300TPD Cement Plant (Rotary Kiln)
Condition:New | Production Capacity:95% | Place of Origin:Henan China (Mainland) | Brand Name:Winner |
Model Number:300TPD | Voltage:380v | Certification:ISO9001:2008 | Warranty:1year |
After-sales Service Provided:Engineers available to service machinery overseas |
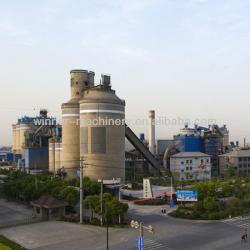
We are specialised in cement production lin emore than 50years. Main equipment: limestone crusher, raw mill, rotary kiln, cement mill, raw mill and cement mill general wound asynchronous motors, power of thousands of kilowatts process, crushing and pre-homogenization (1 ) a crushing cement production process, most of the raw materials to be broken, such as limestone, clay, iron ore and coal, etc.. Limestone to produce the maximum amount of cement raw materials, larger particle size, high hardness after mining limestone crushing occupies a more important position in the cement plant materials broken. (2) raw material pre-homogenizing pre-equalization technology is in the retention of the raw materials, to take the process to use the scientific stacker reclaimer technology, raw materials are initially raw material yard along with storage and homogenization function. 2, raw material preparation process of cement production, each producing 1 ton of Portland cement to be grinding at least 3 tons of materials (including all kinds of raw materials, fuel, clinker, mixed materials, gypsum), according to statistics, the dry process cement production line powder The mill operating power consumption accounts for about 60% of the power of the whole plant, which accounted for 30% of the raw material grinding, accounting for about 3% of coal mill, cement grinding about 40%. Therefore, a reasonable choice of grinding equipment and process optimization of process parameters, the correct operation, and control of the operating system, is of great significance to ensure product quality, reduce energy consumption. 3, raw material homogenizing dry cement production process, stable pit entry of raw material composition is a prerequisite for stable clinker fired thermal system, raw material homogenization system plays stable Rujiao raw material ingredients last a gatekeeper role . 4, preheat the decomposition of the preheating of the raw material and partially decomposed by the preheater to complete, instead of some of the features of rotary kiln, to shorten the length of the back kiln while the kiln gas the expected heat exchanger process stacked state, moved to pre- within the heater under the suspended state, so that the raw material can be discharged with the kiln hot gases sufficiently mixed, increase the contact area of the gas feed, fast heat transfer, heat exchange efficiency is high, to achieve the goal of improving the kiln system production efficiency, reducing the clinker firing heat consumption purposes. (1) The material dispersion heat exchanger 80% in inlet pipe. Raw material in the feed preheater pipe in the updraft and high-speed impact of material folded steering on with the air movement, while being dispersed. (2) gas-solid separation when the airflow carrying the feed powder into the cyclone cylinder and forced in the annular space between the cyclone barrel and the inner cylinder (exhaust pipe) rotating flow, and the downward movement while rotating, from the cylinder to the cone, has been extended to the end portion of the cone, and then turned on the rotation rising from the exhaust pipe. (3) pre-decomposition precalciner technology appear cement calcination process of a technological leap. It is between the preheater and the rotary kiln additional decomposition of the furnace and the utilization of kiln inlet rise flue, provided that the fuel is injected into the device, so that decomposition of the endothermic process of fuel combustion in an exothermic process and raw materials carbonate in the decomposition furnace quickly suspended state or fluidized state, the decomposition of the kiln feed rate increased to 90% or more. Moved exploded original carbonate decomposition of tasks carried out in a rotary kiln, furnace; the fuel most Precalciner Add small part by Yaotou Add, reducing the thermal load of the kiln with, extending liner material life, is conducive to large-scale production; mixed fuel and raw material, fuel burning heat timely passed to the materials, combustion, heat exchangers, and carbonate decomposition process has been optimized. Quality, high efficiency, low power consumption, and thus has a range of excellent performance and features. 4 after the completion of preheating of the firing of the raw material of the cement clinker in the cyclone preheater and precalciner, a next step is to enter the rotary kiln, clinker calcination. Carbonate in the rotary kiln further rapid decomposition and a series of solid-phase reaction to produce cement clinker, and other minerals. With the temperature of material near, and other minerals will become liquid, dissolved in the liquid phase and the reaction was carried out to generate a large number of (clinker). Clinker after baking, the temperature began to decrease. Hot clinker rotary kiln will be unloaded by the cement clinker cooler cooling to the downstream conveyor, storage libraries and cement mill can withstand temperature, while recovery of the sensible heat of the hot clinker to improve the thermal efficiency and clinker quality. 5, cement grinding, cement grinding is the last of the cement manufacturing process, and also a power-up processes. Its main function is to cement clinker (and gelling agent, performance tuning materials, etc.) grinding to appropriate particle size (fineness, specific surface area), the formation of a certain particle size distribution, increasing its hydration area, accelerate the hydration rate, to meet cement paste condensation, hardening requirements. 6, both bagged and bulk cement packing cement factory shipping way.
Warehouse
Processing capacity
If you send E-mail to us we will appreciate it very much
Welcome to our factory for investigation and negotation
Jiaozuo Winner Machinery Co., Ltd
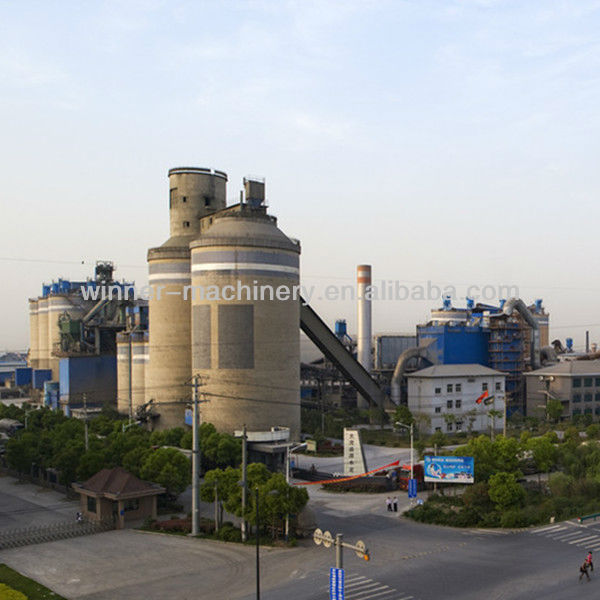
Packaging Detail:Big machine with nude packing, small parts packen in wooden box. |
Delivery Detail:100days |