GM3 CNC Sole Milling Machinery for pre-finished sole
Place of Origin:Manisa Turkey | Brand Name:Goksu Machinery | Model Number:GM3 |
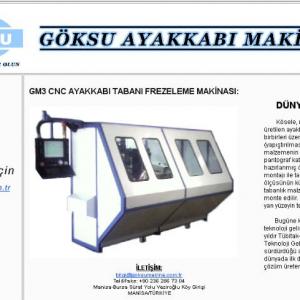
THE FIRST IN THE WORLD!..
Sole of shoe, which is produced from leather, rubber and neolith materials are produced by combining the different materials to each other. Vardola and pantograph layers are being assembled on the sole materials (leather etc.) and the heel, which is being prepared in the beginning at the outside, is assembled under the sole materials. The sole is formed by assembling the semi-layers. Other layers are designed larger than the sole materials for preventing the shrink of the sole size and they are assembled. When the assembling of these different layers have been finished, side surface have to be smoothed. Until now, a lot of technologies have been developed. But our company has developed a machine, which produces solution with CNC controller as a result of Research and Development workings by the supports of TUBITAK (The Scientific & Technological Research Council of Turkey) and TTGV (Turkish Technology Development Foundation).
The project consists of two phases. The fist one is GM3 CNC sole of shoe milling machine, which commands CNC controller to the mechanical parts. The other one is CAD&CAM (G-CAD V2.1) program which introduces the sole to the machine.
For operating the sole of shoe at the machine, G-code must be produced from G-CAD. G-code is suitable for using at a lot of part of the shoe production. The first phase of the code generation on the program is loading the model of sole to the G-CAD. By this program, model can be loaded with the scanner for the first time. This is the difference of this G-CAD from the other CAD&CAM programs in the market. From inside of the G-CAD, model is being scanned from the scanner. The program changed the model to the drawing automatically by scanning the model from the program scanner. By this way, the time lost and the mistakes which may be made with the method of punctuation from the digitizer at the other programs by CAD&CAM operator can be prevented. The produced drawing is being prepared for the other operations by entering the identity information. After this process, standard CAD functions as setting function (producing other numbers from the original sole number which is scanned), and mirror function ( producing right sole from left sole or left sole from right sole) are being used. And then, the programming for operating the sole as required is being made. It is determined according to the amount of rough shaving, angle and set that are needed. G-CAD starts the CAM function after this process and G-code is being generated automatically. Also, the possibility of watching the animation of the generated G-code exits into the G-CAD.
The code, which is being produced by G-CAD, is being loaded to the machine by RS232, Usb flash memory or Ethernet. Then, at the reference area the reference pipes of the sole is being made tangent from 3 points to the fixers (the modular sole holders which is being adjusted according to the different sole of machine) and then it is being tightened by giving start from the pedal. The cover of the working area is being closed and the machine takes the sole after giving start. And so, smoothing process is being realized by the generated code. When the process finished, the sole comes to the filling-discharging place. The operator takes the processed sole from the machine and gives the raw sole to the machine. By this way, the process goes on.
There are 3 semi-fixed spindles on the GM3. The first one is 12.000 rpm. spindle to which the spindle of the heel is connected. The second one is 5.000 rpm. spindle to which rough shaving spindle is connected. The third one is 4.000 rpm. spindle to which belt emery is connected.
The first spindle is being used to smooth and give shape to the front part of the heel. There is no angular moving at the spindle. The front part of the heel is being operated according to the program which is being arranged at the G-CAD (from the front part of the heel to the front part of the heel, from the head of milo to the head of milo, from the head of internal milo to the external front part of the heel).
The second spindle cleans rough shavings of the heel if the smooth rough shavings and the rough shavings of the whole environment of the sole or the rough shavings of the front part of the heel is wanted to take. This spindle has the property of moving angular between +10° and -35°.
The third spindle takes 0.2mm rough shaving for preparing the surface of the sole which is being smoothed by rough shaving and belt emery for painting and polishing. This spindle is connected to the upper surface of the same platform with the second spindle. Because of this, this spindle has the property of moving angular too.
By means of moving angular at 2nd and 3rd spindles:
The front part of the heel can be produced with 35° angle to the inside or 15° angle to the outside.
The back of the heel can be cut smoothly and angular which is being applied to the Western types of soles.
A shape of the front part of the heel is being produced which can be applied for the first time by this machine. We call this: “heel wave”. At this function, when the vardola part of the heel is the same with the original sole model, the cover part of the heel can be wavy. The machine gets normal rough shavings from the heel, and the wavy front part of the heel is being produced by moving angular the 2nd and 3rd spindles. This function is being made by defining at G-CAD; and is being programmed according to the grade and the number of the wavy at the heel that are needed.
The programs of 1000 different models can be kept in the memory by GM3. By calling the program from the memory will be sufficient for starting the process, although a lot of time passes from the ex-process. Also, the sole can be operated without needing any model from the present systems and there is no need to different adhesives for pressing the sole. By the modular fixers, the sole can be arranged according to sharp tips, circular tips, cornered tips and also right and left soles, splayed and narrow soles.
The machine realizes an average sole process at 30second/1 pair by doing all milling processes on the sole with one CNC operator (putting knifed to the spindle, the rough shavings and thin emery of the heel –out of the undercoat emery of the heel), the machine reaches 480 pairs of shoes capacities daily (8 hours). Because of this, an incredible price competition is being supplied as an advantage at the production. Also, the quality of process reaches to the ±0.01 mm standard deviation level which isn’t possible with the present technologies.
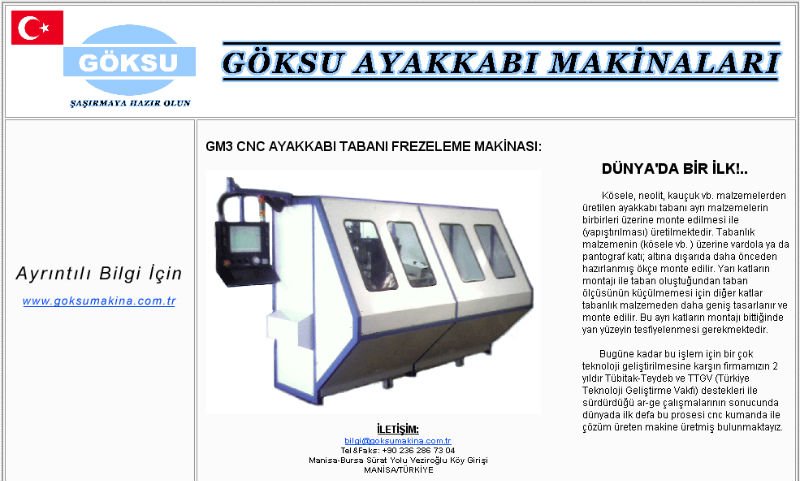
Packaging Detail:orginal sea wooden case |
Delivery Detail:1 month |