Vacuum Cooler for Vegetables(0.5Ton~12Ton/20mins)
Type:Vacuum cooler | Place of Origin:Guangdong China (Mainland) | Brand Name:COLDMAX | Model Number:KMS-3000 |
Certification:CE,TUV | After-sales Service Provided:Engineers available to service machinery overseas | Voltage:AC380V/3P/50Hz | Cooling Type:Air/Water/Evaporative Cooling |
Cooling Capability(kw):270KW | Total Power:120KW |
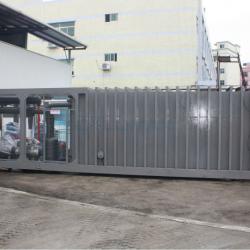
Vacuum Cooler Application
Vacuum cooling is still one of the best ways to protect your fresh produce from degradation in its first hours after harvest. Getting your product cool quickly is the best way to ensure longer shelf life and freshness for your customers.
As well as fresh produce the flower industry is gaining from vacuum cooling, with many importers/exporters demanding the process prior to flying, many of them using coolers capable of eight tonnes!
Advantage of vacuum cooling/cooler:
a. Largely keep freshness and nutrition;
b.Prolong preservation time and shelf-life;
c.Fast cooling speed and average cooling, 20~30mins each cycle;
d.Restrain and kill bacteria and animalcule, no introduced pollution;
e.Wate lost rate is about 2 to 3% of total goods weight, no localized wilting.
Structure of vacuum cooler
Vacuum cooing system or vacuum cooler is composed of four main parts.
a. Vacuum chamber
Vacuum chamber is the spaces for fitting pallets of produce and track conveyor system. According to practical application, the space could be manufactured from 1 pallet to 16 pallets or more. Vacuum chamber should sustain the big pressure from outside when decompressed, so it is normally made of steel to ensure enough intension.
b. Vacuum system
Vacuum system take away air from vacuum chamber at desired speed (m3/s) according to actual application. In the vacuum system, vacuum pumps are the main parts. Vacuum pump will affect the water evaporation speed inside chamber. Before vapor in chamber saturated, faster water evaporated, faster produce temperature reduce.
c. Refrigeration system
Refrigeration system is composed of compressor, expansion, dry filter, liquid receiver, oil separator, gas separator, pipes, etc. Refrigeration system will condense vapor to liquid water to ensure vapor in chamber will not saturate. If vapor saturated in chamber, the water on produce will not evaporate any more. That means, no water evaporation, no temperature reduce.
d. Control system
All above three systems works well coordinated by control system including temperature control, pressure control, high-low pressure control, compressor control, loading control, remote control, etc. Control system is the central part of whole machine which is always special made according to different applications.
Main parameters of KMS-3000 vacuum cooler:
NO. | Name | Model | Remarks |
1 | Volume of the vacuum chamber | 23.4 m³ | W1800*L5000*H2600mm |
2 | Weight of treatment per cycle | 2500-3000kg | |
3 | Processing time per cycle | 20~30min | |
4 | Cooling capacity | 270kw | 232000kcal/h |
5 | Total power | 120kw | |
6 | Compressor power | 93kw | Hanbell RC2-470B-Z 1 set |
7 | Vacuum power | 22.5kw | Rietschle VC303 3 sets |
8 | Power requirements | 3P-380V-50Hz | |
9 | Weight | 14500kg | |
10 | Overall dimensions | L12000×W2200×H2900mm | |
11 | Ultimate vacuum | ≤600Pa | |
12 | Target temperature | 0~15°C |
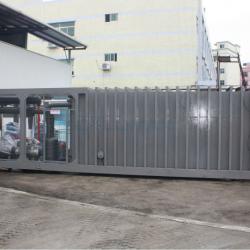
Packaging Detail:40HQ Container. |
Delivery Detail:30 days after order confirmed |