DCD100 sand mill machine in nano level, bead mill
Condition:New | Type:bead mill | Product Type:Paint | Place of Origin:Jiangsu China (Mainland) |
Brand Name:TongHui | Model Number:DCD | Voltage:220/380/415 | Power(W):22000-30000 |
Certification:CE | Warranty:1-5 year | After-sales Service Provided:Engineers available to service machinery overseas | Tank capacity(L):1.2L-79L |
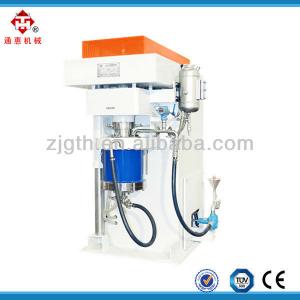
Technical Parameters:
Product Configuration:
· Machine wetted parts made of hardened stainless steel and Tungsten Carbide;
· Variable Speed Drives of Agitator and Product Slurry Feed Pump through Variable Frequency Drives (VFD);
. Unit in EXPLOSION PROOF design
· Double acting mechanical seal with cooling coils for the circulation of cooling water;
·Hydraulic lift for grinding vessel;
· Pressure transducer in the product feed line providing an analog output signal;
· Product discharge temperature probe at the end of the discharge pipe;
· OMRON programmable logic controller (PLC) and software license for PLC;
Advantage:
DCD High Flow Bead Mill has a wide range of applications.
The excellent quality of bright-colored and high-resolution fashion mobile phones, TFT screens or laptops, and a large quantity of fashion automotive paint and bright-colored paint really show the outstanding dispersion characteristic of the model. It is more used the fields of paints and varnishes, agricultural chemicals, inks, chemicals, paper making and nanotechnology.
· High-quality color filter of TFT screen and PLC display screen;
· More glorious car paint, high solids and water-based products;
· Heavy coatings with higher resistance;
· Nano-level grinding of photosensitive pigment makes it more brilliant, eyecatching;
· In the production of high-quality dyeing paint, the enhanced color strength can lead to more economic benefits;
· High-quality packaging and silver² ink with more gloss and transparency;
· Super inkjet products with higher quality;
· Obtaining higher quality and¾ economic benefits in research and production, with high requirements of product development in percentage and grinding.
DCD Milling Media Size:
Quick and easy operation:
The model is simple, easy to master, and all the maintenance can be completed quickly and easily.
·It is very easy to add grinding media from the filling hole above;
·Do not discharge and grind the media, but the protective screen can be taken out of the closed mill;
·Minimal cleaning fluid is required for replacement of the product;
·Minimum time and cleaning are required for replacement of grinding media;
·It is very simple to make the grinding chamber decline by an integral lifting device;
·The grinding chamber can drop and rotate along the pivot.
Good cooling performance:
·Products are pre-cooled in the eddy current guidance gap;
·The effective stator and rotor of the grinding chamber are cooled on the outer layer;
·Products are effectively cooled in the return zone at the bottom of the stator;
·Within grinding chamber of product flow, the effective stator and rotor are cooled;
·The continuous eddy current of the product on the inner surface of the rotor cools the inner grinding chamber down strongly.
Working principle:
The products to be ground go into the feed pump from the top, and are evenly spread on the upper part of the outer rotor with the balanced rotating rotor. The products are thoroughly pre-treated within the centrifuge area of the rotor and the cylindrical gap formed by the stator. In the next strong grinding belt, the interaction between the rotor and stator nails has a strong continuous changing impact on the grinding media, and the grinding media then acts on the products. In the bottom area of the stator, a mixture of the products and grinding media return and enter to the grinding chamber, and flows from the bottom to the top. Here, the grinding media is only affected on the surface of the stator nail and rotor.
The strenuous exercise of small grinding media can achieve truly effective grinding and dispersion of products, and according to actual situations, it can achieve sub-micron or nanometer range; the products stay in the grinding machine for a particularly short time with a certain flow rate through the outer layer and next ring inner grinding chamber, resulting in a very narrow distribution belt of product granules.
Separation of grinding media:
The grinding media at the upper part of the grinding chamber is accelerated to the maximum peripheral speed through a guide plate. Thanks to a different density the grinding media is separated by centrifugal force and returns to the cylindrical vortex guide gap through the open slot in the rotor. As a new product flows into the grinding machine, the separated grinding media is once again sent to the rotor/stator's outer grinding zone. Thus, the grinding media is formed through an internal closed ring of the inner and outer grinding chamber.
Discharge:
Under the pressure of the feed pump, the products separated by the grinding media by means of centrifugation flow along the opposite direction of the centrifugal force, and then are discharged through the cylindrical protective screen set in the middle and the next discharge tube. It is very easy to take them down through the discharge tube and protective screen assembled by screw.
Package ( for your reference ):
Our certification
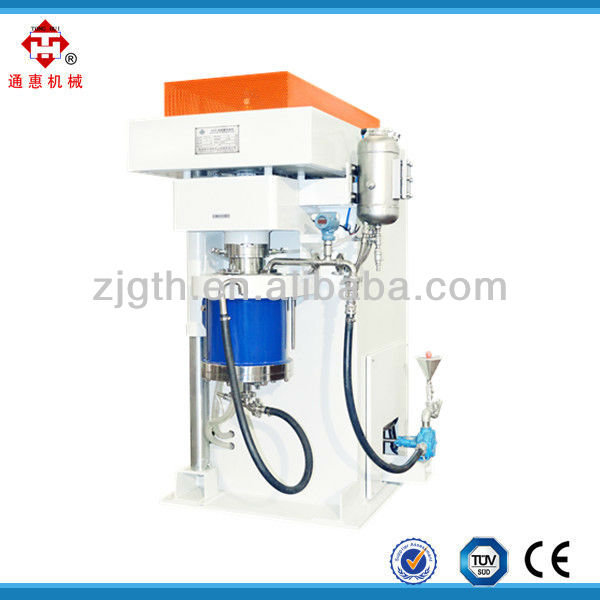
Packaging Detail:International package; standard package. |
Delivery Detail:30 working days |