Automatic bag unloader
Place of Origin:Shanghai China (Mainland) | Brand Name:BPE | Model Number:BBU | After-sales Service Provided:Engineers available to service machinery overseas |
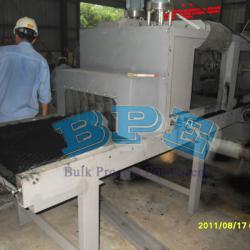
Automatic bag unloader, bag slitting and emptying systems
Perfect solution for all your bag discharge problems
The method of operation is simple but very effective. It ensures that the bags are emptied with minimal residue (0,01% - 0,5% for free flowing products). By the appropriate design, the “spliteter” can be operated by one man only and offers you an economic solution for your bag emptying problems. The “Splitter” machine can be directly placed above a discharge point. If this is impossible or not desired, then TBMA can offer you a wide range of pneumatic and mechanical conveying systems to suit your specific needs.
Dust-free and safe working conditions All access ways to the machine interior are fitted with safety switches. The machine allows simple cleaning in order to handle various products without contamination. A dust filter with extraction fan can be mounted directly on top of the machine or pipe connections can be mounted to allow ducting to a filter unit or central dust collecting system. |
1. Bag centralization – Machine inlet The bags can be fed to the inlet of the machine by roller or belt conveyor. By either method the bags are presented to a set of grip faced powered rollers situated within the machine inlet. The powered rollers propel the bags forward between adjustable side guides to centralise the bags prior to the main twin chain conveyor of the “Galahad” machine. | |
2. Automatic location A bag passing through the centralising guides is automatically collected by the twin chain conveyor. The twin chain conveyor is equipped with a series of knife points to grip the edges of the bag. A set of adjustable rollers exert pressure on the bags, to ensure that they are fully impaled on the knife points of the conveying chains. | |
3. Bag slitting The conveyor chains transport the bags directly to a centrally mounted circular rotating knife which is driven by a separate motor. The rotating knife is adjustable for cutting depth. Bags are conveyed across the rotating knife and are slit open lengthwise. | |
4. Product discharge After being opened the bags remain firmly held by the knife points of the conveyor chains. The bulk of the bag contents are now discharged by gravity via the flanged outlet connection. | |
5. Vibration of bags In order to ensure optimum discharge and minimal retention of product, the conveyor chains are vibrated by pneumatic vibrator units. The vibration effect is adjustable for frequency. | |
6. Empty bag discharge The empty bags progress to the head shaft of the chain conveyor and are released from the knifepoints by a rotating discharge drum. The empty bags are discharged down the exit chute of the machine where they can be collected by either a bag compactor or automatic baling press. |
By clicking the video above you can get a brief impression of
the automatic bagslitter and emptying machine in operation
Ancillary Equipment - Complete Installations “Made to Order”
For example:
- Dust filter unit
Mechanical- or Reverse Jet dust filter in several executions place don top or next to the machine. An integrated dust filter is placed on top of the machine directly above the cutting- and vibration area. The “splitter” can be fitted with 3 pipe connections for ducting to an externally placed dust filter. Choice of type of filter is determined by the product handled. - Operator/control panel
Fitted with motor contactors and motor protectors. Control facilities include door mounted LCD display for all alarm and event messages and PLC controller with Start/Stop sequence. - Tilting/Scissor lift table
For easy intake of bags from pallets at a suitable working height - Belt conveyor in various executions
Almost any desired type of belt conveyor can be fitted to the bag slitting unit for automatic bag in feed. Choice of belt conveyor type is subject to local situation, type of bag and desired working height. Belt width varies from 500 till 600 mm with a maximum elevation angle of approx. 35°. - Rotating-brush cleaning-unit
To prevent contamination of product when bags are used with dirt or dust on the outside, a rotating-brush cleaning-unit can be placed at the bag inlet of the “splitter” machine - Screw conveyor
For mechanical conveying of product after discharge - Rotating sieve or built-in vibrating screen
For removal of contaminants and lumps from product after discharge - Crusher / lump breaker
For breaking down lumps and agglomerates from product after discharge - Rotary blowing seal
A blowing seal can be fitted directly under the product hopper to accommodate pneumatic conveying of product after discharge - Bag compactor
A screw compactor can be fitted at the discharge chute of the machine. Bags are compacted and discharged into plastic bags secured to the outlet of the compactor - Automatic baling press
A baling press can be connected to the “splitter” by means of a closed discharge chute. Various configurations are possible. The bags are compacted to form a bale, automatically tied with annealed wire and pressed out of the baling unit. Length of the bale is adjustable. Flange connections are provided on the baling press for ducting to the dust filter on the “Splitter”.
Bag slitting machine with cleaning unit, bag compactor and enclosed belt conveyor
Special applications
|
Technical specifications | ||
Weight standard Galahad | : | 1000 kg |
Bag thickness | : | max. 250 mm |
Bag width adjustment range | : | 390-520 mm standard |
: | 360-620 mm optional | |
Rotating knife | : | hard chrome plated standard |
: | Tungsten Carbide coated optional | |
Conveying chain speed | : | 8 mtr./min standard |
: | 5 up to 18 mtr./min optional (depending on product) | |
Material execution | : | steel coated or stainless steel |
Drive | : | 0,75 kW bag transport |
: | 0,75 kW rotating knife | |
Chain tension | : | automatic and self-adjusting |
Inspection / maintenance | : | 4 access doors standard |
: | 6 access doors / 2 tilting ceiling doors optional | |
Safety features | : | safety switches on all access doors |
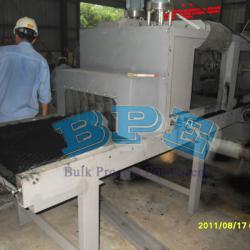
Packaging Detail:in bulk |
Delivery Detail:1 months after down deposit |