AAC block plant
Condition:Used | Type:AAC block machine | Brick Raw Material:Sand | Processing:block production line |
Method:Autoclaved Aerated Concrete | Automatic:Yes | Capacity:50000~300000 | Place of Origin:Jiangsu China (Mainland) |
Brand Name:Duyuen | Model Number:JQF | Voltage:depend on clients condition | Power:380kw~1000kw |
Certification:ISO9001-2000 | Warranty:1 year |
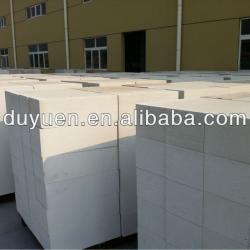
AAC Block Plant Technological Production
AAC block(Autocalved Aerated Concrete) is a light weight, multi-cell new construction material; the features include lower density, heat insulation, possibility, fire and acoustical resistant properties. AAC is made from silicon material( sand or recycled fly ash) and calcium material(lime, cement), mixing with foaming additive(aluminum powder), batching with water, the reaction between aluminum and concrete causes microscopic hydrogen bubbles to form, expanding the concrete to about five times its original volume, It is made into the multi-cell silicate product by the processes of molding, pre-curing, cutting, evaporating and curing.
Capacity Type
Item | AAC-5 | AAC-10 | AAC-15 | AAC-20 | AAC-30 |
Capacity,*103m3/year | 50 | 100 | 150 | 200 | 200 |
Cake size(m3) | 4.2*1.2*0.6 | 4.2*1.2*0.6 | 4.2*1.5*0.6 | 4.8*1.2*0.6 | 6*1.5*0.6 |
Installation power(kw) | 600 | 800 | 900 | 1300 | 1400 |
Production cycle(m2) | 5 | 6 | 6 | 6 | 6 |
Workshop area | 3000 | 3000 | 3500 | 4000 | 5000 |
Plant area | 20000 | 20000 | 25000 | 30000 | 35000 |
Technological process:
(1) First, batching the stored raw materials through measuring;
(2) After batching, pouring the raw materials into pouring mixer to make slurry;
(3) Through thoroughly mixing, the slurry is poured into mould;
(4) After pre-curing under a certain temperature and time, prepare for cutting until the block reach a certain hardness;
(5) Turning over the mould 90°in the air by tilting hoister;
(6) Then open the mould and separate the block from it. And hoist the block with side plate to the cutting car;
(7) Two sides of the blocks are cut vertically through the cutterbar firstly;
(8) Secondly the horizontal cutting;
(9) Finally the vertical cutting;
(10) After cutting, the block is sended to the autoclaved trolley with side plate by semi-product hoister;
(11) Organizing the cut blocks and put them into autoclaves;
(12) Hardening the blocks under a certain temperature and pressure;
(13) Taking finished products out of autoclaves;
(14) Stacking the finished products through final product jig;
(15) Loading after packing;
(16) Sending back the side plate through side plate roller table;
(17) Organizing the side plate with the open mould;
(18) Cleaning the mould and the side plate for next pouring;
(19) Steel bars processing line for slab production.
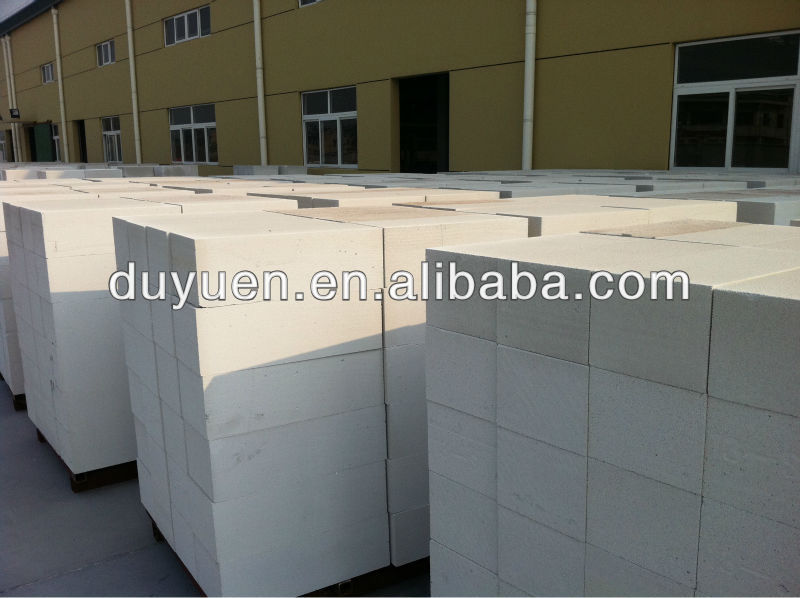
Packaging Detail:wooden |
Delivery Detail:3 months |