Full-auto BGA repair RW-E6250
Place of Origin:Guangdong China (Mainland) | Brand Name:shuttle star | Model Number:RW-E6250 | Voltage:single-phase 220V |
Dimensions:L780*W850*H950mm | Weight:Approx. 150kgs | Usage:BGA repair | automation degree:full-auto |
certificate:ISO 9001:2000 CE |
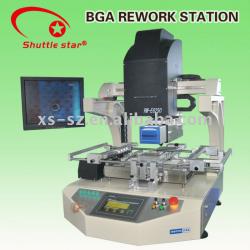
Full-auto BGA Repair RW-E6250
Specification
PCB dimension: W20×20~W450×W400mm
PCB thickness: 0.5~4mm
Applicable chip size: 1×1~70×70mm
PCB locating way: outer or jig
Working table adjustment: ±10mm forward/backward, ±10mm left/right
Temperature control: K-type thermocouple, close cycle controlled
Preheater: far infrared, 6000W
Top heater: hot air,1000W
Bottom heater: hot air, 1000W
Power supply: single-phase 220V, 50/60Hz, 6KW
Air supply: 5~8kgf/cm2,60L/min
Machine dimension: L850×W700×H950mm
Weight: Approx.150Kgs
--------------------------------------------------------------------------------------------------
Description
* Hot air head and mounting head are designed 2 in 1, and have both the auto soldering and
mounting function;
* Color optical system with functions of split vision, zoom - in and micro-
adjustment,equipped with aberration detection device; with auto focus and software
operation function,22X optical zoom; able to rework BGA sized up to 70mm×70mm;
* Touch screen interface, PLC control; able to display temperature curves and five detecting
curves at the same time;
* Color LCD monitor;
* Built-in vacuum pump; 360° rotation in Φ angle; mounting nozzle is micro-adjustable;
* 6 segments of temperature up (down) and 6 segments constant temperature control, 200
groups of temperature curve are stored; Curve analysis can be carried out on the touch
screen and has the communication function as computers ,with software attached;
* Able to arrive at three independent temperature zones,temperature and time can be
displayed digitally on the touch screen;able to rework CGA;
* The supports rack can be adjusted to restrain the local sinkage of the BGA soldering area;
* Suction nozzle can identify material and mounting height automatically, and can control the
air pressure within a small range;
* Both upper and lower hot-air heating head are movable on the IR preheating area to fit for
reworking BGA in different positions on PCB;
* Equipped with different alloy hot air nozzles, easy to replace and able to locate in any angle.
* Driven by the servo motor,the integrative hot air head can store 20 groups of different BGA
heating points and register marks.
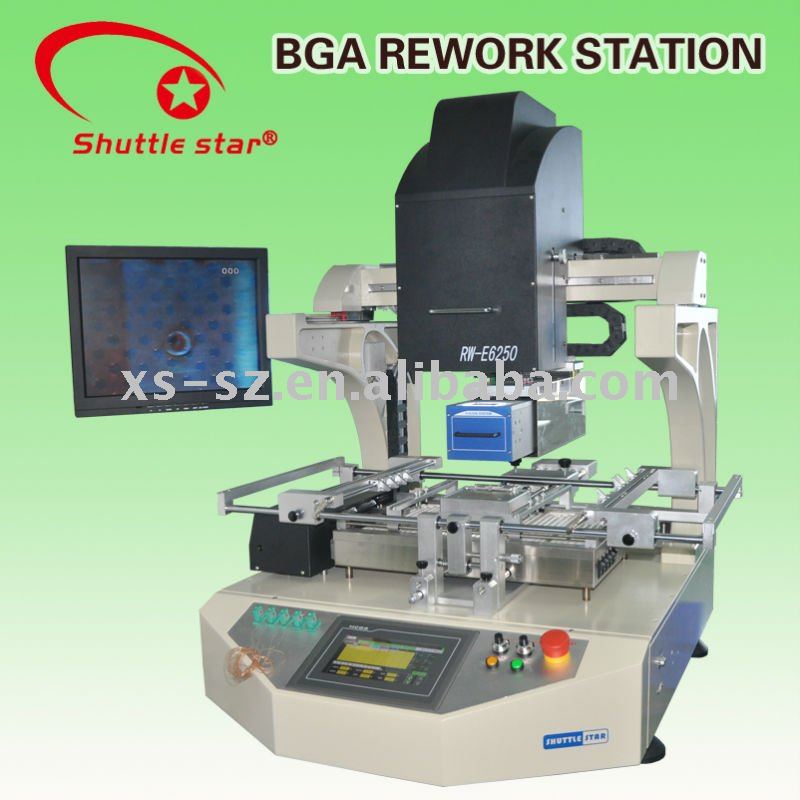
Packaging Detail:packed with standard plywood |
Delivery Detail:within 1 month after receipt of full payment |