Electrohporesis coating line for car assembly line
Type:Coating Production Line | Substrate:metal | Coating:Powder Coating | Place of Origin:China (Mainland) |
Brand Name:Fengjing | Model Number:Fengjing-Electrophoresis6 |
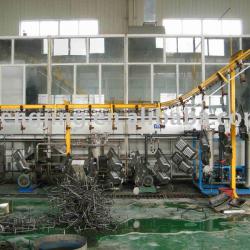
Electrophoretic coating or painting is an immersion process, also known as E-Coating, Electropainting or simply EP.
These terms describe the electrically induced transfer of a non conductive organic coating, from a thin, low solids dispersion in water, onto a conductive surface.
Supplied as high solids concentrates, LVH EP coatings are dilutes with de-mineralised water and contained in a process tank for use.
Coatings may be water white clear, coloured clear or opaque.
Electrophoretic coatings fall into two main categories - anodic or cathodic. Anodic materials coat the positive electrode (the anode) and cathodic materials coat the negative electrode (the cathode).
Connected to either a positive or negative power supply, as appropriate, the work is immersed in the process tank for coating. The process tank also contains electrodes of opposite polarity while a rectifier provides the (DC) power supply.
Although most modern EP coatings are cathodic, there are materials that benefit from the use of anodic coatings, aluminium is a good example.
--------------------------------------------------------------------------------
The electophoretic coating process comprises four stages or operations, as follows:-
1. Cleaning and pre-treatment. Where the work is prepared for coating
2. Application. The coating stage that takes place in the process tank, as already described.
When work is removed from the process tank it has a firm, insoluble, paint or coating of consistent film thickness all over it, including on sharp edges and in awkward recesses. It is also wet with a dip coat of dilute, low solids, material from the coating tank.
3. Rinsing. This removes the dip coat with a material known as permeate or ultra-filtrate. This is a mainly aqueous extract taken from the dilute coating in the process tank. After rinsing, the permeate plus dip coat, is returned to the process tank to minimise losses.
The permeate is also purified by a special ion exchange unit to eliminate contaminants which may build-up in the process tank. The combined ultra-filtration and ion exchange process is known as the TRAP (Total Reclaim And Purification) system.
The final rinse is carried out with de-mineralised water plus a rinse-aid additive.
4. Oven curing (stoving). This follows the final rinse. This helps the film to 'flow-out' and become smooth. Its main function however is to initiate chemical reactions (the curing process) in the applied film, to make it hard and resistant to solvents and chemicals.
The above stages in the electrophoretic coating process may vary to some degree for certain products, please ask for further information.
--------------------------------------------------------------------------------
The electrophoretic surface coating process provides the user with the following economical, technical and environmental benefits:-
* Easily automated plant - low labour costs.
* No wastage - almost 100% transfer efficiency.
* Consistent, controllable film thickness, even on sharp edges and in awkward recesses.
* Smooth films - no runs or sags.
* Water based process - only small amount of low volatility solvent required.
* Low toxicity.
* Minimal effluent.
* Low temperature/time stoving schedules.
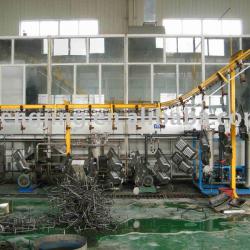
Packaging Detail:1set/pack |
Delivery Detail:Within 2 month after 30% deposit received |