DBC-10 Carbon Mixer
Processing:Mixer | Place of Origin:Jiangsu China (Mainland) | Brand Name:Sunswell | Model Number:DBC-10 |
Processing Types:Carbonated Beverage | carbon mixer:mixer | carbonated soft drinks mixer:carbonated soft drink mixing machine | carbonated drinks mixer:carbonated drinks mixing machine |
csd mixer:csd mixing machine | csd carbon mixer:csd carbon mixing machine | cola mixer:cola mixing machine | carbonated mixer:carbonated mixing machine |
soda mixer:soda mixing machine | gas mixer:gas mixing machine | CO2 mixer:CO2 mixing machine |
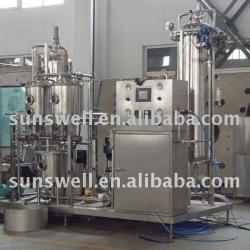
DBC-10 Carbon Mixer
Technical parameter
1) Mixing capacity: 10t/hr
2) Temperature: 0-4°C
3) Sugar content: technical standard
4) CO2content: 8-9g/l
Description of equipment
Providing deaeration, mass flow blending of syrup and water, bi-carbonation. All pressure vessels are designed, fabricated and tested according to applicable provisions of the ISPESL Code (standard). The principal componentss are:
1) One Deaeration system to remove air down to low levels (1ppm of residual oxygen) for stable foam-free filling. The system consists of a single stainless steel de-aeration tank by vacuum pump into which water is sprayed as fine mist in a CO2atmosphere.
2) One Proportioner to provide fully automated control of a two stream water/syrup blending. The flow-rate control is recipe based. The system includes the following quality components:
3) Syrup tank equipped with level control system, and a flow meter for syrup quality, to ensure rigour mix, which can be repeatedly operated.
4) Two control-valves for adjustment of flow volume of syrup from the tested result.
5) Two Centrifugal Blend Pumps and one Straight-line Carbonation Injection Control System to maintain +/-0.02 volumes/volume carbonation control. This range is maintained by measuring the CO2 flow in the CO2 Mass Flow Meter and controlling it, through a modulation valve, at a rate proportional to product flow.
6) One Buffer Tank with Capacitance Level Control to control system flow-rate according to the recipe as reflected by the finished product level in tank. Capacitance Level Probe System provides continuous level indication to PLC to enable fine-tuning and adjustment of flow-rate from the Blender. Finished product is discharged to the Filler.
7) One Control Package to provide automatic system for precision process blend control. Package includes suitable PLC, control program, video graphic operator interface with informational and control screens, and all necessary process sensors and safety protection devices. System software includes system schematics, recipe manager, production displays, trending, alarm screens with complete security password protection.
8) One Control Panel, fabricated in stainless steel with PLC; electrical switches; electrical relays; and controls for Flow-meter Systems. A colour touchscreen operator interface is mounted on the face of the panel. The panel door is equipped with a safety electrical disconnect latch and the door is gasketed.
9) One Pneumatic plant including: all air valves, air switches, and air tubing, and one Tubular Stainless Steel Base on which the majority of the components
are mounted. The base is of welded construction and includes adjustable stainless steel legs, with high density polyethilene mounting pads.
Main features:
1) Advanced mass flow in-line blending and carbonation for reduced product & ingredient losses;
2) High efficiency deaeration
3) Simplified, user-friendly, operator interface
4) Automated “ no-dump” start-up capability
5) Complete product recipe management
6) Ingredient usage trending and totalling
7) Improved product yields and consistency
8) Reduced B.O.D. cost
9) Fast, favourable return-on-investment
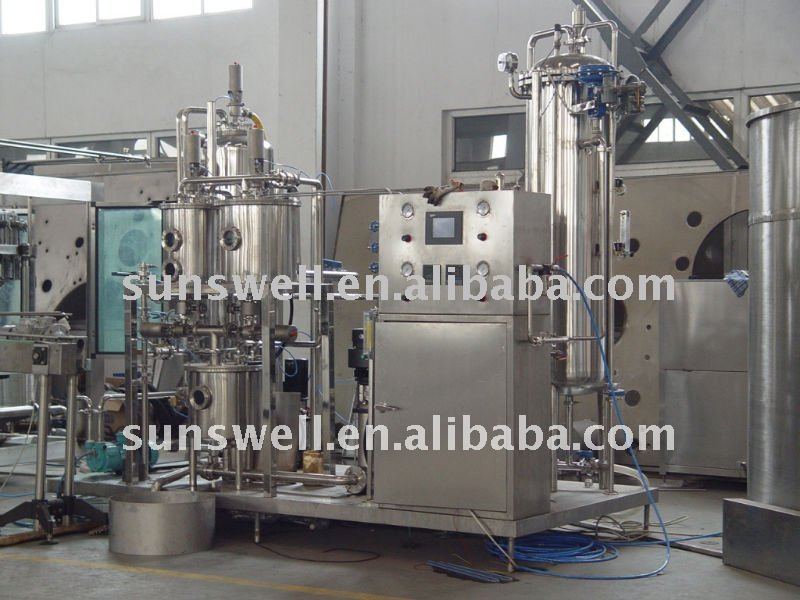
Packaging Detail:Seaworthy wooden cases |
Delivery Detail:20-80 days |