corless medium frequency small smelting furnace
Condition:New | Type:Induction Furnace,steel shell crucble | Usage:Melting Furnace | Place of Origin:Shanghai China (Mainland) |
Brand Name:SEHM | Model Number:GW-8-5000-1J | Voltage:690v | Power(W):5000kw |
Dimension(L*W*H):100000x6000x6000mm | Weight:20t | Certification:iso,ce | Warranty:1 year |
After-sales Service Provided:Overseas service center available | tilting system:hydraulic tilting | capacity:8ton | melting power:5000kw |
power type:single power or dual track | control cabinet:KGPS or IGBT with PLC or without | furnace body or crucible no.:2pcs | meling rate:8ton/hour |
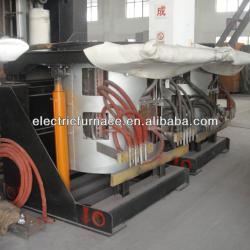
8t energy-conservation medium frequency induction furnace
(steel shell with magnetic yoke hydraulic tilting)small smelting furnace
induction meltig furnace can work with LF furnace ,ladle refining furnace , holding furnace , rolling mill mchine,conticaster
- Model number:rated capacity of furnace 8ton,rated power of medium frequency supply 4000KW.
Power Consumption:550/600 kwh/T
- Complete set supply range:furnace body 2set,furnace tilting device 1set,water cooling cable (6m) 8set, medium frequency supply cabinet 2set, capacitor cabinet (open type) 1set, low voltage distribution cabinet 2set, capacitance tank cabinet 1set, power tank 2set, hydraulic station system 1 set, water temperature and water pressure alarm 1set, furnace leak alarm 1set, the connect cable of medium frequency supply cabinet and capacitor cabinet 2piece, crucible 1set, Φ28 seamless steel tube 30metre, spare parts of equipment: KK 1piece, KP 1piece, master control board 1piece.
- Technical specification:6-phase incoming voltage of medium frequency supply source 950V, 12 pulse rectifier, output voltage of medium frequency supply 1650V. Rated power 4000KW, furnace body length4000, width3780, height3100, inductor inner diameterΦ1260, pillar height 2000.
- Fit out components:silicon-controlled rectifier (SCR) for KP tube 1500A/3500V 12 set;KK tube 2000A/2500V 16 set(connecting in series-parallel), low-voltage distribution cabine1000V/2500A with 2 universal circuit breaker, capacity of compensate capacitor 40000kilovar.
- Furnace tilting type: Hydraulic tilting
- Master control board:The control circuit used one single master control board, it designed to be whole, and reduced connecting line greatly, fixed reliability, so avoided safe failure. This control circuit board is high degree of integration, theαangle automatic adjusted especially, that let power output of the equipment always was on constant condition, and electric power can be saved over 3% in comparison with same kind product. Safe start-up and automatic frequency-sweep.
- Customer service: debugging , all the costs of seller’s experts go and work at abroad for return air tickets, accommodation and meals, will be borne by the buyer. The debugging period is 5 days, overstep the set time the buyer shall compensate the experts at USD 150 per day for delaying time. The seller should be responsible for the scene testing; After normal melting the seller should be responsible to guarantee repair or change of the faulty components in 6 months, such as master control board,reaction,compensate capacitor,hydraulic device,breaker,and furnace shell (except for lining break through, stoppage or shortage of cooling water supply for components).
2)Products standard and operating conditions
2.1Products standard:
GB10067.3-88 ‘Basic specifications for electroheat installations—Induction electroheat installations’
GB10067.1-88 ‘Basic specifications for electroheat installations—General’
GB10066.3-88‘Test methods for electroheat installations—Induction crucible furnace’
GB5959.1-88 ‘Safety in electroheat installations—General requirement’
GB5959.3-88 ‘Safety in electroheat installations—Particular requirements for induction and conduction heating installations and induction melting installations’
GB/T4280-93 ‘Medium frequency coreless induction furnace’
GB/T8669-1997 ‘Semiconductor frequency conversion devices for medium frequency induction heating’
2.2 Operating conditions
2.2.1Cooling water conditions
PH:7-8.5
Hardness:<10degrees(Each degree that 1Lwater contains less than 10mg calcium oxide)
Total solid content:<250mg/L
Water resistance:(Power)>100KΩ-cm
(Furnace)>2KΩ-cm
2.2.2Power supply conditions
- Three-phase voltage unbalanced<5%
- Voltage fluctuations <±5%
- Voltage waveform distortion factor <10%
2.2.3Geographical environment
a. Altitude above sea level <1000m
b. Temperature 5~40°C
c. Relative humidity <90%(20°C)
- No conductive dust, explosive gas and corrosive gas around the equipment.
- Avoid strong shake and concussion.
3)Electrical Technique Instruction
Electrical parts of the equipment include rectification transformer, low-voltage switch cabinet, medium frequency power cabinet, filter reactor, and compensation capacitor bank and water tank.
3.1 Rectifying transformer
This equipment uses special-purpose rectification transformer, which transforms 35KV or 10KV high voltage of the electrical network to 950V, which is suitable for the solid state power.
There is a no- load manual changer at the high voltage side of transformer, output voltage can be adjusted at-5%,0,+5%. It is used to suit the deviation of grid. In order to ensure the safety of silicon-controlled rectifier and avoid to impact on the grid, this transformer request the big short circuit resistance value 10%, simultaneously adds the shielding layer between the primary and secondary-coils. There are a gas relay and the oil thermometer on the power transformer, its output is interlock with high-voltage switch cabinet, when there appears the gas alarm or higher oil temperature, it will automatically turn off the power.
Cooling of the Transformer uses the oil-filled self-cooling.
3.2 Low-voltage switch cabinet
The low voltage switch-automatic air circuit breaker(DW15—1000V) is installed between the transformer output and the medium frequency power input, it is used in the make-and-break and isolates the overhaul of power source for maintenance.
The air circuit breaker has fast broken for overload protection and the no voltage release protection.
3.3 Medium frequency power source
Controllable medium frequency power supply is AC—DC—AC equipment. It uses silicon-controlled rectifier to change there-phase DC to single-phase AC. The equipment is strongly adoptive to any load, and is widely used in metal melting, heat treatment, and crystal’s growth. The medium frequency source made by our company has some special feature list below:
1,The cabinet uses GGD type cabinet structure, the arrangement of element is in one side, which is easy to install and maintain, the way of refrigeration is water-cooling or wind-cooling.
2,Rectifying Bridge (KP tube), Inversion Bridge (KK tube), Silicon-controlled rectifier; those elements are all made by famous companies, the main components of control circuits are import, that guarantee its stability and reliability.
3,The device is started by frequency-sweep zero-voltage soft start mode for separately-excited to self-excited, in the whole startup process, at any moment the loads change is traked by the frequency adjustor system, circuit and voltage adjustment closed loop system, which leads to the perfect soft start-up. This way has less effect to controlled silicon and it extends its life. Also, it has characteristics advantage such as both light, and heavy load easily start up.
4,The electric circuit uses our patent constant-power controlled circuit. In the working process, it will watch the change of voltage and current by itself, and base on that to determine the change of load, automatically adjust the power output that let the equipment always has the largest power output. Especially for melting, this constant–power control can realize power output as larger as possible. It improves melting speed efficiently.
5,No need for special surveillance. The equipment only has one power switch and a power adjustment knob. It is easily to be operated. After start, you only need to turn the power to the largest position; others will work automatically. When increase large number of material, the equipment can adjust the power itself. It won’t stop suddenly as a result of over current and over voltage.
6,As the melting is fast and the thermal efficiency is high, once output is improved. It always works under the highest volts dc (rectifyingα=0). The average output power can increase 12-20%. The melting cycle can decrease to 2/3 of primary one. Electric power can be saved over 10%.
7,The protective circuit is perfect, which let SCR parts always work under the safe range, and failure rate lower.
8,The device uses digital control circuit. It has high reliability. In the working process, three-phase current is balance. As the advantage in design, the sequence of three-phase power can be connected in any way, and the connection with capacitor cabinet or furnace body can’t distinguish phase angle, which made it the equipment can decide automatically and adaptive control. It is easy for installation and maintenance.
The line is used in AC—DC—AC parallel model; its system diagram is as follows:
ⅠPrinciple of main electric circuit
The 3-phase 50HZ AC is input to rectifying bridge through the fusible cut-out and breaker by its main circuit, which is changed to adjustable pulsating DC, after filtering by reactor it becomes smoothing A•C to be input to single phase inversion bridge, after inversion it becomes single phase alternating current (AC), and then the single phase AC source is input to load. The load circuit uses parallel connect oscillating circuit, this kind of inversion bridge is very adaptable for the load, and to be reliability and stability.
Except that the control system has fine protection system, in other parts of main electrical circuit there also have some protective component , each SCR has a RC absorption circuit, in can absorb the over voltage which comes out when element phase changing. To avoid damage element from short circuit and overload, to link a fast fusible cut-out at the input side of rectifying bridge.
ⅡIntroduction of control circuit
BSC14M—2 constant power SCR frequency changing source control triggering panel includes power supply,adjuster,phase changing control,protection circuit,phase-rotation adaptive circuit,startup calculation circuit,inversion frequency tracking,inversion impulse form, pulse blow-up and pulse transformer. This core part used special large ASIC—2 Microprocessor circuit, caused the control circuit to realize the digitization, which has good capability, high consistence and it is made in US. All the inside circuit are digital, except adjustor, rectifier trigger doesn’t need any adjustment; it has high reliability, good impulse symmetry, strong anti-interference ability and fast reaction, also because it has phase-rotation adaptive circuit, do not need synchronic transformer. So during the debugging, there is no need to adjust the phase-rotation and check the synchronization, only need is to connect KP SCR gate line to the control panel, then the rectifier can work.
Inversion circuit, we use frequency-sweep zero voltage startup, its function is better than normal one’s circuit, and it has automatic restart circuit that can avoid frequency changing source fails to start accidentally, so the successful start up rate is 98%. Frequency tracking circuit uses sampling average value, it improves the ability of anti-interference and it only needs sampling signal of frequency changing voltage, no need for the signal of slot capacitor’s current, so that you don’t need for extra frequency changing current’s phase-rotation, so during debugging and use, it won’t fail to start up, even if phase-rotation of frequency changing output line or sampling current indictor is reversed.
There’s an inversion angle adjustment circuit in inversion circuit, which can automatically adjust matching of load impedance to achieve constant power output, and can be made for “fast smelting” frequency changing source, to achieve time saving and electricity saving, aims to improve power factor of network side (this function can also be turned off). The main circuit of inversion is inside part of ASIC—2 integrate circuit, and also is digital.
A,BSC14M—2 control panel include 12 integrate circuit, 12 transistors, 7 trimmer potentiometers, 47 lead-in terminals, it is easy for installation.
B,Model description
ⅢMain technical parameter of main control panel
Lead-in rated voltage:100V~950V(50HZ)(Notice:R3,R7,R11DE matching).
Control power supply: Single-phase 17V/2A.
Feedback signal of frequency changing voltage: AC 12V/15mA.
Feedback signal of electrical current: AC 12V/15mA three-phase input.
Phase shift range of rectifying triggering pulse:α=0~1300.
Symmetry degree of rectifying triggering pulse:<1°.
Signal width of rectifying triggering pulse:>600μs double narrow, interval 60°.
Characteristics of rectifying triggering pulse: peak value voltage of triggering pulse:≥15V.
Peak value current of triggering pulse electrical:≥1A
Fore steepness of triggering pulse:≥0.5A/μs
Inversion frequency: 100HZ—10KHZ (Different specification: 100HZ,200HZ,500HZ,1KC,2.5KC,4KC,8KC.)
Signal width of inversion triggering pulse: 1/(16×inversion frequency)
Characteristics of inversion triggering pulse: peak value voltage of trigger pulse:≥22V
Peak value current of triggering pulse:≥3A
Fore steepness of triggering pulse:≥2A/μs
(inversion triggering pulse transformer is extra connection)
The largest size:290×240×30mm
Failure signal output:
When fail signal is received by control board, it will output a group of connecting points’ signal. The capacity: AC:5A/220V; DC:10A/28V.
Electrical circuit principle
The control circuit of power supply is made to a printing electric circuit board except the end trigger unit. Its function include power supply, rectifying trigger, adjustor, inversion, start up calculation, etc. All of them are digital circuit, except that adjuster’s is simulative circuit.
The core of the integrate circuit of the control panel is IC6 which is a large special integrate circuit. There are 3 ways of time clock input port, 31 ways input/output port. It’s inside function included: rectifying phase-shift trigger, phase-rotation adaptive, inversion trigger, inversion front-angle locking, inversion restart, over current and voltage protection, phase-failure protection, low water pressure protection, and under-voltage protection of control circuit, there are also three 0.2 second timers.
Working principle of rectifying trigger
This circuit includes 3-phase synchronization circuit, phase-rotation adaptive circuit, voltage-control clock circuit, digital trigger circuit and end drive circuit, etc.
Signal of 3-phase synchronization is directly from 3-phase input line of main loop, through the gate lead-in K4,K6,K2 of transistors, and it is filtrated by R3,C2,R7,C2,R11,C3, than through 6 photo electric coupler, to get 6 rectangular wave synchronous signal, their phase-rotation difference between each other is 60°, and it is input to 5P-10P of IC6.
There’s an inside phase-rotation adaptive circuit in IC6, so no need to differentiate phase-rotation for 3-phase alternating input of frequency changing source.
IC1C and ambient circuit form voltage-control clock, its signal output cycle linearity changes with output voltage VK of adjustor, voltage-control clock signal is input to 11P of IC6 as digital trigger timers CLOCK.
Digital trigger’s characteristic: to achieve the phase shift by count (clock pulse), 6ways rectifying phase shift trigger pulse are caused by IC6, IC2C, IC2D and other circuit form the pulse wide output circuit. 6ways rectifying phase shift trigger pulse are amplified by IC5 transistor matrix, it drives rectifying pulse transformer to output, here the pulse transformer uses in the way of reverse excitation.
Working principle of adjustor
There are 2 adjustors. Frequency changing voltage/current adjustor and inversion angle adjustor.
Voltage/current adjustor (IC3C) is a normal PI controller; it runs all the time during startup and run stage. Inversion angle adjustor (IC3B) is used to make the inversion bridge run stably at certainθ angle.
The working process of adjustor’s circuit can be divided into two situations, one is when voltage DC
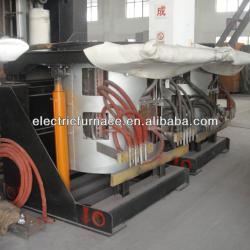
Packaging Detail:Plywood and frame container |
Delivery Detail:45days |