FLUID BED DRYER
Type:Fluid Bed Drying Equipment | Place of Origin:Maharashtra India | Brand Name:RIDDHI | Model Number:RDFBD |
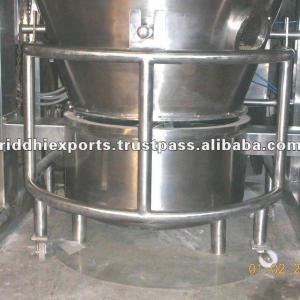
FLUID BED DRYER
Fluid Bed Dryer – 60/120/200/250/300/500 Kgs
'RIDDHI' - introduces one of the finest "FLUID BED DRYER" unit providing compactness and conceptional principle of Air Fluidization for drying granules, crystalline, coarse or similar materials in Pharmaceuticals, Fine Chemicals, Dyes, Food & Allied Industries.
The basic concept of the Fluid Bed System begins with a simple Drying unit to which several different optional packages may be added for conversion to a granulation or coater.
Process control system ranges from standard pneumatic logic to sophisticated computerized controls. Air handling equipments can vary from the basic compact pre-filter and heater to the system, which provides complete control of the condition of the processing air. This higher technology of process involved many modern technologies and to match that RIDDHI introducing conventional Fluid Bed Dryer.
Advantages :
The conventional drying method for drying products in tray dryers is rather inadequate & troublesome. They also occupy large space & have very high & uneven drying times and also involved high labour input. To over come this problem RIDDHI made Fluid Bed Dryer which is the simple solution to dry the products.
Suitabilities :
This compact unit is suitable for drying granular, crystalline, coarse or similar materials in Pharmaceuticals, Dryer, Fine Chemicals & Food & Allied Industries. It is also possible to dry fine crystal or coarse materials in fluid bed dryers.
DESCRIPTION :
Latest improvement in design makes this unit truly GMP model for Pharmaceuticals industries & versatile in operation for other industries like food, dyestuff, chemicals & polymer industry. In GMP models, all the contact parts made out of S.S.304 / 316 material & are provided with isolated panel board. However with standard Fluid Bed Dryers for product containers, retarding chamber are made out of stainless steel materials S.S. 304 only & other parts from mild steel sheet.
BATCH SIZE
Batch size indicates weights of wet products (inclusive of moisture). Our Model RDFD-30 can take batch size of 30 to 40 Kgs. of wet material. Similarly model RDFD-120 can process 120 to 135 Kgs. of wet material per batch. The weight of materials to be loaded per batch depends upon the bulk density of wet material.
OPERATION :
The wet material is introduced into the dryer as a batch of material in a product container which is provided with air distributor plate & clutch weave. Induced draught is created by the blower & fresh air is sucked into the unit. After filteration, clean air passes through the heating elements. This hot air then passes through the product containers, creating turbulance in the products & hence the product moves up and down known as Fluidization in the product container. Due to this process, the heat transfer is quick and the product is dried fast without appreciable loss of heat. Filter bags prevent particles escaping from the dryer.
HEATING:
Fluid Bed Dryer can be supplied in electric heating, steam heating or hot water circulation systems or gas heating system on demand. Electrically heated dryers are provided with electrical heating elements and are suitable to raise air temperatures by about 750 C (i.e from 300 C to 750 C). Similarly steam operated dryers are provided with steam radiator suitable to raise air temperature about 600 C to 750 C depending upon pressure of steam. Generally dryers bigger than RDFD- 60 are incorporated with steam heating system as it is more economical.
DRYING TIME :
The drying time depends upon various factors such as physical properties of material, moisture content, type of moisture (free moisture or water of crystallization), drying temperature etc. The crystalline products can be dried faster than amorphous product containing same percentage of moisture at the same temperature. Generally pharmaceutical granules or crystals containing free moisture of about 20% to 25% can be easily dried in about 30 to 40 minutes at a temperature of about 750C. Certain crystalline materials containing about 40% of moisture can be dried in Fluid Bed Dryer within 35 to 45 minutes.
IMPORTANT :
In case the product contains solvents or inflammable substances, it is essential that the Dryer is steam operated &provided with flame proof motor.
MOTOR :
The dryer will be provided with with suitable Remi/Hindustan/Sabar or standard ISI make motor of 2800 RPM
FILTERATION:
Single stage filteration of 20 microns PP cloth filter, P.P. filter bag for exhaust air, also multi stage filteration can be given on demand. Positive Earthing Arrangement, explosion flap are given as a part of standard features.
Control Panel:
Pre-wired control panel indicate Digital Timer, Digital Temperature Indicator cum controller(Inlet), Digital Temp. Indicator (Outlet), Sensor, Star-Delta Starter with relay, Indicating Lamps, MCBs, Amp. Meter cum Volt Meter, Selector switch etc.
Special features :
- Uniformity in drying and reduction in drying time.
- Atmospheric inlet air is filtered by means of single / multi stage filters of 20 microns to prevent any fine dust to pass through the product.
- Steam Coil made out of 1" dia. SS 304/316 finned tube & is designed to get pressure of around 3-4kg./cm^2 (working pressure 3 kg/cm^2).
- Digital temperature indicators cum controller is provided with the unit to indicate the inlet and outlet air temperature as well as to controller the present inlet air temperature.
- Air suction and discharge dampers provided to control the inlet and outlet air flow.
- An explosion safety flap of adequate capacity at the rear end of the dryer and an positive earthing point to prevent static charge in the machine are provided.
- Timer provided to set the process time which will cut off the motor supply after pre-set time period.
You will have to provide following :
- Level floor at site.
- Required electrical connection up to the machine through suitable isolating switch.
- Compressor with FRL to supply pure air to the Pneumatic components.
- Electrician at the time of Installation.
- Ducting from exhaust to the wall with fittings.
- Proper floor pan to be given at the time of ordering the machine.
- Steam boiler and all the connections, fittings and pipe, with controllers and pressure gauges to be connected to the radiator by party.
- 3 phase power supply upto the control panel of the machine.
- Inlet steam & outlet steam line with pressure gauge safety valve, by pass, On & Off Gate Valve provision to be made, electrical operated steam control valve 1 inch or ¾ inch BSP to be given.
- 4 sq.mm 6 core wire from panel Board to main motor.
- 1.5 sq. mm 2 core wire from panel Board to Pneumatic section.
- 0.5 mm 3 core wire from Panel Board to inlet & out let sensor.
Technical Specification
Model | 5 | 30 | 60 | 120* | 200* | 250* | |||
Product Bowl Volume in Liters | 20 | 100 | 220 | 440 | 780 | 960 | |||
Bacth Capacity In Kg | 5 . | 30 | 60 | 120 | 200 | 250 | |||
Heating capacity in KW | 6 | 18 | 36 | 60 | - | - | |||
Steam Consumption Kgs/hr | 14 | 25 | 50 | 100 | 160 | 200 | |||
Drying temperature in 0 C | 50-80 | 50-80 | 50-80 | 50-80 | 50-80 | 50-80 | |||
Blower Motor (HP) | 1.5 | 5 | 10 | 15 | 20 | 25 | |||
Electricals | 2800 rpm / 3 Phase / A.C. |
* Steam heated Model is advised.

Packaging Detail:SEA WORTHY PACKING |
Delivery Detail:4-6 WEEKS |