cnc diamond grinding wheel
Place of Origin:Jiangsu China (Mainland) | Brand Name:duoling | Model Number:many | Bond systme:Resin |
Abrasive Material:SDC | Machine:AKE Akemat, Utma & Walter | Technology:Japan | OEM:Accepted |
FEPA shape:12 A2 | Core:Aluminun | Diamond Grit:D181 (80/100) |

Cnc diamond grinding wheel
1.12A2 20 Degree Diamond grinding wheel
2.Application of12A2 20 Degree Diamond grinding wheel:
Used for sharpening and finishing of front sufaces reamer teeth,cutter,circular saws,drawing dies and tools made of hard alloys.
3. Specification of12 A2 20 Degreee diamond grinding wheel:
Diameter(D) | Height (T) | Thickness(X) | Width(W) | Hole(H) | ||
50 | 10 | 2 | 2 | 10 | ||
75/80 | 13 | 3 | 3 | 10,20 | ||
100 | 13 | 3,5 | 3 | 20 | ||
125 | 13 | 3 | 5 | 32 | ||
150 | 16 | 3 | 5 | 32 |
4. Grit Size for 12A2 diamond grinding wheel
a.#100 Roughing
b.#120 Cutting-off
c.#150, #180 Medium stock removal plus good finish
d.#220, #320 Finishing
e.#400 Fine finishing
5. Diamond Concentration of 12A2 Diamond grinding wheel
a.50 % for Free cutting – most economical for broad area of contact
b.75% for General purpose
c.100% for Most durable – best form holding
6.GENERAL RULES WHICH APPLY TO SUPERABRASIVES ARE:
1. Storing and Handling
Wheels should be stored separately and protected against shock and contact to reduce the risk
of damage. Wheels may be left mounted on spindles and flanges but should be wrapped
before storage. Otherwise keep wheels in their boxes when not in use.
2. 2. Coolant
It is always advisable to use superabrasives with coolant as performance is superior (sometimes by a factor of 10 times). Many coolants are available but water with an addition of rust preventor or soluble oil (1.5 to 2%) is often adequate. Whilst giving longer life to wheels the use of coolant also minimises the thermal damage to the workpiece and wheel. This guarantees workpiece integrity and dimensional accuracy by reducing heat distortion to a minimum. The use of coolant will also help in obtaining a better surface finish. It is generally accepted that straight oils generate a better finish than emulsion or simple aqueous solutions,and markedly better than the absence of any fluid. Coolant also acts as a lubricant and lowers spindle power drain, it reduces the force needed to remove stock thereby lowering heat generation and increasing wheel life. The final function of coolant is to remove swarf from the abrasive rim. This prevents wheel loading and helps to maintain freeness of cut. To get the best from your coolant flood the workpiece/wheel contact area. Have a large tank to allow swarf to settle out and if possible filter out impurities and fine swarf. A small trickle of coolant occasionally applied is worse than no coolant at all. This causes alternate heating and quenching, which can cause damage to the wheel and workpiece. A good way to apply coolant
is to allow the centrifugal force of the wheel to deliver it in a steady stream to the point of grinding contact.
3.Wheel Mounting and Truing
Unless mounted correctly, Diamond and CBN wheels will not perform well. For correct mounting the flanges and faces must be in good condition. When truing, the wheel rim is cut or abraded to develop perfect roundness and concentricity with the spindle, and the desired profile. Toreduce the amount of rim material to be removed in truing, the wheel should be mounted as true as possible. Truing is most important with peripheral wheels. An out of round wheel will pound the workpiece, wear fast, and produce poor finishes. The new wheels supplied by Diamond Edge have already been trued and conditioned and should be able to set up with the aid of a dial test indicator to runout not more than 0.01mm (0.0004”). Clamp the wheel with gentle pressure on the flanges and tap into truth with a nylon faced hammer, then tighten the flanges securely. Once mounted true it is advantageous to leave the wheel on its mounting provided it is stored carefully. If a wheel has become out of round during use, or is unable to be adjusted on the mount, it may be necessary to true it by one of the following methods:
1. Brake controlled truing device.
2. Mild steel block.
3. Impregnated diamond nib.
4. Rotary powered diamond truing device.
4. Dressing
Dressing is needed when the wheel is showing poor cutting characteristics. This may be accompanied by heating of the wheel and/or workpiece. After truing and if they become clogged or dull during use, superabrasive wheels need to be dressed to expose the abrasive crystals. This can be done easily and quickly with a white aluminium oxide dressing stick containing fine (220 grit) vitrified abrasive. The dressing stick should first be soaked in water and then be pushed by hand or using a holding device evenly into the wheel surface, wearing slowly initially, but once the wheel opens up, very quickly. When the grit can be felt with the thumbnail, the wheel is dressed enough. If possible, coolant should be used during dressing.
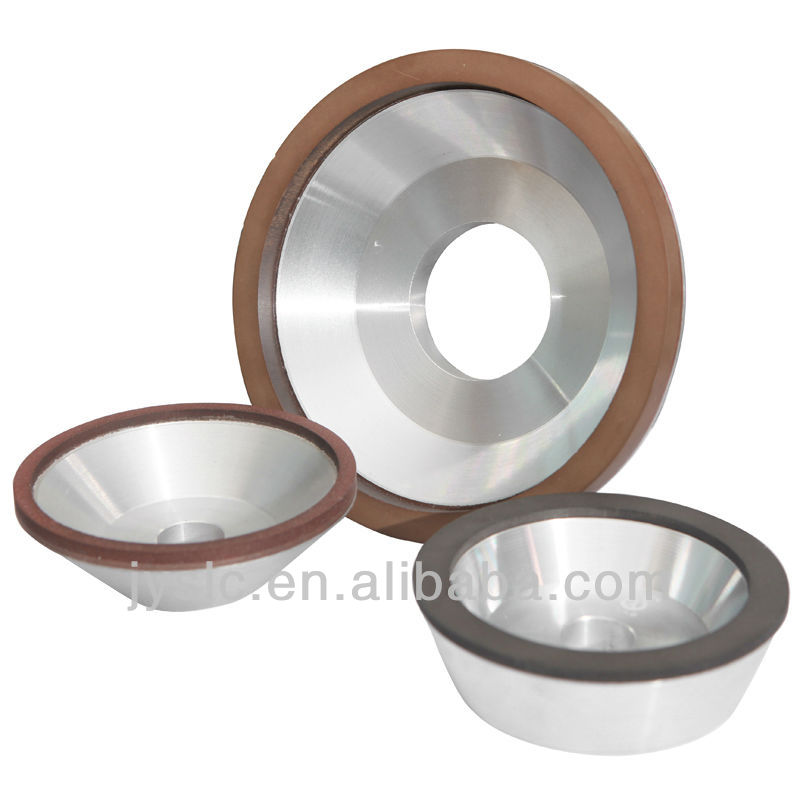
Packaging Detail:Paper boxes or as customer's requirements |
Delivery Detail:15 days |