Aluminium Alloy Wire Rod Casting and Rolling Machine CCR Line
Place of Origin:Sichuan China (Mainland) | Brand Name:141 | Model Number:UL+Z-1600+255/14 | usage:casting and hot rolling |

§ Equipment application
The aluminum alloy rod continuous casting and rolling machine is mainly used to produce ø9.5, ø12, ø15mm aluminum alloy rods and normal aluminum rod for electrical purpose.
§ Equipment composition
Melting Furnace, holding furnace, continuous casting machine, ingot pulling machine, rolling shear, straightener and edge shaver,online heater, rolling mill, oil lubrication systems, emulsion lubricating and cooling system, rod quenching device, rod orbital coiler, electric control system, etc.
§ Brief process flow
Ingot→melting→heat preservation(preparation for alloy composition)→casting→pulling→cutting scrap ingots→ straightening→heating→rolling→quenching and taking up→aluminum alloy rod
§ Technical Datas
1. Crystallizing wheel dia. ø1600 mm
2. Type of casting machine Integral casting machine with 4-wheel
3. Casting bar section 2300 mm2
4. Rolling type 2-roller & 3-roller
5. Rolling pass 2+12
6. Nominal size of rollers ø255mm
7. Outlet rod dia. ø9.5 ø12 ø15 mm
8. Finished rolling speed 9.7 m/s
9. Max. capacity 4.2 t/h
10. Main motor power 355 kw
11. Coiling dia. ø1200- ø2000 mm
12. Max. bundling weight 2.5 t
13. Total weight 800 kw
§ Electric control system
The main motor is in type of Siemens (produced in TianJin) or ABB (produced in Switzerland) DC fully-digital speed adjusting while other motors adopt frequency controlling. By adopting PLC and man-machine interface for the complete line control, it can check and display the running parameter of machines as well as indicate the breakdown.
§ Equipment characteristics
1. Crystallizing wheel is in type of “H”, and cooling on every side. External and side cooling is divided into 4 sections, and internal cooling is divided into six sections. Each section’s supplying for water is separately adjusted, and its pressure is also shown so that make ingots even cooled, grain refined, process with high adaptability.
2. The steel tension is pneumatic control that can be casted high quality ingot as the steel belt tension is invariable when it has been set up.
3. All the components are installed on the same body which is cast part in whole one that makes high rigidity, easy to install. Crystallizing wheel, transition wheels, and tension wheels ensure that the steel belt can not run in the same plane.
4. Casting point is just above the crystallizing wheel, to ensure level casting that protects turbulence so that the casting of molten aluminum alloy ingots without slag, porosity and loose, which can assure high quality aluminum alloy ingot in continuous casting.
5. According to the temperature characteristics of aluminum alloy rolling, rolling mill adopts two-roll & three-roll, taking advantage of large deformation of two rollers to increase spindle deformation in high temperature.
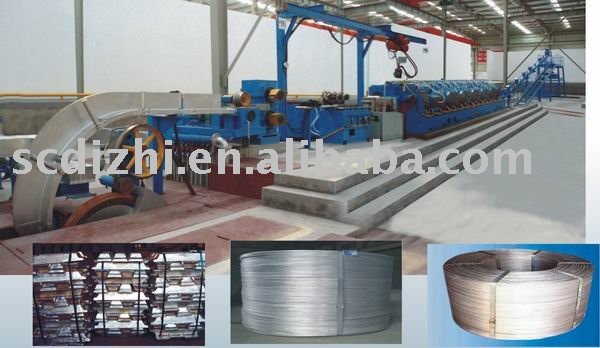
Packaging Detail:Most of the parts are naked in container, while some parts are put in container with plywood box. |
Delivery Detail:Within 70 days after receiving the 30% deposit |