Furfural new technology, Furfural making machine and Furfural production line
Product Type:Chemical equipment | Place of Origin:Jiangsu China (Mainland) | Brand Name:Huiya | Model Number:HY-1009 |
After-sales Service Provided:Engineers available to service machinery overseas |
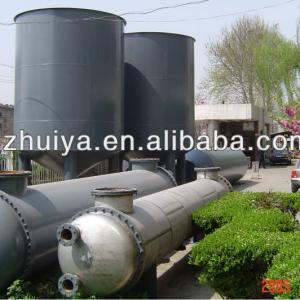
Introduction to a new technology of annual output of 5,000 tons of
furfural
- Technical Advancement
1,Producing a ton finished furfural consumes dry basis corn cob≤8t
2,Producing a ton finished furfural achieves 0 consumption of soda ash.
3,Product quality : In accordance with «Industrial furfural GB/T -20091926.1» country standard, we can customize high-grade furfural with content of 99.5% .
4, The amount of production workers in the operation of the entire production line on a single shift is 17, employing 51 workers on three shifts (the workers are 30% less than the plant of the same scale ).
5,Management of the three waste up to the standard:It achieves zero discharge of the wastewater from the production equipments via circulatory evaporation; the exhaust gas which comes from the process of the waste slag going through boiler combustion will be released up to the standard after the treatment of the desulfurization and dedust patented equipment.
- Advanced technology point:
1,Boiler water supply, wastewater evaporation water supply and the steam condensate adopt automatic control technology, so it can guarantee the stability of the primary steam and secondary wastewater steam and is conducive to the control of hydrolysis, thus ensuring the coarse aldehyde output of every single pot.
2,The slagless process of hydrolysis adopts pneumatic control valve. It is helpful to the control of hydrolysis, then it will decrease a slagless process operator for each class.
3,A steam condensing water reuse device is added to the wastewater evaporation process, it improved the thermal efficiency of the boiler; it can save 30% slag and increase the economic benefits of the by-products.
4,Rectification of the Coarse aldehyde adopts continuous distillation and high-boiling residues reevaporation process, it can guarantee the refined yield of Coarse aldehyde and the stability of the finished product’s quality, and reduce the overall cost of production.
5,The approach of burning slag in boiler uses automatic underground conveyor belt corridor to deliver the slag. Comparing with the furnace with the same scale, it can reduce 60% of the fireman; it not only reduces the pollution and loss of the secondary transfer process, but also ensure the stability of the cinder.
6,Boiler flue gas using domestic advanced desulfurization dust and removal smoke purifier, the removal efficiency has reached 98%, full compliance with national environmental requirements.
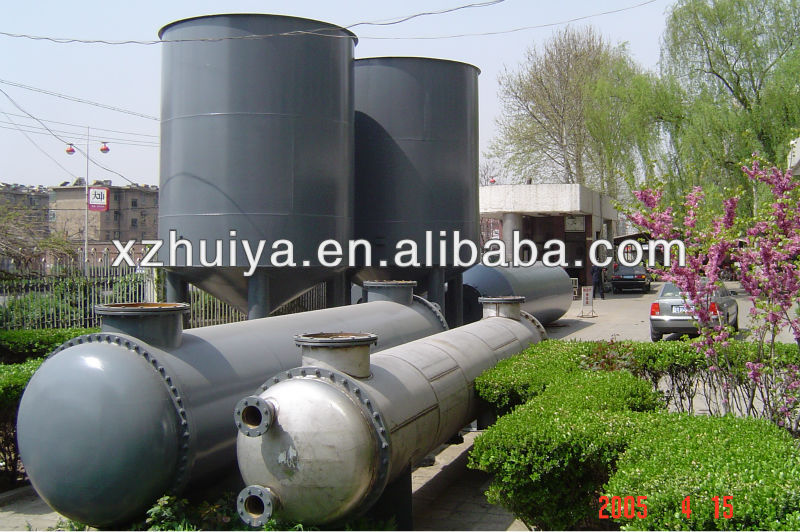
Packaging Detail:Seaworthy packing |
Delivery Detail:2 months after confirm order |