200 gallon moonshine copper stills for sale
Processing:Fermenting Equipment,liquid | Condition:New | Place of Origin:ZHE,Zhejiang, China (Mainland) China (Mainland) | Brand Name:DY |
Model Number:DYZL-001 | Processing Types:Alcohol | Voltage:240V | Power(W):3HP |
Dimension(L*W*H):According to the requirement | Weight:200kg-2000KG | Certification:CE,ISO9001,PED,SGS | Warranty:one years |
After-sales Service Provided:Engineers available to service machinery overseas | material:copper and stainless steel | Volume:20-500gallon | Price:Factory Price |
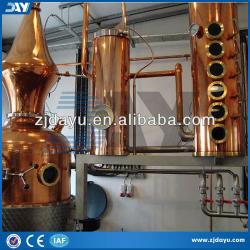
200 gallon moonshine copper stills for sale
Distillation unit with batch capacity of 10 HL
DISCONTINUOUS DISTILLATION UNIT for fermented grapes and other fruits - working with indirect steam at max. 0,5 bar.
The unit is composed of:
- An alembic in stainless steel and copper with a working capacity of 10 hl, equipped with a slow revolving stirrer driven by a geared motor with motor of 1,1 kW, manhole for product loading, butterfly valve for exhausted product discharge, show-glass on top dome and on plating, connections for probes, insulated and coated double wall for steam heating, steam inlet connection, air breathing connection with relevant discharging device, pressure gauge, connection for condensate discharge complete with discharging device The alembic has the copper top dome equipped with lit show-glass, and it’s equipped with an external cyclone separation device, made in stainless steel, which separates from the steams the possible foam draggings, and with a spray ball device for the washing. It’s moreover equipped with: a cast iron valve for steam regulation with servo control; two PT 100 probes for temperature survey.
All connections are equipped for application of Excise seals.
- Device for absorption of possible traces of sulphur dioxide that there could be in the alcoholic steams; it’s a copper cylindrical container having the flanged ends, suited to contain inert material, and equipped with 2 show-glasses, copper pipes complete with motorized three-way valve and two-way valve to exclude the device from the alcoholic steams circuit.
- Copper enrichment column with 8 plates, made in copper with stainless steel boiler and reflux condenser on the top. Equipped with n°2 lit show-glasses (one of which is placed on the 8th plate, while the other is between the 2nd and the 3rd plates), connections complete with probes for temperature survey, flow-meter showing the water quantity going into the reflux condenser, motorized ball valve regulating the condensation water, pump for reflux condensation water circulation, heating system placed at the column bottom with manual regulation valve and condensate discharging device. Each plate is equipped with discharge valve connected to a manifold, that can be used to split the plates and to wash the column.
The connections are equipped for application of Excise seals.
- Vertical column complete with the different connections for application of Excise seals, composed of:
- Alcoholic steams condenser: it’s a copper coil heat exchanger having adequate section and surface, put into a stainless steel cylindrical container with flanged ends and connection complete with probe.
- Coolant: it’s a copper coil heat exchanger having adequate section and surface, put into a stainless steel cylindrical container with flanged ends and connection complete with probe, placed under the condenser.
- Flow-meter and motorized valve ON - OFF for interception of the water intended for the coolant and the condenser.
- A container for collecting the head portions: cylindrical shape, made in stainless steel, equipped with show-glass, n° 2 motorized interception valves ON - OFF for cutting and discharging of heads, glass container complete with float for cutting the heads by volumetric control, forming a structure element of the column and placed under the coolant. The container is intended for receiving from the condenser the head portions that one decides to draw.
- A container for collecting the tail portions: cylindrical shape, made in stainless steel, equipped with show-glass, motorized interception valve ON - OFF for cutting the tails, photocell for cutting the tails by alcoholic content control, forming a structure element of the column and placed under the heads container. The container is intended for receiving the tail portions that one decides to separate from “good taste”.
· Piping's made in copper and AISI 304 stainless steel for the connections of the various components to the outlet of “good-taste” distillate.
· Automatic system for regulation and control of the main phases of the process: it allows to set and display the temperatures of dealcoholisation, condensation and reflux, the interventions for cutting the head and tail portions in relation to volume and alcoholic content, and the end of cycle intervention in relation to the temperature and to the alcoholic exhaustion.
· Control board: stainless steel box with protection IP 55, in which the following electric components are assembled and wired:
¨ blockage switch,
¨ geared motor control,
¨ control of condensation water recycle pump,
¨ control of head cut valve
¨ control of tail cut valve
¨ control of alembic steam valve
¨ control of reflux water valve
¨ control of cooler water valve
¨ warning lights,
¨ set of digital thermoregulators for displaying and regulating the following temperatures:
* alembic alcoholic steams temperature
* bain-marie temperature
* boiler temperature
* pre-reflux temperature
* post-reflux temperature
* distillate temperature at condenser outlet
* distillate temperature at coolant outlet
* water temperature in reflux condenser.
EXCLUSIONS:
* Pipes for discharging of exhausted still-slops.
* Draining wells.
* Excise measurer.
* Electric motors and control boards with anti-explosion protection.
* Steam lines with pressure reducer.
* Steam boiler.
* Condensate pipes.
* Water pipes.
* Distillate pipes.
* Safety valve and condensate discharging device in the steam lines.
* Electrical wiring to the control board and to the users.
* Masonry and all that has not been mentioned.
DESCRIPTION : UNIT - VALUE
Raw material production capacity per cycle : litres 1,000
Total time each cycle : hours 2.5 / 3.5
Maximum percentage of solids in the liquid to be distilled : % 50
Maximum recommended alcoholic content of the raw material to be distilled : vol. % 10 / 12
Maximum steam pressure : bar 0.5
Steam working pressure : bar 0.2 / 0.5
Counter pressure allowed on the condensate discharge : bar 0
Steam consumption during the heating phase : kg / h 120 / 140
Duration of the heating phase (from 20 to 93° C ) : hours 0.45 / 1
Steam consumption during the distilling phase : kg / h 50 / 80
Duration of the distilling phase : hours 1.5 / 3
Consumption of cooling water at 15° C for each cycle : litres 2,000 / 3,500
Maximum instantaneous flow rate of cooling water : l / h 2,000
Recommended pressure of cooling water : bar 0.5
Mean temperature of water leaving the condensers : ° C 60 / 70
Consumption of washing water for each cycle : litres 80 / 150
Instantaneous flow rate of washing water : l / h 7,000
Pressure of washing water : bar 2 / 3
Load of calcium carbonate for the reactor filter : kg 70
Dimensions of electric panel (wall fixture) : mm 500 x 700 x 250
Installed electric power : kW 2
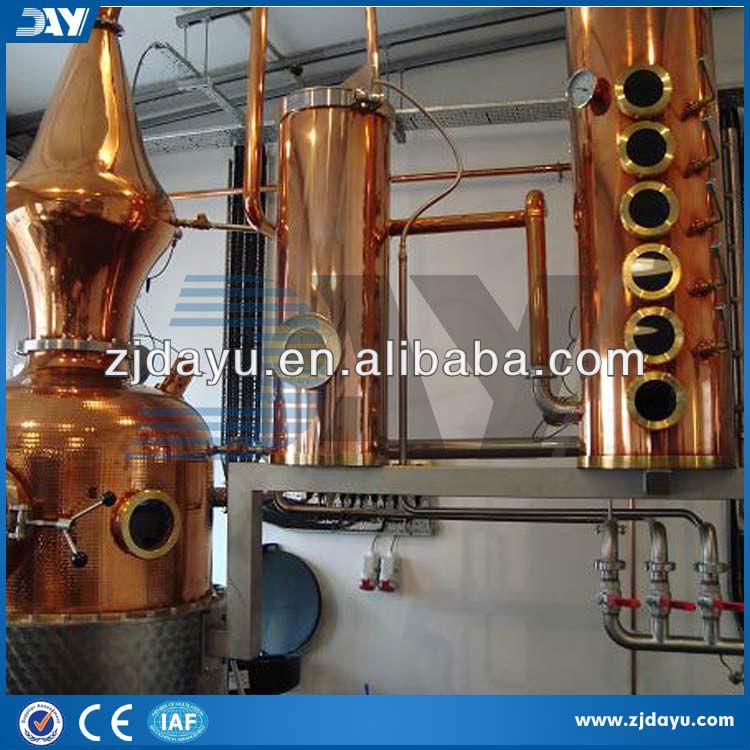
Packaging Detail:Wooden Case,Standard export packing |
Delivery Detail:45days |