automatic newly-designed high perfomance whole stainless stainless steel 316L milk powder production euipment
Condition:New | Type:Spray Drying Equipment | Place of Origin:China (Mainland) | Brand Name:JY |
perfomance:good |
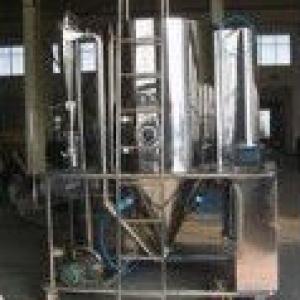
Owned by Junyu Industrial Group, Shanghai Junyu Machinery Enterprise is a high-tech company specialized in many fields, such as food and beverage machinery, stainless steel products, hardware and electric equipment, electric elements, wires and cables, hotel facilities, general merchandise, textile products, packing materials and electrical cabinets and related parts.
With the operation concept of "Professionalism, Sincerity and Trustworthiness", our company has been devoted to providing world-class products and service. Through years of development, we have constantly enhanced our expertise and innovation, sparing no efforts to provide sincere and excellent service, all of which have helped us gain the markets in Europe, the Middle East and Southeast Asia. We have won a high reputation among clients.
To become a "reliable brand supplier" is the objective of our enterprise, and this is also what we always keep in mind to motivate ourselves. Serving as the agent for many world-renowned brands of top quality, we always expect to provide you, at the very moment, with the most all-around solution on site and perfect products and service as well.
Enterprise Objective: Product supplier with professionalism, sincerity and excellence Reliable brand supplier for customers Operation Concept: Professionalism, Sincerity and Trustworthiness Service Mission: the best products, perfect service and reasonable price
Centering on all the customers' needs and aiming at improving productivity and quality, we should try to provide clients with the most possibly all-round solution on site through constant introduction of advanced technology.
Spray dryingis a method of producing a dry powder from a liquid or slurry by rapidly drying with a hot gas. This is the preferred method of drying of many thermally-sensitive materials such as foods and pharmaceuticals. A consistent particle size distribution is a reason for spray drying some industrial products such as catalysts. Air is the heated drying medium; however, if the liquid is a flammable solvent such as ethanol or the product is oxygen-sensitive then nitrogen is used.[1]
All spray dryers use some type of atomizer or spray nozzle to disperse the liquid or slurry into a controlled drop size spray. The most common of these are rotary disks and single-fluid high pressure swirl nozzles. Alternatively, for some applications two-fluid or ultrasonic nozzles are used. Depending on the process needs, drop sizes from 10 to 500 µm can be achieved with the appropriate choices. The most common applications are in the 100 to 200 µm diameter range. The dry powder is often free-flowing.[2]
The most common spray dryers are called single effect as there is only one drying air on the top of the drying chamber (see n°4 on the scheme). In most cases the air is blown in co-current of the sprayed liquid. The powders obtained with such type of dryers are fine with a lot of dusts and a poor flowability. In order to reduce the dusts and increase the flowability of the powders, there is since over 20 years a new generation of spray dryers called multiple effect spray dryers. Instead of drying the liquid in one stage, the drying is done through two steps: one at the top (as per single effect) and one or an integrated static bed at the bottom of the chamber. The integration of this fluidized bed allows, by fluidizing the powder inside a humid atmosphere, to agglomerate the fine particles and to obtain granules having commonly a medium particle size within a range of 100 to 300 µm. Because of this large particle size, these powders are free-flowing.
The fine powders generated by the first stage drying can be recycled in continuous flow either at the top of the chamber (around the sprayed liquid) or at the bottom inside the integrated fluidized bed. The drying of the powder can be finalized on an external vibrating fluidized bed.
The hot drying gas can be passed as a co-current or counter-current flow to the atomiser direction. The co-current flow enables the particles to have a lower residence time within the system and the particle separator (typically a cyclone device) operates more efficiently. The counter-current flow method enables a greater residence time of the particles in the chamber and usually is paired with a fluidized bed system.
Milking machines
Milking machines are used to harvest milk from cows when manual milking becomes inefficient or labour intensive. One early model was patented in 1907.[8]The milking unit is the portion of a milking machine for removing milk from an udder. It is made up of a claw, four teatcups, (Shells and rubber liners) long milk tube, long pulsation tube, and a pulsator. The claw is an assembly that connects the short pulse tubes and short milk tubes from the teatcups to the long pulse tube and long milk tube. (Cluster assembly) Claws are commonly made of stainless steel or plastic or both. Teatcups are composed of a rigid outer shell (stainless steel or plastic) that holds a soft inner liner orinflation. Transparent sections in the shell may allow viewing of liner collapse and milk flow. The annular space between the shell and liner is called the pulse chamber.
Milking machines work in a way that is different from hand milking or calf suckling. Continuous vacuum is applied inside the soft liner to massage milk from the teat by creating a pressure difference across the teat canal (or opening at the end of the teat). Vacuum also helps keep the machine attached to the cow. The vacuum applied to the teat causes congestion of teat tissues (accumulation of blood and other fluids). Atmospheric air is admitted into the pulsation chamber about once per second (the pulsation rate) to allow the liner to collapse around the end of teat and relieve congestion in the teat tissue. The ratio of the time that the liner is open (milking phase) and closed (rest phase) is called the pulsation ratio.
The four streams of milk from the teatcups are usually combined in the claw and transported to the milkline, or the collection bucket (usually sized to the output of one cow) in a single milk hose. Milk is then transported (manually in buckets) or with a combination of airflow and mechanical pump to a central storage vat or bulk tank. Milk is refrigerated on the farm in most countries either by passing through a heat-exchanger or in the bulk tank, or both.
In the photo above is a bucket milking system with the stainless steel bucket visible on the far side of the cow. The two rigid stainless steel teatcup shells applied to the front two quarters of the udder are visible. The top of the flexible liner is visible at the top of the shells as are the short milk tubes and short pulsation tubes extending from the bottom of the shells to the claw. The bottom of the claw is transparent to allow observation of milk flow. When milking is completed the vacuum to the milking unit is shut off and the teatcups are removed.
Milking machines keep the milk enclosed and safe from external contamination. The interior 'milk contact' surfaces of the machine are kept clean by a manual or automated washing procedures implemented after milking is completed. Milk contact surfaces must comply with regulations requiring food-grade materials (typically stainless steel and special plastics and rubber compounds) and are easily cleaned.
Most milking machines are powered by electricity but, in case of electrical failure, there can be an alternative means of motive power, often an internal combustion engine, for the vacuum and milk pumps. Raghav Gowda from Karnataka, India has developed a low cost environment friendly milking machine which uses a 2-piston reciprocating pump operated manually for creating vacuum. Milk cows cannot tolerate delays in scheduled milking without serious milk production reductions
Milk powders
Milk is also processed by various drying processes into powders. Whole milk, skim milk, buttermilk, and whey products are dried into a powder form and used for human and animal consumption. The main difference between production of powders for human or for animal consumption is in the protection of the process and the product from contamination. Some people drink milk reconstituted from powdered milk, because milk is about 88% water and it is much cheaper to transport the dried product.
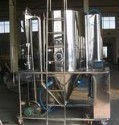
Packaging Detail:wooden box |
Delivery Detail:ASAP |