2 phase 1-4A current 20-50v M542 stepper motor driver
1. High performance, low price, 2 voltage 18V-50VDC., 3 For neam23 and nema17 motor, 4 less than 4.2A current, 5 300g weight - details see: https://www.machineto.com/2-phase-1-4a-current-20-50v-m542-stepper-motor-driver-10234669
Place of Origin:Zhejiang China (Mainland) | Brand Name:LEISON | Model Number:M542 | Motor Type:Stepper Motor |
Stepper Motor Driver:Stepper Motor Driver |
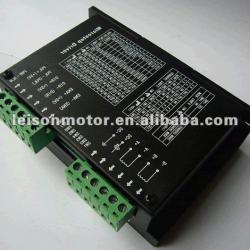
stepper motor driver:
Introduction:
M542MA is a type of two-phase hybrid stepping motor driver, the drive voltage of it is from
18VDCto50VDC. It is designed for use with 2-phase hybrid stepper motor of all kinds with
42mm to 86mmoutsidediameter and less than 4.0A phase current. This circuit that it adopts
is smiliar to the circuitof servocontrol which enables the motor run smoothly almost without
noise and vibration. Holdingtorque when M542MA run under high speed is also significantly
higher than the other two-phasedriver, what’s more,the positioning accuracy is also higher.
It is widely used in middle and big sizenumerical control devicessuch as curving machine,
CNC machine, and computer embroider machine,packing machines and so on.
Features:
l High performance, low price
l Average current control, 2-phase sinusoidal output current drive
l Supply voltage from 18VDC to 50VDC
l Opto-isolated signal I/O
l Overvoltage, under voltage, overcurrent, phase short circuit protection
l 15 channels subdivision and automatic idle-current reduction
l 8 channels output phase current setting
l Offline command input terminal
l Motor torque is related to speed, but not related to step/revolution
l High start speed
l High hording torque under high speed
Electrical specification:
Input voltage | 18-50VDC |
Input current | < 4A |
Output current | 1.0A~4.2A |
Consumption | Consumption:80W; Internal Insurance:6A |
Temperature | Working Temperature -10~45°C; Stocking temperature -40°C~70°C |
Humidity | No condensation, no water droplets |
gas | Prohibition of combustible gases and conductive dust |
weight | 300G |
Function choice ( Using DIP pins to achieve this function)
1) Micro step resolution is set by SW 5,6,7,8 of the DIP switch as shown in the following table:
SW5 | OFF | ON | OFF | ON | OFF | ON | OFF | ON | OFF | ON | OFF | ON | OFF | ON | OFF |
SW6 | ON | OFF | OFF | ON | ON | OFF | OFF | ON | ON | OFF | OFF | ON | ON | OFF | OFF |
SW7 | ON | ON | ON | OFF | OFF | OFF | OFF | ON | ON | ON | ON | OFF | OFF | OFF | OFF |
SW8 | ON | ON | ON | ON | ON | ON | ON | OFF | OFF | OFF | OFF | OFF | OFF | OFF | OFF |
PULSE/REV | 400 | 800 | 1600 | 3200 | 6400 | 12800 | 25600 | 1000 | 2000 | 4000 | 5000 | 8000 | 10000 | 20000 | 25000 |
2Closest to your motor’s required current
Output current (A) | ||||
SW1 | SW2 | SW3 | PEAK | RMS |
ON | ON | ON | 1.00 | 0.71 |
OFF | ON | ON | 1.46 | 1.04 |
ON | OFF | ON | 1.91 | 1.36 |
OFF | OFF | ON | 2.37 | 1.69 |
ON | ON | OFF | 2.84 | 2.03 |
OFF | ON | OFF | 3.31 | 2.36 |
ON | OFF | OFF | 3.76 | 2.69 |
OFF | OFF | OFF | 4.20 | 3.00 |
Pins of motor & power:
Motor and power pins | 1 | A+ | Motors wiring | |
2 | A- | |||
3 | B+ | |||
4 | B- | |||
5,6 | DC+ DC- | Power supply | Power supply :DC18-50VDC |
Mechanical Specification:
Driver wiring
A complete stepper motor control system should contain stepper drives,
A complete stepper motor control system should contain stepper drives,
DC power supply and controller (pulse source). The following is a typical
system wiring diagram
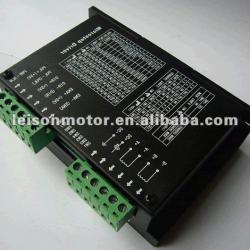
Packaging Detail:Standard Export Cartons |
Delivery Detail:Within 10 Days |