AAC/Auoclaved aerated concrete Blocks Production Line Plant
Condition:New | Type:Hollow Block Making Machine | Brick Raw Material:quarz sand,lime,cement,fly ash | Processing:Brick Production Line |
Method:Autoclaved Aerated Concrete | Automatic:Yes | Capacity:50000-300000CBM/year | Place of Origin:Jiangsu China (Mainland) |
Brand Name:Duyuen | Model Number:AAC-1 | Voltage:380V | Power:600-1400kw |
Certification:ISO9001-2000 | Warranty:1year | cake size:4.2m*1.2m*0.6m | Workshop area:3000-5000m2 |
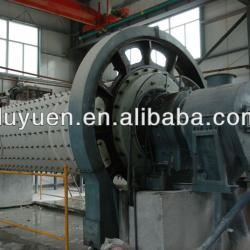
INTRODUCTION:
AAC is Autoclaved Aerated Concrete. The blocks are made to aerate by creating a reaction between silica in base material such as fly ash or sand, active lime, and aluminum power. The block hardness is being achieved by cement strength, and instant curing mechanism by autoclaving. Gypsum acts as a long term strength gainer.
The Duyuen Equipment Manufacturing Co., Ltd line from 50,000 CBM to 300,000 CBM includes the following items:
1. Production equipments and Technology of the AAC Blocks process.
2. Special lay out for your factory and One year equipment warranty.
3. Transfer of know-how with the training in your site.
4. Set up and installation in the customer facility.
ADVANTAGES:
The advantages are as follows:
1.Consumes Fly ash, which is a big problem for thermal power plants to dispose. It is environment friendly, because of no need of burning.
2. Higher strength, best thermal insulation & excellent sound absorption, vibration resistance compared to red bricks. The AAC product’s lightweight and easy workability means that is very quick to install on site and transportation with lesser brakeage.
3.AAC blocks made walls can be left exposed (without Plaster) and gains strength over time. It saves structural cost by 35% and recycling of breakage, rejects also.
4. AAC products are not affected by harsh climatic conditions and will not degrade under normal atmospheric conditions.
5. AAC Block does not have any toxic substances or emit odors. Its production, management and disposal do not represent any health risks or damage to the environment. Its production process develops non-toxic gases.
6. AAC blocks are bigger in size then conventional bricks, resulting in lesser number of joints. Less joints result in lesser quantity of mortar required, resulting in saving of mortar.
TECHNICAL COMPARISON:
PARTICULARS | CONVENTIONAL RED BRICKS | FLYASH BRICKS |
Strength | 40 – 65 Kg/cm2 | 70 – 120 Kg/cm2 |
Shape & Size | Non Uniform & Irregular | Uniform & Regular |
Water Absorption | 20 – 25 % | 10 – 15 % |
Breakage / Wastage | 8 – 10 % | 3 – 4 % |
Mortar Consumption | High | Less |
Density | 1500 – 1700 Kg/cm3 | 1200 – 1350 Kg/cm3 |
Nos. of Bricks for100 sq.ft. wall of 9” thick | 1100 Nos | 925 Nos. |
Mortar Joint Thickness | 15 – 18 mm | 8 – 10 mm |
Plaster Thickness | 15 – 20 mm | 10 – 12 mm |
REMARKS:
1.Terms of payment: | 30% down payment, 70% before container loading. |
2.Lead time: | 2 months |
3.Container: | about 14pcs 40’containers |
4.Package uses: | large goods bulk packing, small goods and electric control parts have wooden box packing. |
5.After-sales service | One year free service after successful installation. |
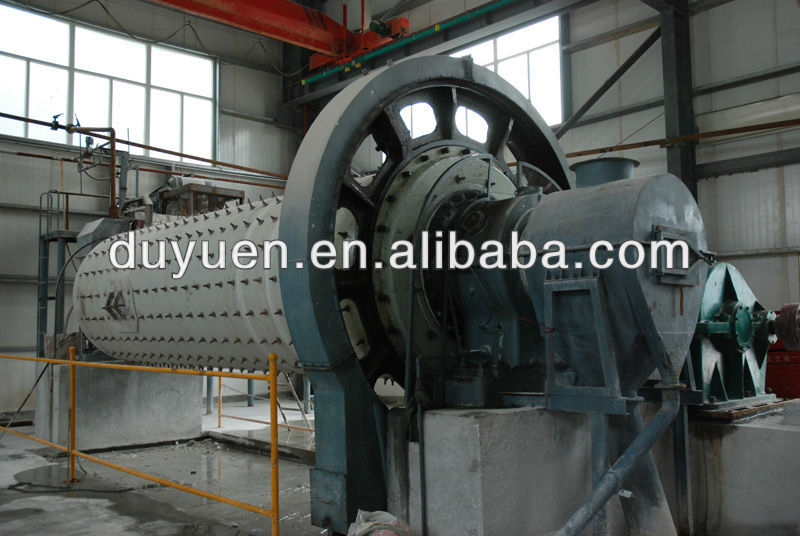
Packaging Detail:Direct container packing. It will be delivered upto your site in the containers. Complete care is taken in packaging to be completely damage free. It has Fourteen 40 feet cointainers. It is sent via shipment through sea. |
Delivery Detail:45 work days after receiving deposit |