ASMR300 Sterilizing Tunnel for Ampoules and Vials(US FDA&EU cGMP Standard )
Place of Origin:Shanghai China (Mainland) | Brand Name:Rotech | Model Number:ASMR300 | Application:ampoules and vials |
Type:Drying Machine | After-sales Service Provided:Engineers available to service machinery overseas |
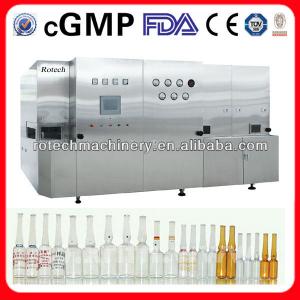
ASMR300 Sterilizing Tunnel for Ampoules and Vials
Design and Manufacturing According to FDA&cGMP Standard
Product Introduction:
The machine is design in tunnel structure, and it is divided into preheating segment, sterilizing segment and cooling segment, dry heating sterilizing principle is used for instantaneous high-temperature sterilizing process in container; it is suitable for drying and sterilizing for ampoules, antibiotic vial, oral medical liquid bottles as well as other medical glass bottle.
Advanced PLC and touch screen control system is used on the machine, operating conditions of the machine is monitored by touch screen, monitor and control is executed according to actual production and technical requirements, the sterilizing dryer can be used together with washing machine, filling& stoppering machine to indicate why does the fault occur, positions of faults and simple solutions, in addition, it can record temperatures and its curve diagrams automatically.
Working principle
ASMR300 circulating heated air sterilizing oven is applicable to dry ,sterilize, or de-pyrogen for glass container, especially in food or pharmaceutical productwhich requirements is very strict. The whole area which container go by is protected by hot air verticallaminar flow ( maximum temperature is 320°C) , the whole tunnel is protected by 100 c laminar flow so that prevent glass container from outside contamination
In heating section and cooling section ,Temperature is Changed with times go by, lowest Temperature in heating section is 320°C. sterilizing and de-pyrogen for 5minutes, the quantity ofpyrogen can reduce 3log.
The Tunnel is composed of 3 parts , the first part ispreheatingsection (LE ),second Part is heating section, Thirdly Part is cooling section ( LK ). Air pressure at LH is more than LE , air pressure at LK is about 5-10Pa ,whereas air pressure at LE and LK is 15Pamore than working room, these air pressuredistinction keepthe tunnel in 100c situation.
Preheating section
Preheating section (LE) is mainly composed of laminar flow case, blower, Approach switch and HEPA. After switch on the machine, the upper chamber of laminar flow case get the air in, the air is forced into the lower chamber of the laminar flow case , then the air go into HEPAand trun into clean air, and clean air blow to the containerto preheat them. thepreheating process can protect bottle from crack due tohightemperatature, the air flow at preheatingsectionis 0.5m/s , and its pressureis a bit of more than outside of the oven, so the air from outside can not go into oven to pullute the container .
Heating section
This section is the chief working area , glass container is heated and dried in this area. In heating section, the State under the HEPA is 100c, recirculating air speed is 0.6m/s in this state, and wind speed can be adjustable. Each part of the heating section equipped with static pressure chamber , air distributed uniformly. ventilation door monitors the airflowof the blower outlet in the laminar area.
Stainless steel tubular heater is used for heating air , and keepTemperature in balancing at heating section. ;Stainless steel generating chamber , 2 layers of cross Wall for warm keeping, leached fibre fill the cross Wall . ;Drain out the moisture from forward end of heating section . back and Forth of the heating section is Isolated by Stainless steel cross Wall from adjacent section, its height is adjusted by operator.
Use differential pressure meter to test pressure of the HEPA , and use temperature probes whitch fitted behind the HEPA to test and adjust theair Temperature in heating section . Control unit fit on control cabinet , and it controlthe heater , and Control unit monitor the min/max temperature. Each heating recorder is protected by overheating protection , and carry Out Heat interlocking for preheating section's blower and cooling section ' sblower , carry Out shut heating system. Only Temperature < 100°C , the whole electric circuit could cut Off. When Temperature too high , it cut Off the power of the heating system , and use the ventilation system exhaust system to cool it.
Set one temperature probes on Each heating area to regulate , Record and monitor min/max temperature. The state under HEPA is 100c, filter efficiency is 99.995%, and HEPA could bear 400°C. HEPA' Frame is made of Stainless steel, it can fit the filter even without bolt and screw, the HEPA is fitted and changed by lifting mechanism.
Cooling Section
Cooling section ' s structure is same as Preheatingsection , there isalso 100 c laminar flow to protect Cooling section. ,Primary function of the cooling sectionis cooling the glass container from heating section under protection of 100 c air , and reduce the glass container breaking rate due toshock cooling . Wind speedunder the HEPA in cooling sectionis 0.5m/s, wind speed is adjustable. Air in cooling section is distributedn uniformly, and ventilation door fitted on the outletof the blower monitors and controls the airflow
Advantages
1. Protection system
1) Poweroff protection , in heating section, set one device to protectairflow overspill in case of power cut , it is not necessary to connect the compressed air.
2) There isinterlocking device in control circuit, when the Temperature is less than 100°C, control system can cut-out power supply automaticly. When the Temperature is more than 100°C,all of the blower can not shut down , so the control circuit can protectthe preheating section and cooling section's HEPA.
3) Give an alarm in case of high temperature ,and automatic cut-out heating power supply
2. Electric control
1) Touch screen : heating, operation technological parameter and etc canbe automatic Record and printed, support wireless networks printer, and all kinds of printer that Support PCL language. 64MB ram,canstore 300000 pcs of data. There is USB on the touch screen, mouse or keyboardcan directly access Touch screen. Equipped with CF card interfacing , original data could be copy directly, and save data permanently. Without air Fan , without removable component. Modular design , there be no need for changing the whole Touch screen in case of damage.
2) Set 6 Temperature scan Points , one is situated preheating section , which is used for measuring preheating section's Temperature , if not normal Temperature (<100 ), machine show that wind over pressure at heating section . 2 Temperature scan Point situated heating section , these 2 point is set for keeping heating time after setting,At the same time ,2 Temperature scan Point situated at heating blower's inlet , these2 point is used for blower and HEPA protection in case of machine out of control . 1 Temperature scan Point situated cooling section, which is used for testingTemperature when bottle leaveing from oven.
Technique Information
Model | ASMR300 |
Conveyor effective width | 1200mm |
Maximum sterilizing temperature | 350°C |
container specification | cut vial or open-funnel vial:1-100ML,diameterφ8-φ54mm,height40-160mm or similar column containers Ampoules: 1ml-20ml |
sterilizing temperature | 320°C adjustable |
temperature at bottle outlet | ≤25°C(water cooling) |
water consumption | 3000-6000KG/H(temperature at inlet water should below 8°C,water cooling) |
Temperature at bottle outlet | ≤45°C(wind cooling) |
air displacement | 4100CMB/H |
power | 51KW,including 43KW for electrical heating |
cleanness | international 3 class(ANSI 100c) |
power cost by mechanical | 7.36KW |
power cost by heating | SS heating tube 0.8KW 220v×24PCS |
dimension | The size can be changes according to customers' requirement) |
Net weight | 3000KG(with electrical cabinet) |
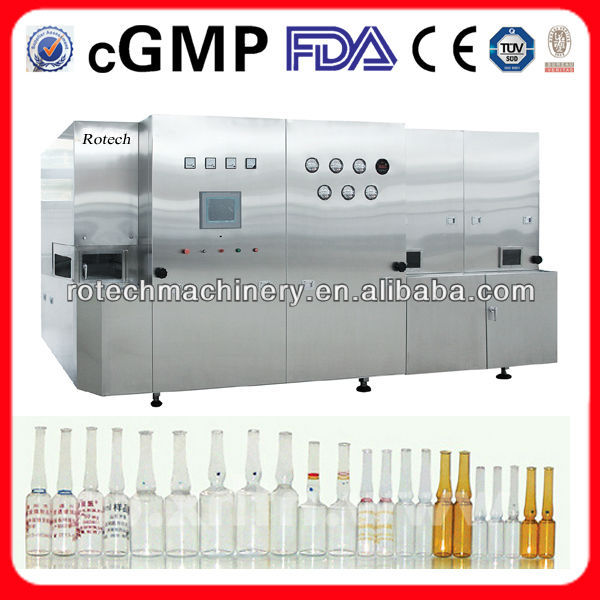
Packaging Detail:International Export Wooden Case Packing, Water Proof |
Delivery Detail:Delivery it in 2 month after received the downpayment |