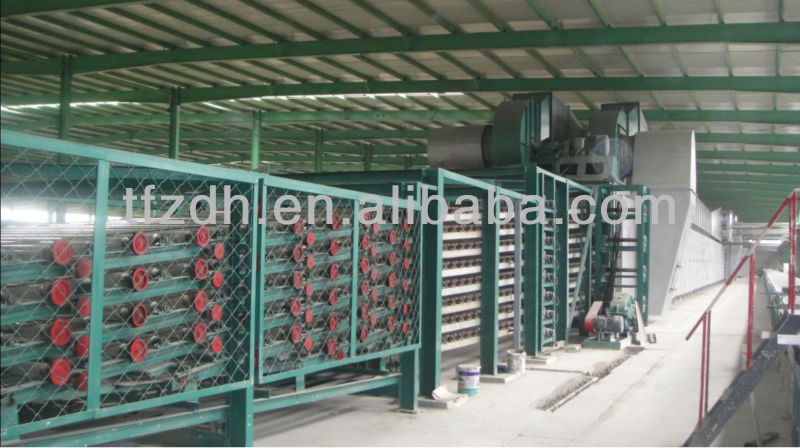
Packaging Detail:For the gypsum plasterboard manufacturing machine ,It needs from 8-18sets 40feet container according to different capacity of the line. |
Delivery Detail:In 3-5 months |