50,000~600,000m3/Year AAC Autoclaved Aerated Concrete Block/Panel Production Line
Condition:New | Type:Light Weight Block | Brick Raw Material:Fly Ash | Processing:Brick Production Line |
Method:Hydraulic Pressure | Automatic:Yes | Capacity:20,000-300,000m3/year | Place of Origin:Shanghai China (Mainland) |
Brand Name:Qianyu | Model Number:AAC | Voltage:As Per Local Condition | Power:450kw |
Dimension(L*W*H):6050*1540*650mm | Certification:GB/T 19001-2008/ISO 9001:2008 | Warranty:One Year | After-sales Service Provided:Engineers available to service machinery overseas |
Advantage:German Technology | Installation:Engineer Guidance |
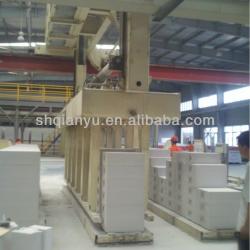
About Shanhai Qianyu:
Qianyu Heavy Industrial Machinery Co., Ltd. is a qualified manufacturer of new buliding material machineries, especially of lightweight aac autoclaved aerated concrete block and panel making machine plant with reasonable prices.
QR Code
Basic Introduction:
Autoclaved Aerated Concrete (AAC) is a siliceous material (sand, fly ash and silicon tailings such as waste porcelain clay, stone processing waste materials, blast furnace slag, etc.) and calcareous materials (lime, cement) as the main raw material, mixing fat gas agent (aluminum powder), by ingredients, mixing, casting, pre-raising, cutting, autoclave, curing process made of light porous silicate products, because by the hair contains a lot of gas even after the small pores, hence the name of aerated concrete.
AAC Production Process
Advantage of AAC:
- Lightweight: Porosity achieve 70% to 85%, volume density is generally 500 ~ 900kg/m3, as 1/5 of general concrete the 1/4of clay, the 1/3 of hollow brick, and similar with wood can float in water. It can reduce building weight, reduction in the cost of integrated building.
- Fireproof: Most of the major raw materials is inorganic materials, so it has good fire resistance, and do not emit harmful gases when meet fire. Fire 650 degrees, as a refractory material, the thick up of 90mm walls can reach to 245 minutes fire resistance, 300mm thick up wall can reach to 520 minutes fire resistance.
- Sound insulation: Due to a unique porous structure, so it has a sound absorption capacity. The sound absorption capacity can reach of 10mm thick wall up to 41 db.
- Insulation: As the material inside has a large numbers of the pores and porous, which has a good thermal insulation properties. The Thermal conductivity is 0.11-0.16W/MK, as 1/4-1/5 of brick. Typically, the insulation effect of 20cm thick aerated concrete wall is equivalent to 49cm thick solid brick walls ordinary.
- Permeability: Result of material by the composition of many independent small pores, the moisture absorption is slow, in the volume of absorbent is 5 times of clay saturation do. When used in the bathroom, the wall can be treated to interface directly paste tiles.
- Anti-seismic:The same building structure, improve the two seismic than the brick level.
- Green: Manufacturing, transportation, all use the process of pollution, to protect arable land, saving energy, is one kind of a green building material.
- Durability: material strength is stability, in the specimens tested after one year of atmospheric exposure; the intensity increased by 25%, and remained stable after ten years.
- Shortcut: it has good machinability, can be sawed, planed, drilled, nailed, and available appropriate as bonding of adhesive material, so create favorable conditions for building construction.
- Economies: An integrated lower cost than using more than 5% of solid clay bricks, and can increase the usable area, greatly enhance the utilization of floor space.
Samples:
Requirements for Raw Materials:
Main Equipments in AAC Production Line:
- Material-milling Equipments:
a.Crusher: Lime, gypsum, and such kind of bulk material need to be crushed as the first step in AAC Plant.
b. Miller: The AAC material must be fully grinded in order to make better reaction. Ball Mill is used widely, it has two types: dry and wet, can be chosen upon requirement.
- Material Metering Equipments:Computer Control Automatic Metering System is commonly used as measurement of raw materials.
- Material mixing and casting equipments:Mixer, it’s the slurry mixing machine, also is slurry casting machine.
- Cutting Machine:the AAC blank is formed after castingand pre-curing, as the size is too large, it must be cut to achieve the required product size.
- Autoclave:Autoclave is a device for silicate hydration products to get physical and mechanical properties.
- Boiler:the boiler supports for the autoclave and pre-heat furnace and other facilities with heat.
- Auxiliary Equipments:
a. Mould Frame, Mould Bottom and Mould Car, they composed together to form the Casting Mould, which is the main forming equipments in AAC Production Line.
b. Hardening Car, Ferry Cart and Hangers, they must be equipped as auxiliary equipments in autoclave curing system.
Production Flow:
Office and Workshop:
Customers:
Contact Information:
Ms. Evelyn Zhu
- Telephone: 86-021-37591139
- Mobile Phone: 8613611676896
- Email: evelyn"at"cnqianyu.cn
- Skype: bailingocean
- MSN: evelyn_blingzhu"at"hotmail.com
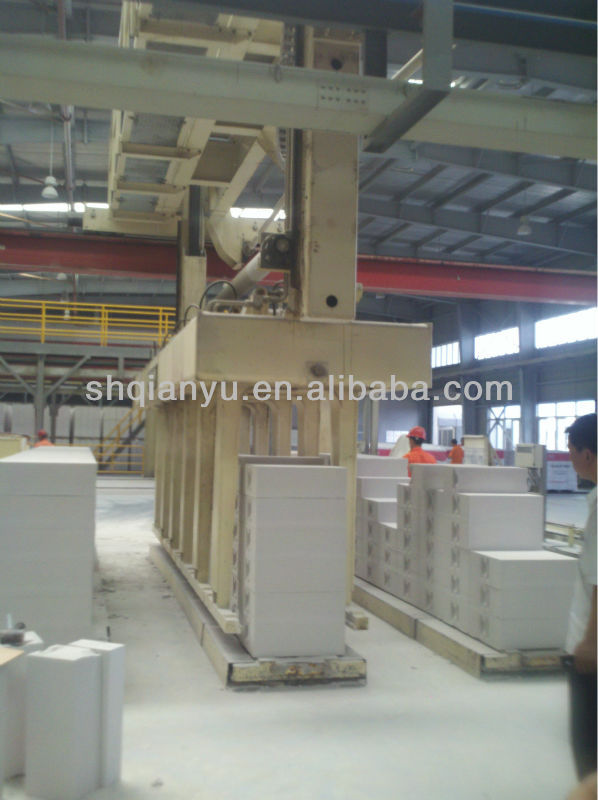
Packaging Detail:Export Standard |
Delivery Detail:60 days |