Dia. 508~3048mm Spiral Welded Pipe Mill
Type:Pipe Production Line | Pipe Material:Q235, Q345, A25, A, B, X42-X80 | Application:Water Supply and Drainage, piling pipe, API Line Pipe, Oil and Gas | Place of Origin:Shanxi China (Mainland) |
Brand Name:TMM | Model Number:Dia. 508~3048mm Spiral Welded Pipe Mill |
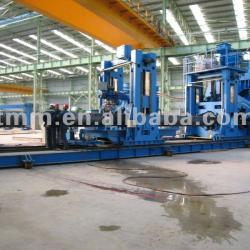
Turnkey Associate
TMM is fully geared up to associate with you for setting up Pipe Manufacturing & Pipe coating Plants from the Green Field Stage.
Design & Engineering
TMM has a fully-equipped and adequately manned in-house Project Engineering Department having famous Technical engineers in the field of welded pipe industrial.
Easy & Early installation & commissioning
With TMM's rich experience in Spiral Pipe Manufacturing, TMM can install and commission the plants with equipments and machines earlier than others.
TMM’s experienced backup support will bring customers’ plants in commercial production fastest.
Training support
TMM can also provide on the job practical training to Customers’ Engineers/Operators on a fully operational plant in one of TMM’S running factories
Unique Advantage
TMM is not only a Designer & Manufacturer of Pipe manufacturing plants, but also has the unique capability of Commissioning and demonstrating assured production quantity; drawing operational expertise from its own running plants.
High-SAW PIPE MANUFACTURING
Large diameter API / IS Grade pipes with a diameter ranges from 406 mm to 3175 mm, wall thickness upto 25 mm, length upto 20 meter and upto and including API 5L X – 80 are manufactured at Varsana H-Saw pipe mills. Annual mill capacity is around 100000 MT per mill.
The making of Spiral Weld pipes :
Hot rolled Coil strip is mounted into the straightening machine. The strip is positioned to the correct helix angle. Before passing the strip through, the leading and trailing ends of the incoming and already inserted coil strip respectively are welded together. The edges are then machined simultaneously on both sides by an edge miller. In the forming section, a 3-roller bending device bend the strip helically into a cylindrical pipe. Then the longitudinal edges of the incoming strip are brought into low point contact and the resulting butt joint is continuously welded externally after a half-turn of the pipe. Finally, it is cut off to the desired length with a plasma torch.
The duly welded pipe is discharged from the Spiral mill for processing of the pipe ends
End beveling station. |
Hydro-testing station for testing of each pipe. |
U.T. / Ultrasonic testing station for NDT weld flaw detection. |
End X-ray / continuous radiography. |
Finishing station and final inspection station. |
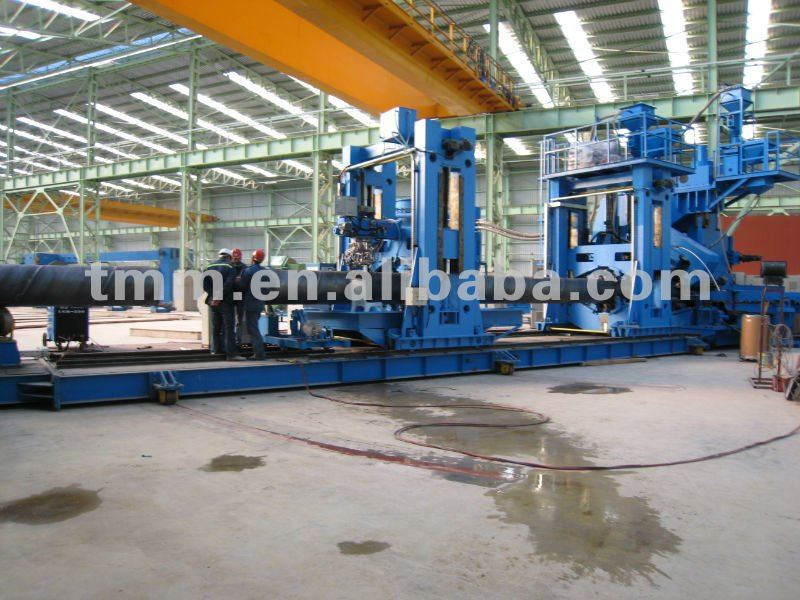
Packaging Detail:Waterproof Package for bulk shipping, Plywood Case and 40' Containers |
Delivery Detail:5-8 Months for completed mill line |