CNC Busbar Punching Shearing Machine
Place of Origin:Shandong China (Mainland) | Brand Name:Euro-Asia/Gaoji | Model Number:GJCNC-BP | Condition:New |
After-sales Service Provided:Engineers available to service machinery overseas |

CNC Busbar Punching Shearing Machine
CNC Busbar Punching and Shearing Machine -GJCNC-BP is a professional high efficient and high accurate busbar processing machine controlled by computer.The punching dies,shearing dies and embossing dies are put at the tooling library.This machine can finish hole punching(round hole, oblong hole etc) embossing, shearing, grooving, cutting filleted corner etc.The machine can realize auto rotating of clamps for long busbar, human intervention is not needed.The finished workpiece will automatically delivered via the conveyor.This series machine can match with CNC bender to form busbar processing production line.
1.The operating software is a special aided design software(GJ3D)developed by our company,which can be connected so as realize auto program .It took the lead an applies the 3D graphic technology is world-class level.Being convenient and fast,the operation can demonstrate the shape of copper processing intuitively an three-dimensionally,calculate the hole punching/shearing and bending position,automatically from machine code,reduce the time of manual code and avoid the possibility of false manual code .The software can demonstrate the whole process of punching,shearing and bending,and prevent effectively the material waste because of input fault.
2.A single setup X-axis forms maximum 2000mm.It adopts primary,secondary clamps structure working at the same time to reduce the quality requirement of busbar’s flatness and degree of scoliosis. In the process,it can clamp busbar automatically,save labor and improve the efficiency and accuracy.
3.The stainless steel conveyor can be used to convey the workpiece and improve efficiency to guarantee no wear of the workpiece,long service time and high reliability.
4.Human-computer interface, the operation is simple and can demonstrate real-time the operation status of the program,the screen can show the alarm information of the machine,it can set the basic die parameters and control the machine operation.
5.The machine adopts high accurate ball screw transmission and straight guide to guarantee high precision and fast efficiency.The adopted component is world-famous,with long service and good quality.
6.Tooling library has 7 sets of tool stations(including one shear die,one bend die and five punch die).The machine adopts integrated shear and can finish the shearing of busbar once to guarantee the flatness of cross-section and improve processing efficiency.The removal and installation of dies is simple,reliable and easy-going,which can guarantee the high production efficiency in the condition of changing dies frequently .All the used dies are produced by famous domestic die manufacturers so as to meet the requirements of accuracy and performance.The impact of the number of mold≥50 thousand.
Main Technical Parameter
Name | Unit | Parameter | ||
Nominal Force | Punching Unit | kN | 500 | |
Shearing Unit | kN | 500 | ||
Embossing Unit | kN | 500 | ||
Location Speed of X-axis | m/min | 48 | ||
Max Stroke of X-axis | mm | 2000 | ||
Max Stroke of Y-axis | mm | 530 | ||
Max Stroke of Z-axis | mm | 350 | ||
Beat Cylinder Stroke | mm | 45 | ||
Beat Frequency | HPM | 55 | ||
Dies Bits | Punching Die | 5 | ||
Shearing Die | 1 | |||
Embossing Die | 1 | |||
Control Axes | 3 | |||
Pitch Control Accuracy | mm/m | ±0.20 | ||
Max Punch Diameter | mm | Φ32(Copper Thickness <12mm) | ||
Max Cross-sectional Area | mm2 | 160×60 | ||
Max Allowable Plate(LxWxT) | mm | 6000×200×15 | ||
Total Weight | kg | 7600 | ||
Host Area(LxW) | mm | 7500×2980 | ||
Total Power | Kw | 21 |
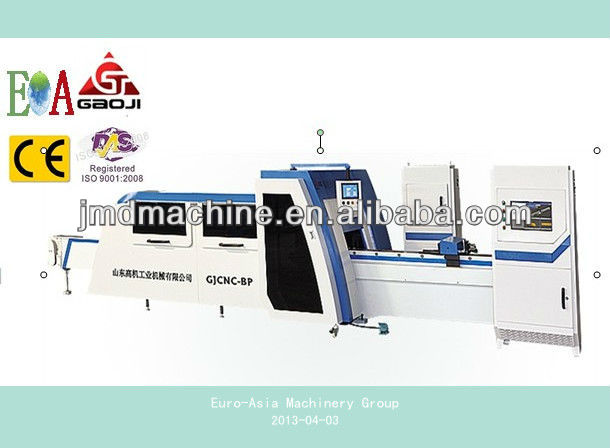
Packaging Detail:Export standard free-fumigation wooden case |
Delivery Detail:Within 15 days after receiving the 1st deposit |