freeze driers for AFGF BFGF EGF
Type:Freeze Drying Equipment | Place of Origin:China (Mainland) | Brand Name:JY | material:ss304 |
performance:good |
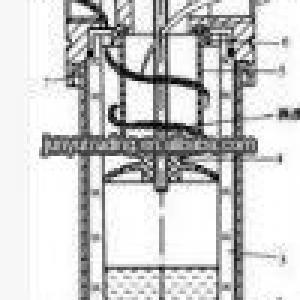
Principle of Freezing -Dryier
Freeze-drying,also known aslyophilisation,lyophilization,orcryodesiccation,is a dehydration process typically used to preserve a perishable material or make the material more convenient for transport. Freeze-drying works by freezing the material and then reducing the surrounding pressure to allow the frozen water in the material to sublimate directly from the solid phase to the gas phase
There are four stages in the complete drying process: pretreatment, freezing, primary drying, and secondary drying.
Pretreatment
Pretreatment includes any method of treating the product prior to freezing. This may include concentrating the product, formulation revision (i.e., addition of components to increase stability and/or improve processing), decreasing a high vapor pressure solvent or increasing the surface area. In many instances the decision to pretreat a product is based on theoretical knowledge of freeze-drying and its requirements, or is demanded by cycle time or product quality considerations. Methods of pretreatment include: Freeze concentration, Solution phase concentration, Formulation to Preserve Product Appearance, Formulation to Stabilize Reactive Products, Formulation to Increase the Surface Area, and Decreasing High Vapor Pressure Solvents.[1]
Freezing
In a lab, this is often done by placing the material in a freeze-drying flask and rotating the flask in a bath, called a shell freezer, which is cooled by mechanical refrigeration, dry ice and methanol, or liquid nitrogen. On a larger scale, freezing is usually done using a freeze-drying machine. In this step, it is important to cool the material below its triple point, the lowest temperature at which the solid and liquid phases of the material can coexist. This ensures that sublimation rather than melting will occur in the following steps. Larger crystals are easier to freeze-dry. To produce larger crystals, the product should be frozen slowly or can be cycled up and down in temperature. This cycling process is called annealing. However, in the case of food, or objects with formerly-living cells, large ice crystals will break the cell walls (a problem discovered, and solved, by Clarence Birdseye), resulting in the destruction of more cells, which can result in increasingly poor texture and nutritive content. In this case, the freezing is done rapidly, in order to lower the material to below its eutectic point quickly, thus avoiding the formation of ice crystals. Usually, the freezing temperatures are between−50 °C and−80 °C. The freezing phase is the most critical in the whole freeze-drying process, because the product can be spoiled if badly done.
Amorphous materials do not have a eutectic point, but they do have a critical point, below which the product must be maintained to prevent melt-back or collapse during primary and secondary drying.
Primary drying
During the primary drying phase, the pressure is lowered (to the range of a few millibars), and enough heat is supplied to the material for the water to sublime. The amount of heat necessary can be calculated using the sublimating molecules’ latent heat of sublimation. In this initial drying phase, about 95% of the water in the material is sublimated. This phase may be slow (can be several days in the industry), because, if too much heat is added, the material’s structure could be altered.
In this phase, pressure is controlled through the application of partial vacuum. The vacuum speeds up the sublimation, making it useful as a deliberate drying process. Furthermore, a cold condenser chamber and/or condenser plates provide a surface(s) for the water vapour to re-solidify on. This condenser plays no role in keeping the material frozen; rather, it prevents water vapor from reaching the vacuum pump, which could degrade the pump's performance. Condenser temperatures are typically below−50 °C (−60 °F).
It is important to note that, in this range of pressure, the heat is brought mainly by conduction or radiation; the convection effect is negligible, due to the low air density.
Secondary drying
The secondary drying phase aims to remove unfrozen water molecules, since the ice was removed in the primary drying phase. This part of the freeze-drying process is governed by the material’s adsorption isotherms. In this phase, the temperature is raised higher than in the primary drying phase, and can even be above 0 °C, to break any physico-chemical interactions that have formed between the water molecules and the frozen material. Usually the pressure is also lowered in this stage to encourage desorption (typically in the range of microbars, or fractions of a pascal). However, there are products that benefit from increased pressure as well.
After the freeze-drying process is complete, the vacuum is usually broken with an inert gas, such as nitrogen, before the material is sealed.
At the end of the operation, the final residual water content in the product is extremely low, around 1% to 4%.
Freeze-drying equipment
Unloading trays of freeze-dried material from a small cabinet-type freeze-dryer
Product viewable single shelf freeze-dryer
Production freeze-drier
Development freeze-dryer
There are essentially three categories of freeze-dryers: the manifold freeze-dryer, the rotary freeze-dryer and the tray style freeze-dryer. Two components are common to all types of freeze-dryers: a vacuum pump to reduce the ambient gas pressure in a vessel containing the substance to be dried and a condenser to remove the moisture by condensation on a surface cooled to−40 to−80 °C(−40 to−112 °F). The manifold, rotary and tray type freeze-dryers differ in the method by which the dried substance is interfaced with a condenser. In manifold freeze-dryers a short usually circular tube is used to connect multiple containers with the dried product to a condenser. The rotary and tray freeze-dryers have a single large reservoir for the dried substance.
Rotary freeze-dryers are usually used for drying pellets, cubes and other pourable substances. The rotary dryers have a cylindrical reservoir that is rotated during drying to achieve a more uniform drying throughout the substance. Tray style freeze-dryers usually have rectangular reservoir with shelves on which products, such as pharmaceutical solutions and tissue extracts, can be placed in trays, vials and other containers.
Manifold freeze-dryers are usually used in a laboratory setting when drying liquid substances in small containers and when the product will be used in a short period of time. A manifold dryer will dry the product to less than 5% moisture content. Without heat, only primary drying (removal of the unbound water) can be achieved. A heater must be added for secondary drying, which will remove the bound water and will produce a lower moisture content.
Tray style freeze-dryers are typically larger than the manifold dryers and are more sophisticated. Tray style freeze-dryers are used to dry a variety of materials. A tray freeze-dryer is used to produce the driest product for long-term storage. A tray freeze-dryer allows the product to be frozen in place and performs both primary (unbound water removal) and secondary (bound water removal) freeze-drying, thus producing the dryest possible end-product. Tray freeze-dryers can dry products in bulk or in vials or other containers. When drying in vials, the freeze-drier is supplied with a stoppering mechanism that allows a stopper to be pressed into place, sealing the vial before it is exposed to the atmosphere. This is used for long-term storage, such as vaccines.
Improved freeze drying techniques are being developed to extend the range of products that can be freeze dried, to improve the quality of the product, and to produce the product faster with less labor
Spray dryingis a method of producing a dry powder from a liquid or slurry by rapidly drying with a hot gas. This is the preferred method of drying of many thermally-sensitive materials such as foods and pharmaceuticals. A consistent particle size distribution is a reason for spray drying some industrial products such as catalysts. Air is the heated drying medium; however, if the liquid is a flammable solvent such as ethanol or the product is oxygen-sensitive then nitrogen is used.
All spray dryers use some type of atomizer or spray nozzle to disperse the liquid or slurry into a controlled drop size spray. The most common of these are rotary disks and single-fluid high pressure swirl nozzles. Alternatively, for some applications two-fluid or ultrasonic nozzles are used. Depending on the process needs, drop sizes from 10 to 500 µm can be achieved with the appropriate choices. The most common applications are in the 100 to 200 µm diameter range. The dry powder is often free-flowing.[2]
The most common spray dryers are called single effect as there is only one drying air on the top of the drying chamber (see n°4 on the scheme). In most cases the air is blown in co-current of the sprayed liquid. The powders obtained with such type of dryers are fine with a lot of dusts and a poor flowability. In order to reduce the dusts and increase the flowability of the powders, there is since over 20 years a new generation of spray dryers called multiple effect spray dryers. Instead of drying the liquid in one stage, the drying is done through two steps: one at the top (as per single effect) and one or an integrated static bed at the bottom of the chamber. The integration of this fluidized bed allows, by fluidizing the powder inside a humid atmosphere, to agglomerate the fine particles and to obtain granules having commonly a medium particle size within a range of 100 to 300 µm. Because of this large particle size, these powders are free-flowing.
The fines generated by the first stage drying can be recycled in continuous flow either at the top of the chamber (around the sprayed liquid) or at the bottom inside the integrated fluidized bed. The drying of the powder can be finalized on an external vibrating fluidized bed.
The hot drying gas can be passed as a co-current or counter-current flow to the atomiser direction. The co-current flow enables the particles to have a lower residence time within the system and the particle separator (typically a cyclone device) operates more efficiently. The counter-current flow method enables a greater residence time of the particles in the chamber and usually is paired with a fluidized bed system.
A spray dryer is a device used in spray drying. It takes a liquid stream and separates the solute or suspension as a solid and the solvent into a vapor. The solid is usually collected in a drum or cyclone. The liquid input stream is sprayed through a nozzle into a hot vapor stream and vaporised. Solids form as moisture quickly leaves the droplets. A nozzle is usually used to make the droplets as small as possible, maximising heat transfer and the rate of water vaporisation. Droplet sizes can range from 20 to 180 μm
depending on the nozzle.[2]There are two main types of nozzles: high pressure single fluid nozzle (50 to 300 bars) and two-fluid nozzles: one fluid is the liquid to dry and the second is compressed gas (generally air at 1 to 7 bars).
Spray dryers can dry a product very quickly compared to other methods of drying. They also turn a solution, or slurry into a dried powder in a single step, which can be advantageous for profit maximization and process simplification
performance | efficience | perfomance | |
good | high | great |
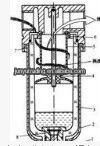
Packaging Detail:wooden package |
Delivery Detail:asap |