Cooling and heating temperature system control many reactors
Place of Origin:Jiangsu China (Mainland) | Brand Name:LNEYA | Model Number:SUNDI series | Application:Other |
Type:Other | After-sales Service Provided:Overseas third-party support available | Temperature:-100℃~+350℃ | Case material:SUS 304 |
Process control:PID PLC | Input&display:7-inch colour touch screen graph display | Communication:RS485 | Refrigerants:R-404A,R508B |
Evaporator:KAORI Plate heat exchanger | Data Record:U disk |
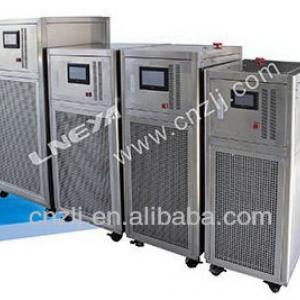
Dynamic Temperature Control systems | |
Description: Heating Refrigeration temperature control system is mainly applied to the glass reactor, metal reactor, bioreactor heating and cooling, temperature control, especially for needy during the reaction heating, exothermic process control. |
Advantages & Functions
Working temperatures from -100°C to +350°C
Previously unachievable performance
Intelligent temperature control
Maximum process stability and reproducibility
The fastest heating and cooling rates
High Cooling Power from 0.5 to 500 kW
Large temperature range without fluid change
Increased thermal fluid life
Incredibly compact
Brilliant 4 inch, 7 inch, 10 inch TFT touch screen with graphic display
Comprehensive warning and safety functions
Rapid cooling down from high temperature (from 300 °C)
Typical Applications:
Reactor Systems Autoclaves
Pilot Systems
Mini Plant Systems
Scale up for Operational Development
Double wall reactors
Advanced-Flow Reactors
Distillation Systems
Material Testing
Combinational Chemistry
Semiconductor Industry
Vacuum Chambers
Structure design
Reproducibility
Guaranteed reproducible thermoregulation results with the highest
possible dynamics.
Environmental protection
All the machine parts are made from recyclable materials.
Option is available for 100 % environmentally friendly refrigerants.
Adaptive Control
Varying research criteria and process demands changes the thermal load on the temperature control system. What does not change is the requirement for good control.
The solution is “Adaptive Control” which has the capability to automatically change with those demands. By building a multi-dimensional model of the process, the Adaptive Control Is able to automatically adjust its PID parameters to cope with and respond rapidly to sudden changes in the process. Operating in both “Jacket” and “Process” control, Adaptive Control provides responsive and close control. Rapid changes with no overshoot that is what Adaptive Control brings to the process – automatically and under all conditions. User defined ramp rates allows for faster or slower response.
Display Functions
Heating Cooling Temperature Control System Display – The Refrigeration system's multi – image display displays various information
1. Displays all the kind of process control temperatures.
2. Shows the liquid level of the heat conducting medium in the expansion vessel.
3. Shows indication for refrigeration system working.
4. Shows indication for heater working.
5. Shows indication for circulation pump working.
6. Displays the temperature control ( materials temperature control pattern, heat conducting medium temperature control ).
7. The temperature upper limit, lower limit control can be set.
8. The temperature difference between jacket & reactor material can be set.
9. Shows the alarm to add the liquid when it is empty.
10. The refrigeration compressor can be set to operate manually or automatically.
11. Simple Menu to use.
Displays Clear Curves
Can enlarge or shrink the curve and support U disk data exporting and export file as list form.
Simple way to Set Temperature Profiles
Shows detail information of Alarm Record
Programmer
Single temperature changes can be achieved using the linear ramp function. The easy to use programmer with 50 steps is available for more complex temperature requirements.
Individual steps can be pieced together to form a profile, we can program total 20 profiles one time input.
Process-relevant data is always in view
The control system graphical interface is easy to operate, gives user confidence and keeps the user continuously informed of all relevant process data. The colorful TFT display shows all information in plain text. Process temperature, internal (flow and jacket) temperature and all safety-relevant information can be read easily and quickly. The display can be varied as
required and in addition to a concise but comprehensive list of data. The most important information (set-point, actual, and internal / process temperature and Over Temperature limit) are shown in a larger format, making the essentials easier to read from a distance. The temperature resolution can be displayed to 0.1°C.
Embody capacity and dynamics.
Small in size big in power.
Dynamic Temperature Control systems combine the efficiencies of effective thermodynamics and modern microelectronics making it a highly efficient alternative to open bath temperature control technology. Dynamic Temperature Control systems are circulators without a bath. An expansion vessel for thermal expansion and contraction replaces the conventional bath. The expansion vessel is isolated from the thermoregulation unlike open baths.
The Dynamic Temperature Control systems principle uses minimal heat transfer fluid (HTF) volume and increased thermal transfer abilities through higher HTF flow rates, reduced HTF pressure and highly efficient heat exchange surfaces. This Increases the systems speed of response to changes in demand. Dynamic Temperature Control systems have the most rapid ramping rates, and are capable of cooling rates of more than 100 kW/hr
illustrative diagram
Maximum HTF flow
Improved pump and piping design together with reduced internal flow resistance gives higher HTF flows with lower HTF
pressures meaning more efficient thermal transfer and faster ramping of the process for the same power.
High temperature resistant low temperature magnetic drive pump or a leak-free high and low temperature shield-driven
pump reduces the risk of system leakage.
Circulation pump
LNEYA Dynamic Temperature Control systems in practice
In comparison to other thermal control systems, Dynamic Temperature Control systems differ sometimes considerably in their thermodynamic characteristics. In practice Dynamic Temperature Control systems offer definite advantages in your work: noticeably shorther heating and cooling times, better stability and reproducibility through the entire process chain, greater safety for expensive glass reactors and the contained substances, together with simple and easy operation.
Heat-Conducting Medium
It is important to choose the suitable heat-conducting medium, to make sure that system works stably.
To choose the suitable medium according to the working temperature of the system is essential.
The package for LNEYA heat conducting medium are 10L, 25L, 30L, 200L. When ordering the heat-conducting medium,the heat conduction medium for constant temperature control system, channel, and external circulation equipments.
Mode | KDOC-350 | KDOC-250 | KDOC-220 | KDOC-210 | KDOC-80 | UDOV-100 | UDOX-88 | VDOW-125 |
Temper range °C | -30~320 | -25~250 | -55~250 | -70~220 | -80~195 | -100~95 | -88~160 | -120~50 |
Color | colorless | colorless | colorless | colorless | colorless | colorless | colorless | colorless |
Smell | no harsh | no harsh | no harsh | no harsh | no harsh | harsh | harsh | harsh |
Density kg/m3 | 1000 | 1000 | 935 | 880 | 820 | 750 | 835 | 735 |
Freeze point°C | -60 | -60 | -90 | -100 | -100 | -134 | -130 | -145 |
Flash point°C | 280 | 200 | 211 | 134 | 87 | -6 | 54 | |
Boiling Point°C | 330 | 260 | 255 | 230 | 200 | 99 | 165 |
Connecting Pipe
Items | Temper range | Interface Dimensions |
Fluorine rubber hose | -30~220 | DN15DN20 |
Metal insulation pipe | -60~250 | DN15DN20DN25M24*1.5M30*1.5M38*1.5 |
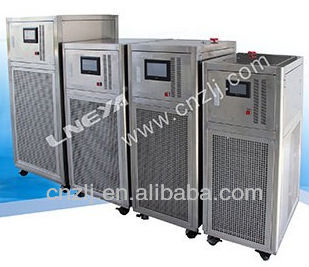
Packaging Detail:Standard export wooden package |
Delivery Detail:Within 20-25 working days |