CNC horizontal boring machine CPBR130 CPBR160
Condition:New | CNC or Not:CNC | Production Capacity:4 months | Place of Origin:China (Mainland) |
Brand Name:HHT | Model Number:CPBR130/160 | Voltage:change as customers' requirements. | Power(W):30/41kw, 37/51kw |
Weight:68t, 85t | Certification:ISO, CE | After-sales Service Provided:Engineers available to service machinery overseas | Automatic Grade:automatic |
Processing Types:Metal | cnc system:SIEMENS FANUC | Ball screw:I+F | Spindle bearing:SKF NSK IBC FAG |
Grating ruler:HEIDENHAIN |
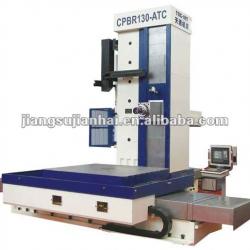
CNC horizontal boring machine CPBR130 CPBR160:
Model:CPBR130/160
Type: Planer type
Layout form: Horizontal
Specification:
Specifications Type | CPBR 130 | CPBR 160 | |
Spindle diameter | mm | 130 | 160 |
Diameter of milling spindle | mm | 221.44 | 240 |
Ram size | mm | 450×450 | 450×450 |
Spindle speed | r/min | 10-1500(Optioonal 5-2000) | 10-1200(Optional 5-1500) |
Spindle taper | - | ISO50 7:24 | ISO50 7:24 |
Power of spindle motor | Kw(S1/S2) | 30/41 | 37/51 |
Spindle torque | Nm | 3500 | 4000 |
Resisting force X Y Z B V W | N | 40000 | 50000 |
Torque of milling spindle | Nm | 3500 | 4000 |
Shank | - | JT50# | JT50# |
Pull stud | - | LDA-50 | LDA-50 |
Cross travel of table X | mm | 3000 | 4000 |
Vertical travel of spindle head Y | mm n | 2000(optional 2500 3000) | 2500(optional 3000) |
Longitudinal travel of column Z | mm | 1800(Option) | 1800(option) |
Ram travel V | mm | 900 | 1000 |
Axial travel of spindle W | mm | 800 | 900 |
Table rotation B | Angle | 360° | 360° |
Table size | mm | 2000×2000 | 2000×2500 |
T-slots (W×Space) | mm | 28×200 | 28×200 |
Max. load | kg | 20000 | 25000 |
Rapid traverse X Y Z V W B | Mm/min r/min | 10000/6000 6000 1.5 | 10000/6000 6000 1.5 |
Feedrate X Y Z V W B | Mm/min r/min | 1-6000 1-4000 0.005-1 | 1-6000 1-4000 0.005-1 |
Positioning accuracy X Y Z V W B | mm arc-second | ±0.015 ±0.025 ±5″ | ±0.015 ±0.025 ±5″ |
Repeatability accuracy X Y Z V W B | mm arc-second | ±0.01 ±0.02 ±3″ | ±0.01 ±0.02 ±3″ |
CNC system | - | SIEMENS/FANUC | SIEMENS/FANUC |
Weight | kg | 68000 | 85000 |
Structural Features:
1.Big basic parts such asthe lathe body, the columns, the table, the slide carriage, the headstock, and the back tail barrelare all high-strength resin bonded sand iron castings and receive two times of heat ageing treatment.
2.The Main Shaft: the main shaft consists of a boring shaft and a milling shaft with an imported main shaft bearing. The main drive system, which integrates an AC servo motor and two-stage mechanical gear shift, enables stepless speed regulation.
3.The Material Forming the Main Shaft: 38CrMoAlA. The surface of the main shaft undergoes nitrogen treatment and finishing with a hardness of above HV900.
4.Swivel Table: the swivel table can be positioned at any angle. The rotor axis adopts a twin-row cylindrical roller bearing, and the upper part of the shafting adopts a central unloading device. A swiveling feed mechanism is driven by an AC servo motor; the gear reduction box having a drive structure that double pinions preloaded by a butterfly spring drive a girth gear can automatically eliminate the gear drive gap and consequently ensure higher drive precision.
5.The Guide Rails: a Schneeberger MR heavy-duty roller straight line guide rail made in Switzerland is adopted for X,Y,Z,W-direction guide rail, a plastics sticking slide rail for B-direction guide rail;
6.The Feed Mechanism: the feed mechanism, which adopts X, Y,Z, W coordinate feeding modes, is driven by an AC servo motor.
7.The Balancing Mechanism: the headstock adopts a counterweight balancing device with two-point suspension, double-guide and rollers.
8.The Hydraulic System: famous brand hydraulic elements with their mounting size meeting international standards are adopted.
9.The Lubrication System:the X,Y,Z,B,W coordinate guide rails and the ball screw nut pair are lubricated by an automatic lubrication device with set time and fixed quantity; a main shaft transmitting gear and a bearing thereof are lubricated by circulating cooling oil; and the main shaft bearing and the screw bearing are lubricated by grease.
10. The Electric System: a SIEMENS840D system is adopted. The system, which adopts six-shaft control and free four-shaft interlock with a hand held control unit, can carry out control and management of the tool shed and gauge head of a facing head.
11.The detecting element: the X , Y , Z axes adopt grating rules and B axis adopts grating circular to form fully closed loop position detection; and the W axis adopts a coder to form semi-closed loop position detection.
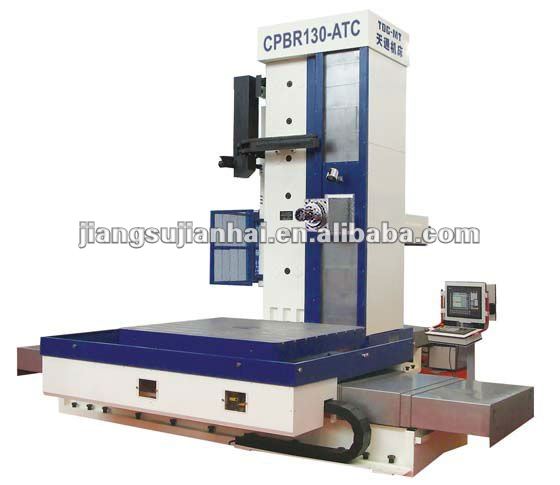
Packaging Detail:wooden package,with fumigation treatment. |
Delivery Detail:Three months, and will be confirmed again when place order. |