Full Automatic EPS sandwich panel production line
Place of Origin:Hebei China (Mainland) | Brand Name:Fada machinery | Model Number:EPS sandwich board machine line | After-sales Service Provided:Engineers available to service machinery overseas |
Using EPS or Rock wool Insulation board:Using EPS or Rock wool Insulation board | Power:AC 380V/50-60HZ | Total power:35KW | Total weight:16 tons |
Production line speed:0--5 m/min | Product thickness:30-250 mm | Annual output:600,000 square meters | Control System:Mitsubishi PLC touch screen |
Certification:CE & ISO9001:2008 | HScode:84552210 |
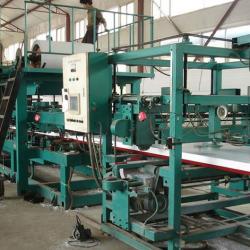
Full Automatic EPS sandwich panel production line
It is the most compact, easy and fast panel production line, using EPS(which is Expanded
Poly Styrene) blocks as an insulation.
Using light and block shaped insulation of EPS, it is possible to produce the panels with
maximum capacity.Having many experience of developing different sandwich panel
manufacturing line, we supply the reliable and easy machine to operate.
Having separate functional group of raw material-EPS and coil-insert, panel making and
dischage section, it is clear to control the line.
Raw material insert section is to insert EPS blocks and steel coil into the machine for
continuous production without failure.
Various roll forming machines shall be adopted to produce various profiles. Flying cutting
machine allows non-stop production with cutting tolerance of Maximum ±1mm in length.
Discharge section is to bring out the finished panel products outside for delivery. As light
insulation, it might be piled and packed manually.
Welcomed EPS sandwich panels
Alumium steel sandwich panels
Processing Sketch
EPS sandwich panels production lines
Panel Line Staging
COIL HOLDERS– Options for coil handling range from basic mandrel type systems to fully cantilevered driven
coil holders with coil cars.
JOINT ROLL FORMING– The Full Spec Line roll forming system is forming joints for wall, secret fix and roof
profiles in a compact side transfer unit. This full line roll-forming system is superior due to extra forming length
and all forming being done prior to any core introduction. Also available are very economical systems in the
Modular and Classic ranges as well as the heavy duty “Euroline”.
CORE LOADING– Options include a variety of cores such as EPS and Mineral Wool which is loading from
stacks of sheets or prepared lamellas. The special features include complete flexible setup ability with unique
core in-feed systems.
FAMWOLF– Incorporates a fully automatic Mineral Wool handling and preparation system for cutting, turning
and feeding Mineral Wool without the need for pre-cutting of Mineral Wool into lamellas.
CORE SANDING– we have a range of core preparation systems which include diamond coated roller-sanding,
planing and linishing.
CORE TRIMMING– Systems include TCT cutting as well as the new Multi Type cutting systems for ultimate in
speed and flexibility. The system utilises several cutting heads to ensure optimal cutting finishing especially on
Mineral Wool and composite cored panel systems.
GLUE APPLICATION– we offer a variety of solutions including wiping and spraying systems. The standalone glue
system allows interchanging the system to suit the needs of every production line. This system can even be made
interchangeable with an injection system for PUR and PIR foams.
LAMINATING PRESS– Various length Roller Presses are available for different line speed requirements or
Caterpillar Presses for ultimate laminating experience. The Caterpillar System can also be configured or
retrofitted to allow the production of injected foamed panels on a Laminating System.
PANEL CUTTING– A range of panel cutting systems including the proven Universal Bandsaw. Cutting
Systems can include overlap rebate saws for roof panels as well as several other options and combinations.
CONVEYORS– Several options are available for run out conveyors to take panels from the saw to further processing
including free rolling, motorised systems as well as reject tipping conveyors.
PANEL STACKING– The Panel Stacking Systems can be fitted with the latest designed Panel Flipper and
Conveyor Systems as required. The Panel Stacking System can be configured in various lengths and types
including options such as positioning systems, in-feed and exit conveyors, board and pallet loading systems
for below the stack to exit conveyor types, etc.
PANEL PACKAGE CONVEYORS– After stacking, panels are transported to other processing
EXTRACTION SYSTEM– we offer several types of extraction systems to suite each production line including standard
bag houses to full reverse pulse-jet systems as required for the correct Mineral Wool dust extraction.
PANEL WRAPPING– The Spiral Wrapper is an Automatic Wrapper which wraps the pack in stretch film. The
machine as standard includes automatic film cut off and starting, internal driven conveyor to assist in wrapping
shorter packs and gear set pre-stretching of the film. Various options include items such as automatic EPS leg
loading under panel stacks and automatic end film wrapping.
Other Options
Other options – available are: overlap removal system, overlap film insertion system, automatic leg insertion
under panel packs, core cutting with automatic coldwire or hotwire, reject panel transfer conveyors, board loading
and laminating systems, GFK/GRP laminating systems, side tape application, protective foil application. return to top
our standard profiles of sandwich panel.
Sale Mannger :Morre yin
Botou FaDa Numerical Control Goffer Tile MachineCo.,LTD
Fuzhuang Development Area of Botou City 104 Road,Hebei Province,China,062150
Mobile: +86 13091161261
URL:http://xinfada.en.alibaba.com
http://www.hbxfd.com/products.html
http://steelpipes.org/hbfadacom/ru/
" Save Paper, Save Earth, Print only if you Must! "
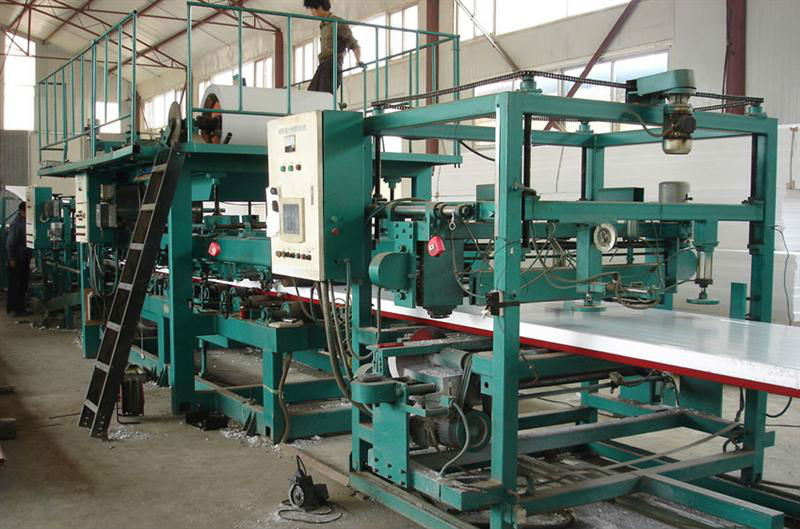
Packaging Detail:Standard export packing : 2*40 HP container ; main machine naked and fastened with iron wire in the container, rollers were painted with oil and packed with plastic film, electrics devices be packed with wooden box. |
Delivery Detail:within 45 working days after we recive your deposite |