Silicon Carbide/SiC/Foam Filter for Iron Casting/INNOVACERA
Place of Origin:Fujian China (Mainland) | Brand Name:INNOVACERA | Model Number:INVFF023 | Materials:Al2O3, ZrO2, SiC |
Pore Per Inch:10-60 ppi | Shapes:Square, Rectangle, Round, Tube | Applications:Aluminium, Steel and Iron Casting |
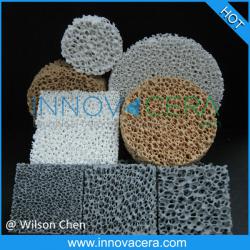
Silicon Carbide/SiC/Foam Filter for Iron Casting/INNOVACERA
Keywords:
Ceramic Foam Filters for Foundry
Foundry Ceramic Filters
Ceramic Foam Filters for Metal Casting
Steel Casting Ceramic Foam Filters
Alumina Ceramic Foam Filters
SiC Ceramic Foam Filters
Silicon Carbide Foam Filter
Zirconia Ceramic Foam Filters
Ceramic Foam Filter Plate
Aluminium Ceramic Foam Filter
Metal Foam Filter
1. Introduction
Ceramic foam filtershave the advantages of high prorosity, low loss of thermal shock, high mechanical strength at normal and high temperature, large specific surface, good chemical stability and excellent filtering functions of screen, filtering residum collection and absorption especially for tiny impurity of 1~10um.
The three-dimension structure can improve the cast quality in large scale by changing the molten metal from turbulence flow to lamellar flow, removing the gas and smoothing the casting.
It is not only applied for molten metal filtering in high temperature, but gas treatment in high temperature,carrier of catalyzer, solid heat exchange and advanced filling for chemical industry.
With more than ten years of scientific research and development, INNOVACERA has developed a series of ceramic foam filters which are made of different materials such as Aumina, Silicon Carbide and Zirconia.
1) Alumina Ceramic Foam Filters
Alumina Ceramic Foam Filters mainly for filtration of aluminium and aluminium alloys in foundries and cast houses. Cleaner metal results in higher-quality castings, less scrap, and fewer inclusion defects, all of which contribute to bottom-line profit.
2) Zirconia Ceramic Foam Filters
Zirconia Ceramic Foam Filters are used for molten all types of steel like unalloyed, low alloyed, stainless and high-alloyed as well as Nickel and Cobalt-based super-alloys.
3)Silicon Carbide Ceramic Foam Filters
Silicon Carbide Ceramic Foam Filters mainly for filtration of cast iron and non-ferrous alloys.
3. Material Specifications
Material | ZrO2 | SiC | Al2O3 |
Colour | Yellow | Grey Black | white |
Pore density (ppi) | 10~60 | 10~60 | 10~60 |
Porosity (%) | 80~90 | 80~90 | 80~90 |
Operating temperature(°C) | 1700 | 1500 | 1100 |
Compression Strength(MPa) | 1.2 | 0.9 | 0.8 |
Density(g/cm3) | 0.90-1.50 | 0.35-0.50 | 0.30-0.45 |
Thermal Shock Resistance(1100-20°C) | >6 times | >6 times | >6 times |
Application | steel | iron | Non-Ferrous Alloy and Aluminium |
4. Pore Density (PPI = Pore Per Inch)
5. Pouring Rate and Filtration Capacity
1) Alumina Ceramic Foam Filters
Dimensions(mm) | Dimensions(inch) | Pouring Rate(kg/s) | Filtration Capacity(ton) |
178x178x50 | 7x7x2 | 0.2-0.6 | 5 |
228x228x50 | 9x9x2 | 0.3-1.0 | 10 |
305x305x50 | 12x12x2 | 0.8-2.5 | 15 |
381x381x50 | 15x15x2 | 2.2-4.5 | 25 |
430x430x50 | 17x17x2 | 3.0-5.5 | 35 |
508x508x50 | 20x20x2 | 4.0-6.5 | 45 |
585x585x50 | 23x23x2 | 5.0-8.6 | 60 |
2) Zirconia Ceramic Foam Filters
Dimensions(mm) | Pouring Rate(kg/s) | Filtration Capacity(kg) |
50x50x22 | 3-5 | 30 |
50x75x22 | 4-6 | 40 |
75x75x22 | 7-12 | 60 |
75x100x22 | 8-15 | 80 |
100x100x22 | 14-20 | 100 |
D50x22 | 2-6 | 18 |
D80x22 | 6-10 | 50 |
D90x22 | 8-16 | 70 |
3) Silicon Carbide Ceramic Foam Filters
Dimensions (mm) | Pouring Rate(kg/s) | Filtration Capacity(ton) | ||
Grey Iron | Ductile Iron | Grey Iron | Ductile Iron | |
40x40x22 | 4 | 3 | 65 | 32 |
50x50x22 | 6 | 4 | 100 | 52 |
75x50x22 | 9 | 6 | 150 | 75 |
75x75x22 | 14 | 9 | 220 | 100 |
100x50x22 | 12 | 8 | 200 | 100 |
100x75x22 | 18 | 12 | 300 | 150 |
100x100x22 | 25 | 16 | 400 | 200 |
150x150x22 | 50 | 36 | 900 | 450 |
6. Usage of Ceramic Foam Filters
7. Storage Condition
Store in a dry and well-ventilated place, keep out of rain and heavy weights.
8. Quality Control/Assurance Standard:
We are ISO certified: ISO9001:2008 ISO14001:2004 OHSAS18001:1999
The constant goal of Innovacera is a superior level of quality and sevice at competitive prices. Particular attention is given to the production of individual customer parts for both large and small runs. We implement a very sophisticated Quality Control process which we have our own customers certify. All parts that pass through our facility are visually and dimensionally inspected as well as calibrated. Our engineering staff is available for counsel and recommendations that will satisfy your ceramic requirements.
9. Packing:
10.Other Products for Foundry/Casting:
1) Mullite Ceramic Pouring Cups (plz check more details about this product in our site)
2) Boron Nitride (ZSBN: BN+ZrO2>99%) Ceramic Transfer Nozzle for Molten Liquid
Superior quality of products with reliance is our prime consideration.
Feel free to contact us if you need any other assistance about our products.
We care and provide what you want!
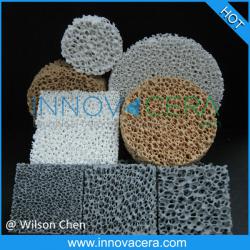
Packaging Detail:Export Carton / Wooden Box / Pallet |
Delivery Detail:15 days after payment |