Blast Furnace
Condition:New | Type:Blast Furnace | Usage:Melting Furnace | Place of Origin:Beijing China (Mainland) |
Brand Name:DSCD | Model Number:DSCD-BF450 | Effective BF Volume:320m3 | Annual Average Productivity:3.0~3.2t/m3.d |
BF Top Pressure:0.08~0.12MPa | Blast Temperature:1100℃ | Overall Fe Content:more than 59% | Slag Rate:more than 320Kg/t |
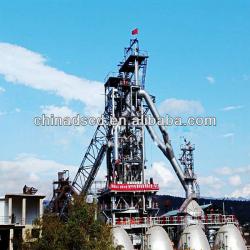
Description of Blast Furnace
DSCD, after years’effort, has had more than 200 employees for blast furnace installation and construction, 5 senior engineer for technolical research and development, 12 engineers for professional technical design, and 30 skillful technicians for blast furnace sintering and metallurgical process, including furnace foreman, hot air worker, shift foreman, foreman, technologist and analyst for operation and maintenance service. DSCD is the qualified general technical contractor for nationwide small and medium sized metallurgical enterprise project and production operation management, and sign the production technical contract with these enterprises. Furthermore, DSCD can carry out the technical improvement for blast furnace and sintering, solve the problems and manufacture various blast furnace and sintering equipment with advanced process and reliable quality.
With the profound corporate culture, professional staff and advanced management philosophy, DSCD has cooperated with design institutes to share the information and technology. After years of joint effort, DSCD is striving for the new goal.
Overview of Blast Furnace Ironmaking Basic Principle
Blast furnace is a cylinder high-temperature reduction reaction vertical metallurgical furnace with steel plate as shell, refractory brick as inter lining and refractory brick or ceramic cup structure as bottom. The blast furnace body is comprised of furnace top, throat, body, waist, bosh, hearth and bottom from top to bottom. For the blast furnace Ironmaking technology has characteristics of better economic indicator, simple process, large production capacity, high production efficiency and lower energy consumption, the iron made from this method has taken up great proportion of total iron output in the world. The iron ore, coke and agent for slagging (limestone) are put into the furnace from top, and the preheated air is given from tuyere on bottom of furnace during production. The coal in coke and coal powder injection (heavy oil and natural gas) at high temperature and oxygen in air are burning to generate the blast furnace gas, such gas absorbs the oxygen of iron ore during rising, so as to obtain the iron from the iron ore. The melted iron will discharge from the outlet. The unreduced impurity and limestone in iron ore are combined to produce the slag discharging from outlet. The gas produced exhausts from top of furnace, and serves as fuel for hot blast heater, heating furnace, coke furnace and boiler after dedusting. The major products melted in blast furnace include cast iron and blast furnace slag as well as gas.
Raw Materials in Blast Furnace Process
Generally, a total of raw materials (including 1.5-2.0T iron ores, 0.4-0.6T cokes, 0.2-0.4T fusing agents) are required for processing 1T cast iron. The sufficient raw materials are required to ensure the continuality of blast furnace process.
The blast furnace is processing in a continual manner. A generation of blast furnace (from starting process to interruption for overhaul) can produce for several years. During processing, the iron ore, sinter ore, pellet ore, coke and fusing agent are loaded continuously from top of furnace (this part consists of material and hopper, while the modern blast furnace consists of bell-shaped valve furnace top and material-free bell-shaped furnace top), and the hot air (1000~1300°C), oil, coal or natural gas alike fuel is injected into the tuyere at bottom of blast furnace. The iron ore loaded into the blast furnace is mainly the compound of iron and oxygen. The coal of coke and injected material and carbon monoxide generated after burning capture the oxygen in iron ore to get the iron, which is the reduction process. The cast iron is made from iron ore with reduction process and the melted iron is discharged from outlet. The gangue and coke in iron ore, ash in injected material and limestone are combined to form the slag discharging from the iron and slag outlet, the gas is exhausted from the furnace top for industrial purpose after deducting. The modern blast furnace can use partial of gas to generate electricity with high pressure at furnace top.
Smelting Process
The cold air from the blower, after heating to 800~1350°Cin hot blast heater, is sent to the hearth continually via the tuyere, with the blast heater, the coke in front of it is burned to produce the reducing gas with temperature exceeding 2000°C. The rising high temperature gas flow preheats the iron ore for a series of physical and chemical change, thus the heat exchanging and physical and chemical reaction are conducted between the stock column and ring gas flow.
The capillary water in dropping material evaporates immediately at 100~200°C, while the crystal water in limonite and gangue dissolves and evaporates at 500~800°C. The major agent limestone, dolomite, and other carbonate as well as sulfate dissolve in furnace. The iron ore starts reduction in blast furnace at 400°Cor lower temperature, some ferric oxideis melted into slag in high temperature area at bottom of furnace, and then undergoes reduction to produce the iron from the slag.
The coke can not be melted in the blast furnace, but gasified in front of tuyere, a few cokes are gasified as CO during reduction of oxide, and the iron ore starts softening in partial reduction process when the temperature rises at 1000~1100°C, and then it is fully smelted at 1350~1400°C, even drops over 1400°C. Due to the counter current heat exchange, the following areas with different temperature are formed: Area I is the dry area comprised of ore and coke, and it is also the bulk zone; Area II is the softening zone comprised of softening layer and coke layer where the ore starts smelting till fully smelting; Area III is the liquid slag and iron dipping zone where only the coke is in solid state, and Area IV is the spherical coke area where the coke is swirling and burning strongly, and it is also the major production base for internal blast furnace heat and gaseous reducing agent.
The raw material for blast furnace smelting mainly includes the iron ore, fuel (coke) and fusing agent (limestone).
The blast furnace smelting is a continual process in which the iron ore is reverted to cast iron. The solid raw materials such as iron ore, coke and fusing agent are proportionally loaded into the furnace via the furnace top charging device, and a certain height should be maintained with the blast furnace throat material level. The coke and ore form the alternative layer structure in the furnace. The ore is deoxidized gradually during falling to be the iron and slag that are discharged from the iron and slag hole.
Therefore, procurement of raw material is very vital for the cast iron manufacturer or steel mill.
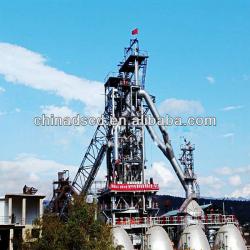
Packaging Detail:Seaworthy packing |
Delivery Detail:According to buyer's requirement |