automatic kraft paper production line
Condition:New | Product Type:kraft paper production line | Processing Type:Pulp Molding Machine | Place of Origin:China (Mainland) |
Brand Name:RHO | Model Number:2100MM | Voltage:380/420 | Certification:ISO |
Warranty:2 YEARS | After-sales Service Provided:Engineers available to service machinery overseas | Pulp material:Waste paper, wood, etc |
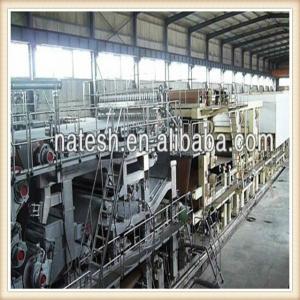
Description
automatic kraft paper production line
RHO Group of companies introduced Kraft Paper production machines to produce International stranded Kraft Paper productionmachine group isdesignedon German technology,and we fully reform the design of the equipment with most upto date international 3 dimensiondesign software (proENGINEER), and the design of the automatic production line is inaccordance with the national design criteria of the People’s Republic of China.
All machine parts, standardized parts and gearwheels are in metric system,100% made in China. The main parts of the machine group are withdrawing for maintenance and calibration purpose. : Electric system design criteria of theKraft Paper productionmachine groupThe design of the electrical system of the machine group is in accordance with the international
Advantage of using RHO Kraft Paper Production line
Scope of the production machine
1: Raw material can use recycle paper, paper board, wood, wooden materials, husk etc
2: Product feasibility /can produce
Kraft paper,Semi Kraft paper,One side waxing / oil proof paper,Double side waxing / oil proof paper,Double colour paper (top side with white colour and bottom brown).
Hypothesis of the production line
1: Output paper: High strength fluting paper, Liner paper,
2: Paper output weight: 80-150g/m2
3: Paper width: 2200mm
4: Wire width: 2400mm
5: Machine design speed: 150m/min
6: Machine operational speed: 80-120m/min
7: Production capacity: 30tones per day – can reach up to 50 tones per day by adding heating rollers
8: The gauge: 3100mm
10: Pressure type: pneumatic pressure device
11: Driving type: use AC frequency conversion, and driving by step
12: Pulp formation type: pressure mould former
13: Machine design: squaring box type, including left and right hand machine, high speed running in safe and safety environment.
14: Dryer: Wire-releasing part: ≥18-24%
Squeezing-mill releasing part: ≥38-40%
Manufactured paper dryness: 90-92%
15: Calculated running hours in a day: 22.5 hours
16: Calculated outputting rate: 97%
17: Calculated finished product rate: 95%
18: Layout type: one sheet layout including right machine
Technical design
Pulping, paper making and processing equipment adopt one-stop process design. This advanced composite design occupies small space for convenient operation and management with high level of security and atomization , and assured consistent production with steady quality.
This equipment has allocated with pulping pressure mould former, which is the most advanced mesh design. It can pulp from different tubes and fast and uniformly dehydrate into mould with extreme pressure. The produced paper is uniform and flat, good durability for lengthwise force and transverse force. Small difference between paper width has made it excellent as the fourdrinier machine. It has fitted multi-varieties and flexible quantifying scope through adjusting the pulping press. This is just coincide with the high speed of the machine and can not reject the pulp. So it has improved the production yield and increased the economic benefit.
Water, electricity, air and vapour requirement:
2.1:Electric power:
Installed power:AC1000V±10%
Voltage: AC380V 220V±10%
Frequency: 50HZ±1%
2.2: Compressed air:
Dielectric pressure: (air supply)0.6-0.7Mpa
The highest temperature: 35°C
Quality: need filtrating
Working air pressure: above 0.6Mpa
2.3: Compressed air for the meter:
Dielectric pressure: 0.5-0.6Mpa
The highest temerature: 35°C
Quality: filtrated, unoiled and arefaction
Working air pressure: above 0.5Mpa
2.4: Water:
Branch water and primary water: clear and colourless water without sand, neutral PH scale.
2.5: Vapour:
Working pressure: 0.3-0.4Mpa
Testing pressure: 0.8Mpa
Advanced Frequency Converting Controlling System
The modern papermaking equipment has widely developed with high technology. And this development is going to be more advanced with more accurate and reliable structure safety at high speed. For improving production capacity of the machine, thus designed with digital frequency converting controlling system to realize the modernization and high speed of the machine.
3.1: Controlling way: Adopt Siemens or Sanken inverter and high quality low voltage apparatus.
3.2: The main core hardware supporting every branch transmission point goes with a AC Inverter, indicator lamp, air switch, terminal board and so on; these all sino-foreign joint products.
3.3: Transmission control cabinet - All adopt standard GGD control cabinet, including power supply cabinet, transmission cabinet.
3.4: Control panel - Including main transmission operational panel.
3.5: Software and design information:
3.5.1. PLC applications software, speed chain, current control and telecom software.
3.5.2. Providing system schematic manual, external wiring diagram and cable list.
3.5.3. Providing technical specification of system unit, operation, running and configuration software.
Paper making / Dryer part
1: The cylinder part: Φ 1500mm×2400mm 4 stainless steel mesh cylinder mould, material: s.s.304, Φ 500mm×2400mm 5 couch rolls (including 1 returning roll), shore harness 38°±2, pneumatic compression device, equipped with turning roll device, and attached with 4 pressure mould former(made of polyethylene board).
2: The press part:1 pre-press,Φ 550mm×2400mm 1 stone rolls, Φ 500mm×2400mm 1 rubber rolls; 2 main press,Φ 750mm×2400mm 2 stone rolls, Φ 700mm×2400mm 2 rubber rolls; shore hardness 95°±2, and pneumatic compression device(standard height and moderate rubber roll)
3: The dryer part: Φ 1500mm×2400mm 16 dryer cans,2 of them are chroming. arrangement pattern (10+sizing machine+6), and pneumatic compression device. Equipped with pneumatic guide and electric mesh-fastener.
4: Winding part: 2100mm cylinder winding paper machine and frame style rewinding machine.
5: Driving and controlling part: using of AC frequency conversion, and driving by step.
Pulping machine part.
1: 2100mm multi-dryer cylinder and multi-wire paper machine 1 set
2: Exhausting hood 2sets
3: Flow fan 2sets
4:Model 15 Vacuum pump 1set
5: Suction box 4sets
6: Pressure mould former 4sets
7: 2100mm winding machine 1set
8: 2100mmframe stylerewinding machine 1set
9: 2100mm sizing machine 1set
10: Air compressor (gas cabinet, string and nozzle complete set)1 sets
11: Paper transducer(Siemens) 1set
12: Total workbench , ladder, handrail whole sets
13: High-post box 2sets
14: Pulp-modulating box 2sets
15: 5 m3 water pulp shredder 2sets
16: 2m2 shaking screen 2 sets
17:Pressure-flow within sieve 1 set
18: Double suction pulp-150 1 set
19: 450 double pulping machine 2 sets
20: Φ700 thruster 4 sets
21: Pulp-150 6 sets
22: Pulp-200 2 sets
23: 606 desander 12sets 2groups
24: 4T Gas fired-boiler (with Siemens burner) 1set
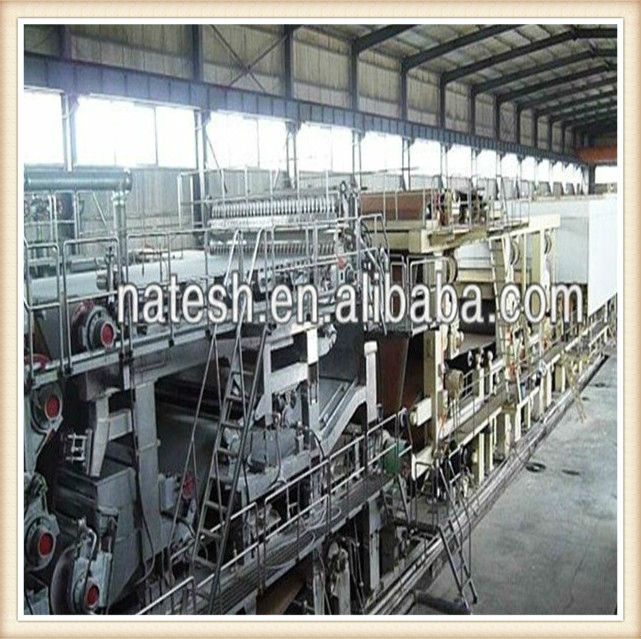
Packaging Detail:Sea Worthy strong ply wood box suitable for multiple handling |
Delivery Detail:45 days |