Cross Flow Membrane Filtration
Processing:Filter,Full Automatic | Condition:New | Place of Origin:Italy | Brand Name:FRAMAX |
Model Number:FILTER CROSSFLOW 092-06 W | Processing Types:Alcohol | Voltage:380 V - 50 Hz | Power(W):7500 W |
Weight:750 Kg | Dimension(L*W*H):cm 190x150x170 h | Certification:European CE | Warranty:12 months |
After-sales Service Provided:Engineers available to service machinery overseas |
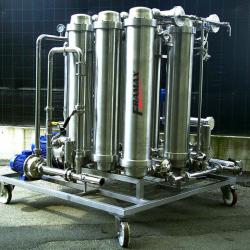
FRAMAX CROSS-FLOW FILTER
Model : 092-06 W
Material : S.S. AISI 304
Use of cross-flow filter
- to obtain very clear liquids (turbidity < 1 NTU)
- to produce sterile liquids (through Nano-Micro membrane filtration)
- to prevent bacterial contaminations
- to block anomalous fermentations
- to let stand out aromas and perfumes in purity
- to clarify just in one step
- to reduce and/or avoid clarifying agents
- to eliminate the use of DE and its waste disposal
- to improve and making faster the tartaric stability
- to prolong the life of the pre-bottling cartridges
Characteristics of cross-flow filter
- 20 hours and more of filtrating cycles
- self-governing filtration and automatic shut down
- rinsing and C.I.P. step with no water requirements
- regular permeate flow and safe filtration
- no more down times
- lower pollution
- no product losses (yield to 99.8%)
- energy saving
Crossflow filter with organic membranes of 0,65 micron absolute pore size, to achieve impressive super filtration. Crossflow filtration makes a perfectly clear wine without any clarifying agent and/or filter aid requirement.
When a clarifying treatment with bentonite is required, it is necessary to provide the complete separation of bentonite (by decantation or centrifuge) from wine before starting filtration.
Filtration rates and cycles of filtration are depending of solid’s content and kind of products such as colloids, bacteria, yeasts.
Supporting Skid
S.S. AISI 304 supporting skid on wheels, complete with connections for filtering modules, pumps, control board.
Feeding section
Double S.S. AISI 304 pre-filter, apt to retain coarse particles complete with pleated S/S cartridge.
Feeding inlet collecting pipe, complete with butterfly valves, DIN 11851 fittings.
Feeding centrifugal pump, S.S. AISI 304 made.
Loop section
Filtering modules with S.S. housings and with organic membranes of 0,65 micron absolute pore size.
Vertical and parallel assembling.
Loop pipelines for filtering modules collection (retentive side), S.S. AISI 304 made, completed with flanges and DIN 11851 fittings.
Concentrate outlet pipe, complete with pressure-tuning valve, S.S. AISI 304 made.
Section butterfly valves with DIN 11851 fittings.
Drain pipe and S.S. ball valves.
Safety pressure switch device and working pressure gauges.
Recirculation centrifugal pumps, S.S. AISI 316 made.
Filtrate liquid outlets.
Filtrate outlet collecting pipes (delivery and discharge) complete of butterfly valves, DIN 11851 fittings.
Filtrate rates regulation valve.
Filtrate flow-meter with observatory glass.
Drain pipe with ball valve.
Filtrate Sample cock tap.
Pressure gauge device.
Back-wash unit
Automatic Back flushing System working during the filtration cycle, operated by a counter current pumping device. It provides longer filtration cycles by controlling the membrane flow decline.
Completed with by-pass butterfly valve.
Cleaning section
Double water pre-filter, disposable PP cartridge, complete with pressure gauge and ball valve.
Service buffer tank for the cleaning step, made in s/s, on wheels, with accessories.
Pneumatic section
Reduction/regulator pressure device complete with safety filter and electro-valve.
Reduction/regulator pressure device complete with safety filter, section cocks for plant emptying.
Control board
Electric control board, made in S.S. under USA rules. Function’s control on:
recirculation pumps , feeding pump, actuated valve, electrical devices.
It also include the back-flushing system setting.
Set of control instrumentation consisting of thermometer/thermostatic device with alarm set point.
Safety plant turning-off to avoid damages.
Finishing
Internal surface : 2B, polished
External surface : pipes & accessories, mirror polished or 2B
Welding
ARGON/TIG execution with gas saturation (welding as per food requirements)
Technical data
Model : 092-06 W (92 sqm of nano/micro membrane)
Adsorbed power : 7.5 kW
Plant max working pressure : 6.0 Bar
Nominal yield : 500 – 900 HL/day
Dimensions (LxWxH) approx : mm 1900x1500x1700 h
Weight approx : 750 Kg
OPTIONAL
- PLC automation
- By means of a touch screen PLC control.
- PLC includes six operational programs:
- Feeding / filtration / emptying / total drain / rinsing / cleaning
- Employee has to select the required program and starting cycle.
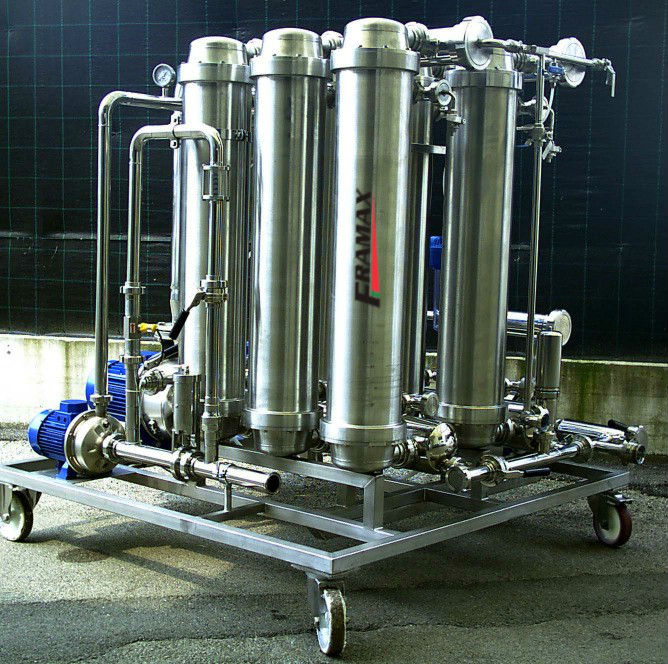
Packaging Detail:Seaworthy Crate, Cage, Pallet with Barrier bag accoring to shipping requirment |
Delivery Detail:Approx 30 to 60 days according to workload |